Abstract
In the process of gear shaping, the unbalanced inertia force generated by the unbalanced dynamic motion of the main motion mechanism of the gear shaping machine causes vibration and noise of the machine tool. Therefore, by conducting a balance analysis of the main motion mechanism of the gear shaping machine, calculating the total unbalanced mass of the crank pin and connecting rod during one revolution of the crank, and adopting two optimization calculation methods, integral solution and mean value solution, with mean square deviation as the evaluation index, an optimization strategy is formulated. The balance optimization example calculation of the main motion mechanism of the YKW51160 gear shaping machine shows that the unbalanced masses calculated by the integral optimization method and the mean value optimization method are similar, with a difference not exceeding 0.2 kg·m. The mean square deviation of the unbalanced mass after integral optimization is 0.614, with less fluctuation and better vibration reduction effect.
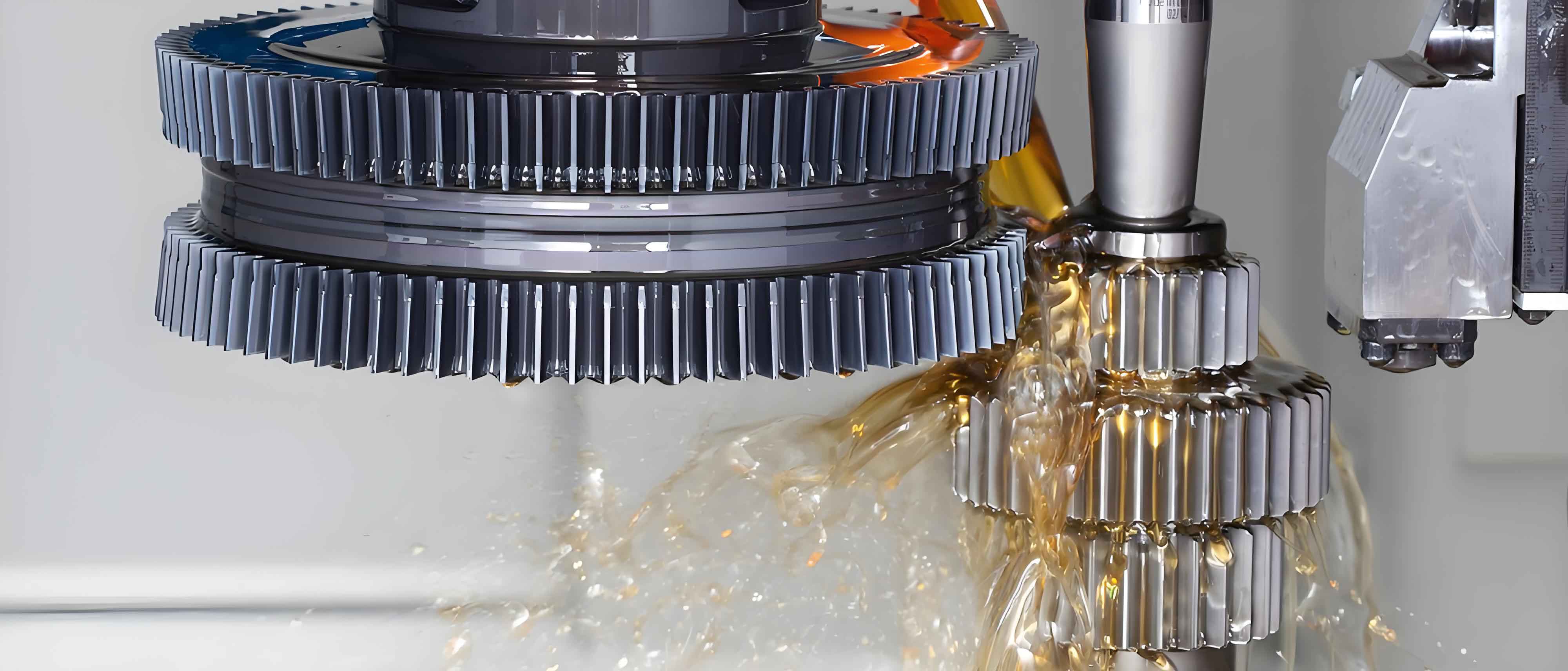
1. Introduction
The main motion mechanism of high-speed gear shaping machines adopts a crank-slider mechanism. During the gear shaping process, the crank-slider mechanism simultaneously undergoes high-speed rotational and reciprocating motion. If the center of mass of the moving parts does not coincide with the center of rotation, inertia forces, etc., will be generated, resulting in unbalanced motion, which in turn causes vibration, noise, or reduces the life of the machine tool. Many scholars at home and abroad have conducted research on the dynamic balance of mechanisms.
This paper focuses on the dynamic balance problem of the main motion mechanism of gear shaping machines, combining mechanism dynamics theory, dynamic balance theory, dynamic balance optimization methods, and optimization evaluation indicators to form a complete set of dynamic balance optimization strategies for the main motion mechanism of gear shaping machines.
