This article focuses on the performance analysis and test verification of the spiral bevel gear transmission system. Firstly, the mechanical models of key components in the system are established, including the equivalent models of the transmission shaft, gear pair, and bearing. Then, the static characteristics of the system are analyzed, such as the meshing misalignment amount, loading contact characteristics, and the comparison with different models. Next, the dynamic characteristics are studied, including the construction of the dynamic model considering meshing stiffness, modal analysis, and harmonic response analysis. After that, the test experiment is carried out using a CNC rolling inspection machine, and the experimental results are compared with the theoretical analysis results. Finally, the full text is summarized, and the future research directions are prospected.
1. Introduction
1.1 Research Background and Significance
Spiral bevel gears play a crucial role in various fields due to their excellent transmission performance. However, in the actual operation of the transmission system, the meshing state of the gear pair is affected by the load deformation of the system, which in turn affects the transmission performance. Therefore, it is of great significance to conduct in-depth research on the performance analysis of the spiral bevel gear transmission system to ensure the stable and efficient operation of various industries and improve the reliability and durability of the transmission system.
1.2 Research Status at Home and Abroad
- Meshing Misalignment Research: Scholars have studied various methods to analyze the meshing misalignment of the spiral bevel gear transmission system, but there are still some problems, such as inaccurate calculation or high resource consumption.
- Dynamic Analysis Research: The dynamic analysis methods of the transmission system have their own advantages and limitations. Combining the finite element method and the lumped parameter method is a potential research direction.
- Gear Transmission System Test Bench Research: A lot of research has been done on the gear transmission system test bench, which provides a theoretical basis and technical support for the performance test of the gear transmission system.
1.3 Research Contents and Methods
- Research Contents: This article mainly includes the establishment of the mechanical model of the key components of the spiral bevel gear transmission system, the analysis of the static and dynamic characteristics of the system, and the test verification of the system performance.
- Research Methods: The finite element method is used to establish the analysis model of the transmission system, and the experimental method is used to verify the accuracy and effectiveness of the theoretical analysis results.
2. Mechanical Model Building of Key Components in the Spiral Bevel Gear Transmission System
2.1 Transmission Shaft Model
- Entity Finite Element Model: The transmission shaft is simplified and divided into different regions for meshing. The bearing installation region and gear installation region have higher mesh density to ensure calculation accuracy, while the remaining regions use a sparser mesh to reduce computational resources.
- Beam Element Model: Considering the characteristics of the transmission shaft, the Timoshenko beam element is selected. The stiffness matrix of the two-node beam element is derived, and the multi-node beam unit model is established by superimposing the stiffness matrices of each two-node beam unit.
2.2 Gear Pair Model
- Equivalent Meshing Force: The meshing force of the gear pair is calculated by considering the torque or power, and the meshing force is translated to the axis according to the parallel theorem, taking into account the influence of the offset distance.
- Equivalent Rigid Body Model: The meshing stiffness of the gear is equivalent to a spring model, and the gear is regarded as a rigid disk with a certain moment of inertia to improve the analysis efficiency. The moment of inertia of the gear is calculated according to its geometric shape.
2.3 Bearing Model
- Structure and Force Analysis: The structure of the tapered roller bearing is analyzed, and the force and deformation of the bearing under load are studied. The contact load and deformation relationship of the bearing are derived, and the comprehensive stiffness coefficient is calculated.
- Stiffness Matrix Calculation: Based on the force and deformation analysis of the bearing, the six-degree-of-freedom stiffness matrix of the bearing is established by considering the nonlinear relationship between the contact load and deformation and the coupling phenomenon between the stiffness in different directions.
2.4 Summary
In this chapter, the mechanical models of the key components of the spiral bevel gear transmission system are established, which lays a foundation for the subsequent analysis of the static and dynamic characteristics of the system. The equivalent models of the transmission shaft, gear pair, and bearing are obtained through theoretical analysis and calculation, which can effectively simulate the mechanical behavior of the components in the transmission system.
3. Static Characteristics Analysis of the Spiral Bevel Gear Transmission System
3.1 Meshing Misalignment Calculation
The meshing misalignment of the gear pair is defined, and its calculation formula is derived. The meshing misalignment is calculated by analyzing the deformation of the transmission shaft and the gear under load, which is an important parameter affecting the transmission performance of the gear pair.
3.2 Analysis Model of the Spiral Bevel Gear Transmission System Based on the Solid Finite Element Method
- Transmission Shaft Coupling Analysis Model: The solid finite element model of the transmission shaft is established, and the grid is divided reasonably. The static analysis steps are defined, including material definition, analysis step settings, constraint settings, result output settings, and load definition.
