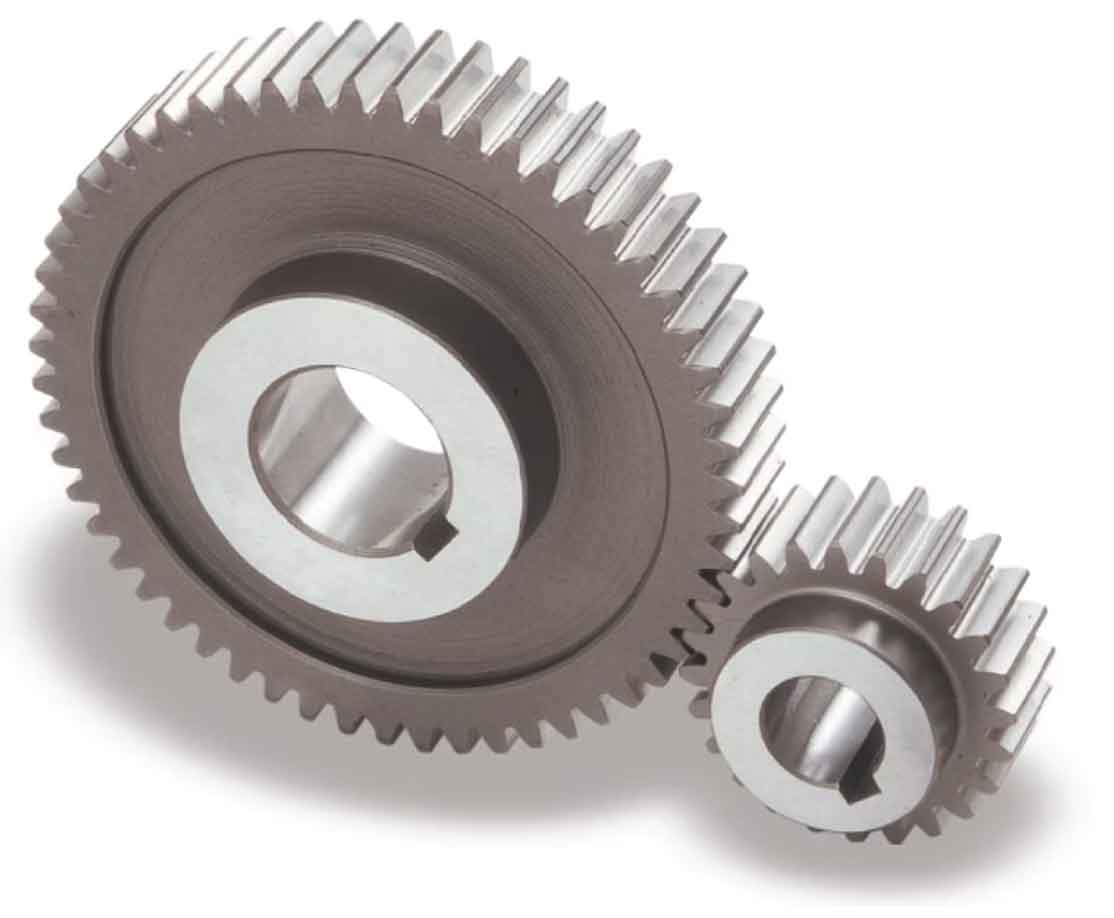
Spur gear manufacturing has witnessed significant innovations and advancements over the years, leading to improved efficiency, precision, and quality in gear production. These advancements have been driven by advancements in technology, manufacturing processes, and materials. Here are some key innovations and advancements in spur gear manufacturing:
1. Computer-Aided Design (CAD) and Computer-Aided Manufacturing (CAM):
The widespread use of CAD and CAM software has revolutionized spur gear manufacturing. These tools enable engineers to design complex gear geometries with high precision and simulate gear meshing behavior before production. CAM software aids in generating tool paths and optimizing manufacturing processes, resulting in improved efficiency and accuracy in gear production.
2. High-Precision Machining Techniques:
Advancements in machining techniques have improved the accuracy and surface finish of spur gears. High-precision machining processes such as CNC (Computer Numerical Control) milling, grinding, and hobbing allow for tight tolerances and precise tooth profiles. These techniques ensure consistent gear quality and reduce the need for post-machining operations.
3. Gear Hobbing and Shaping Machines:
Hobbing and shaping machines have undergone significant advancements in terms of accuracy, automation, and flexibility. Modern gear hobbing machines can produce spur gears with complex profiles, helical gears, and even custom gear shapes. Advanced controls and automation features have enhanced productivity and reduced setup times.
4. Gear Grinding and Finishing:
Gear grinding processes have improved significantly, allowing for higher precision and surface finish. The use of CNC-controlled grinding machines with advanced grinding wheels and abrasive technologies enables precise gear tooth profiles and surface quality. Gear grinding ensures accurate tooth geometry and low noise levels in the final gear products.
5. Heat Treatment Techniques:
Heat treatment processes have seen advancements in controlling the hardness, case depth, and microstructure of gear materials. Advanced techniques such as induction hardening and vacuum carburizing provide precise and consistent heat treatment results, enhancing gear strength and wear resistance.
6. Material Innovations:
New materials and alloys with improved strength, wear resistance, and fatigue properties have been developed for spur gear manufacturing. Advanced steel alloys, powder metallurgy techniques, and composite materials are being utilized to produce gears with enhanced performance and durability.
7. Inspection and Quality Control:
Non-destructive testing methods, such as laser scanning and coordinate measuring machines (CMMs), have made gear inspection more accurate and efficient. These technologies enable the measurement and verification of gear dimensions, tooth profiles, and surface finishes, ensuring high-quality gear products.
8. Automation and Robotics:
Automation and robotics have been introduced in gear manufacturing processes to enhance productivity and reduce human errors. Robotic systems can handle tasks such as loading and unloading gears, gear inspection, and even gear measurement and sorting. Automated systems improve efficiency and consistency in gear production.
These innovations and advancements in spur gear manufacturing have led to higher production efficiency, improved gear quality, and the ability to produce complex gear geometries with tight tolerances. As a result, industries can benefit from higher-performing and more reliable spur gears that meet their specific application requirements.