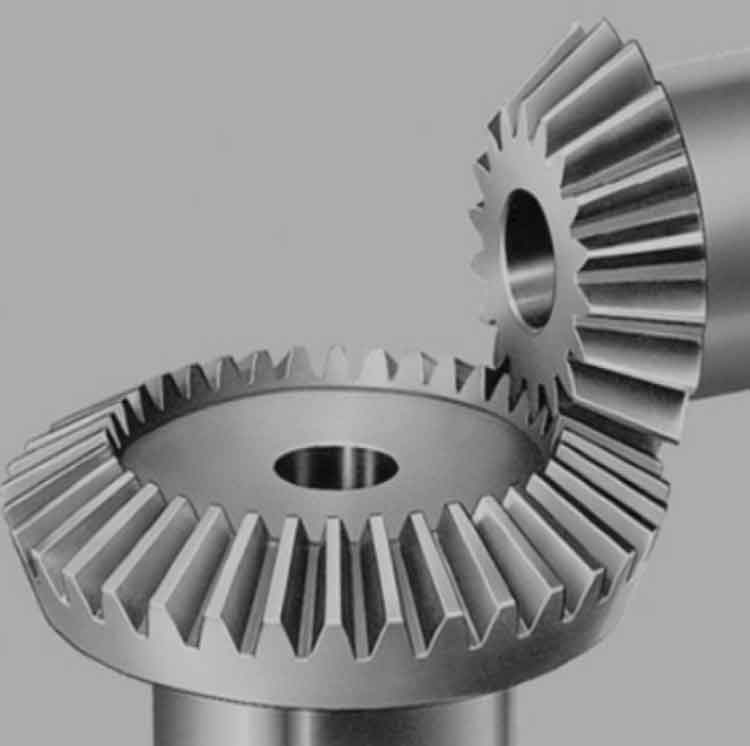
Straight bevel gears play a significant role in aerospace technology, where they are utilized in various critical applications. Advancements in materials, design, and manufacturing processes have improved the performance of straight bevel gears in aerospace applications. However, several challenges still need to be addressed to further enhance their efficiency and reliability. Here are some advancements and challenges associated with straight bevel gears in aerospace technology:
Advancements:
- Material Innovations: Aerospace gear manufacturers are continuously exploring advanced materials, such as high-strength alloys and composites, to improve gear performance. These materials offer enhanced strength-to-weight ratios, improved wear resistance, and higher fatigue life, critical factors in aerospace applications.
- Advanced Manufacturing Techniques: Advancements in manufacturing technologies, such as computer numerical control (CNC) machining, precision grinding, and 3D printing, have allowed the production of complex and highly accurate straight bevel gears. These techniques ensure precise gear tooth profiles, reducing gear noise and increasing efficiency.
- Gear Design Optimization: Advanced computer-aided design (CAD) software and simulation tools enable engineers to optimize gear designs for specific aerospace applications. Finite element analysis (FEA) and computational fluid dynamics (CFD) simulations help assess gear performance under varying operating conditions, leading to improved gear geometries.
- Gear Surface Treatments: Aerospace gear manufacturers employ advanced surface treatments, such as shot peening, carburizing, nitriding, and coating processes, to improve gear hardness, wear resistance, and fatigue life.
- Tribology and Lubrication: Research in tribology and lubrication has led to the development of specialized lubricants and coatings, reducing friction and wear between mating gear surfaces.
- Reduced Weight and Noise: Advancements in gear design and material selection contribute to lighter gear components and quieter gear operations, which are crucial in aerospace applications.
Challenges:
- High Load and Fatigue Requirements: Aerospace gears often encounter high loads and experience repetitive cyclic stresses, necessitating a careful selection of materials and heat treatment processes to ensure long-term durability.
- Tolerance and Precision Requirements: Aerospace applications demand tight tolerances and precise gear tooth profiles to maintain smooth meshing and minimize gear noise and vibration. Achieving such high precision during manufacturing can be challenging.
- Space Constraints: Aerospace gearboxes and drivetrains often operate in confined spaces within aircraft, requiring compact gear designs and optimization of space utilization.
- Temperature Extremes: Aerospace environments experience a wide range of temperature fluctuations. Gear materials and lubricants must withstand extreme temperature conditions without compromising performance.
- Safety and Reliability: Aerospace systems require an exceptionally high level of reliability to ensure passenger safety. Gear failures can have severe consequences, making material selection, gear design, and manufacturing processes critical considerations.
- Environmental Regulations: Aerospace manufacturers must comply with stringent environmental regulations related to material usage, waste management, and emissions.
To address these challenges and capitalize on advancements, ongoing research and collaboration among gear designers, materials scientists, and aerospace engineers are essential. By continuously innovating and optimizing gear technology, straight bevel gears will continue to play a vital role in driving advancements in aerospace technology while ensuring safety, efficiency, and reliability.