Table 1: Key Research on Mechanism Dynamic Balance
Scholar | Research Content | Methodology | Contribution |
---|---|---|---|
Lu Yang | Dynamic balance of high-speed press sliders | Centrifugal inertia force balance method | Accurate calculation of dynamic balance slider mass and stroke |
Guo Ruiqin | Balancing the oscillating force of planar linkage mechanisms | Mass moment balance of two-pair components | Construction of complete balancing conditions for oscillating forces of general planar mechanisms |
Liu Jun | Dynamic balance analysis of engine crankshafts | Improved crankshaft center hole processing technology and drilling weight reduction method | Realization of dynamic balance |
Hou Longtao | Dynamic balance optimization of aero-engine rotors | Four-point balancing method | Optimization for rotors with dynamic imbalance due to processing, assembly, or operation |
Kochev I S | Evaluation indicators for balancing mechanism oscillating forces and oscillating moments | Proposed evaluation indicators | – |
Nehemiah P | Balancing mechanism oscillating forces | Mass redistribution method and inertia counterweight method | – |
2. Dynamic Balance Analysis of the Main Motion Mechanism of Gear Shaping Machines
The motion process of gear shaping machines is divided into five types: main motion, generating motion, circumferential feed motion, radial feed motion, and tool retraction motion. Among them, the main motion involves the reciprocating up-and-down motion of the gear shaping cutter as it follows the spindle to perform gear cutting on the workpiece. The reciprocating stroke motion of the gear shaping machine spindle is achieved through the crank-slider mechanism driven by an AC variable-frequency motor. For gear cutting processing of large tooth width gears, the stroke of the main motion is long, which requires adjusting the crank lever length of the crank-slider mechanism to achieve the processing function.
2.1 Mechanical Structure of the Main Motion
Taking the YKW51160 long-stroke CNC gear shaping machine as an example, the main motion mechanism’s mechanical structure is shown in Figure 1. The spindle connected to the drive motor serves as the driving member, and its rotational motion is converted into linear motion through the crank-slider mechanism. The connecting rod is connected to the reciprocating slider through a spherical joint. To accommodate the need for processing gears of different tooth widths, a screw nut structure is used to adjust the working radius of the crank.
Figure 1: Mechanical Structure of the Main Motion of the YKW51160 Gear Shaping Machine
(Insert an image here representing the mechanical structure)
3. Dynamic Balance Optimization Methods for the Main Motion Mechanism of Gear Shaping Machines
3.1 Time-Varying Unbalanced Mass of the Mechanism
The relevant structural parameters of the dynamic balance of the main motion mechanism of the CNC gear shaping machine YKW51160 are shown in Table 2. Taking the crank angle θ as the driving variable, the time-varying unbalanced mass U of the connecting rod and crank pin over one cycle is calculated (Figure 5). The calculation result of the unbalanced mass component U1 along the OB direction is shown in Figure 6. When the crank angle is 0°, the gear shaping cutter strokes to the lower protruding position of the workpiece, and U and U1 are maximum at 12.81 kg·m; at an angle of 180°, both are minimum.
Table 2: Structural Parameters of the YKW51160
Parameter | Value |
---|---|
k | 0.1 |
n | 128 |
Figure 5: Calculation of Time-Varying Unbalanced Mass
(Insert an image here representing the calculation)
Figure 6: Unbalanced Mass Component U1
(Insert an image here representing the unbalanced mass component)
3.2 Optimization Methods
3.2.1 Integral Optimization Method
Through MATLAB programming, when the unbalanced mass of the balance block is 10.7 kg·m, the optimal solution min is 0.144 kg·m. The integral optimization process is shown in Figure 9.
Figure 9: Integral Optimization Process
(Insert an image here representing the integral optimization process)
3.2.2 Mean Value Optimization Method
The mean value optimization method takes the average of the maximum and minimum values of the unbalanced mass U of the connecting rod and crank pin over one cycle as the unbalanced mass Up of the balance block, Up = (Umin + Umax) / 2 = 10.8. A comparison of the unbalanced masses optimized by the integral optimization method and the mean value optimization method is shown in Figure 10. The optimization results of the integral optimization method and the mean value optimization method are similar.
Figure 10: Comparison of Optimization Results
(Insert an image here representing the optimization results comparison)
Table 3: Comparison of Optimization Results
Evaluation Indicator | Integral Optimization Method | Mean Value Optimization Method |
---|---|---|
Minimum Unbalanced Mass Us | Value | Value |
Maximum Unbalanced Mass Us | Value | Value |
Average Unbalanced Mass Us | Value | Value |
Mean Square Deviation | 0.614 | – |
4. Conclusion
- During one revolution of the crank in the main motion mechanism of the gear shaping machine, the maximum and minimum unbalanced masses of the connecting rod and crank pin occur at crank angles of 0° and 180°, respectively, and the unbalanced mass component along the crank direction accounts for a larger proportion.
- The integral optimization method was studied and applied to the dynamic balance structural optimization of the main motion of the gear shaping machine. The optimization results of the integral optimization method and the mean value optimization method are similar. Therefore, it is feasible to apply the integral optimization method to mechanism dynamic balance optimization.
- By combining mechanism dynamics theory, dynamic balance theory, optimization methods, and optimization evaluation indicators, a complete set of dynamic balance optimization strategies for the main motion mechanism of gear shaping machines is formed. The optimization strategy accurately calculates the unbalanced mass of the balance block, thereby reducing vibration and noise in the main motion mechanism, and provides an engineering feasible solution to the problem of dynamic imbalance in the main motion mechanism of gear shaping machines.
The comprehensive strategy for optimizing the dynamic balance of the main motion mechanism of gear shaping machines, highlighting the importance of precise calculations and the application of optimization methods to reduce vibration and noise, ultimately enhancing the performance and lifespan of gear shaping machines in industrial applications.