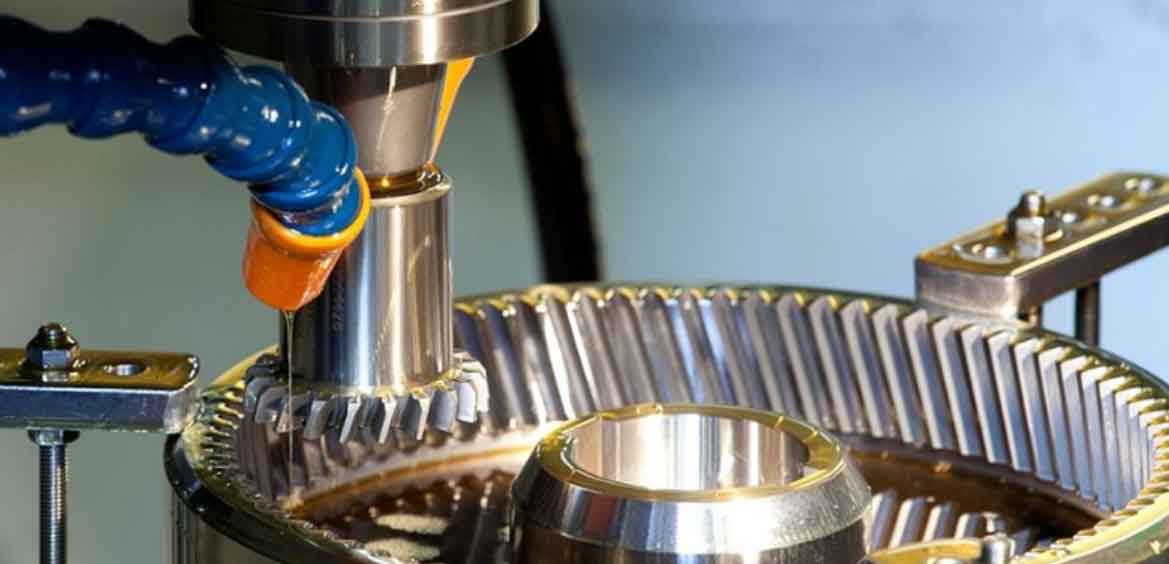
Gear shaping is a fundamental process in gear manufacturing that involves the precise cutting of gear teeth using a shaper cutter. The process of gear shaping can be summarized in the following steps:
- Gear Blank Preparation: Start by preparing the gear blank, which is the workpiece that will be shaped into a gear. The gear blank should be properly machined, ensuring accurate dimensions and surface finish.
- Tool Selection: Choose a suitable shaper cutter based on the gear specifications, such as tooth profile, module, pressure angle, and number of teeth. The shaper cutter is a specialized cutting tool with the desired tooth profile.
- Machine Setup: Set up the gear shaping machine by installing the shaper cutter and securing the gear blank onto the machine’s workholding device or fixture. Ensure that the machine is properly aligned and adjusted for the desired gear specifications.
- Cutting Parameters: Determine the cutting parameters, including cutting speed, feed rate, and depth of cut, based on the material properties, gear design, and machine capabilities. These parameters affect the cutting efficiency and quality of the gear teeth.
- Gear Shaping Process: Start the gear shaping process by engaging the shaper cutter with the gear blank. The shaper cutter reciprocates vertically while the gear blank rotates, gradually cutting the gear teeth. The precise motion of the cutter generates the desired tooth profile on the gear.
- Coolant and Lubrication: Use cutting fluids or lubricants to cool the cutting area, reduce friction, and prolong the life of the shaper cutter. Proper coolant and lubrication help maintain the cutting efficiency and improve surface finish.
- Quality Control: Throughout the gear shaping process, perform regular inspections and measurements to ensure the gear’s dimensional accuracy, tooth profile, and surface finish. This may involve using measuring instruments such as micrometers, gear checkers, or coordinate measuring machines (CMMs).
- Post-Processing Operations: After gear shaping, the gears may undergo additional operations for finishing, such as gear grinding, honing, or heat treatment, depending on the desired gear quality and performance.
- Final Inspection and Quality Assurance: Conduct a final inspection to verify that the shaped gears meet the required specifications. This includes checking tooth profile accuracy, runout, surface finish, and other critical dimensions.
- Packaging and Storage: Once the gears pass the quality inspection, they are packaged and prepared for shipment or storage, ensuring proper protection and identification.
It is essential to follow proper safety guidelines, adhere to the machine manufacturer’s instructions, and continuously monitor the gear shaping process to ensure optimal results. Experienced operators, accurate tooling, and effective quality control measures are vital for achieving high-quality gears through gear shaping.