- Loading Contact Analysis Model Considering Meshing Misalignment: The theoretical model of the spiral bevel gear is constructed by deriving the tooth surface equation. The meshing misalignment is considered to adjust the meshing position and posture of the gear, and the loading contact analysis model is established. The meshing characteristics of the gear pair are analyzed by using the static analysis method.
3.3 Example Analysis and Result Comparison
- Model Building: The spiral bevel gear transmission system of a passenger car drive axle is selected as the research object, and the basic parameters of the gear pair are given. The meshing force and bending moment of the gear pair are calculated, and the stiffness matrices of the bearings in the transmission system are calculated.
- Result Analysis: The displacement deformation diagrams of the transmission shaft of different models are obtained, and the meshing misalignment amounts of different models are calculated and compared. The loading indentation and transmission error of different models are analyzed and compared. The calculation time and accuracy of different models are compared and analyzed.
3.4 Summary
In this chapter, the static characteristics of the spiral bevel gear transmission system are analyzed. The meshing misalignment amount of the gear pair is calculated, and the loading contact characteristics of the gear pair are studied. The analysis model based on the solid finite element method is established, and the accuracy and effectiveness of the model are verified by comparing with other models.
4. Dynamic Characteristics Analysis of the Spiral Bevel Gear Transmission System
4.1 Dynamic Model of the Spiral Bevel Gear Transmission System Considering Meshing Stiffness
The dynamic model of the spiral bevel gear transmission system considering meshing stiffness is established. The meshing stiffness of the gear pair is calculated, and the dynamic model of the transmission system is constructed by combining the mechanical models of the transmission shaft, gear pair, and bearing.
4.2 Modal Analysis of the Spiral Bevel Gear Transmission System
The modal analysis of the spiral bevel gear transmission system is carried out. The first 20 natural frequencies and vibration modes of the transmission system are obtained, and the vibration characteristics of the transmission system are analyzed.
4.3 Harmonic Response Analysis of the Spiral Bevel Gear Transmission System
The harmonic response analysis of the spiral bevel gear transmission system is carried out. The dynamic response of the transmission system under the excitation of the meshing force is obtained, and the vibration acceleration amplitude-frequency characteristic curve of the transmission system is analyzed. The resonance phenomenon of the transmission system is studied, and the optimization direction of the transmission system structure is proposed.
4.4 Summary
In this chapter, the dynamic characteristics of the spiral bevel gear transmission system are analyzed. The dynamic model of the transmission system considering meshing stiffness is established, and the modal analysis and harmonic response analysis of the transmission system are carried out. The dynamic response characteristics of the transmission system are obtained, and the resonance phenomenon of the transmission system is studied.
5. Test Experiment
5.1 Experimental Preparation
- Experimental Object: The theoretical working surface indentation and transmission error are preset, and the gear pair sample is obtained by adjusting the machining parameters of the gear.
- Experimental Scheme: The gear pair is installed and adjusted, and the acceleration sensor and microphone are installed. The experimental data is collected and processed by using the LabShop software.
- Experimental Equipment: The experimental equipment used in the test experiment is introduced, including the CNC rolling inspection machine, acceleration sensor, microphone, and data acquisition card.
5.2 Experimental Results
- Static Characteristic Experimental Results: The static characteristic experimental results of the spiral bevel gear pair are obtained, including the contact indentation of the large wheel convex surface, the transmission error of the gear pair, and the light-load transmission error order amplitude of the gear pair. The experimental results are compared with the theoretical results and the analysis results of the finite element model.
- Dynamic Characteristic Experimental Results: The dynamic characteristic experimental results of the spiral bevel gear pair are obtained, including the vibration acceleration amplitude-frequency characteristic curves of the two spindles and the meshing noise amplitude-frequency characteristic curve. The experimental results are compared with the theoretical results and the analysis results of the dynamic model.
5.3 Scheme Optimization
The optimization scheme of the gear pair is proposed to improve the contact characteristics and reduce the vibration and noise of the transmission system. The optimized gear pair is tested experimentally, and the experimental results show that the optimization scheme is effective.
5.4 Summary
In this chapter, the test experiment of the spiral bevel gear transmission system is carried out. The experimental results verify the accuracy and effectiveness of the theoretical analysis method and the dynamic model of the transmission system. The optimization scheme of the gear pair is proposed and verified experimentally, which provides a reference for the design and optimization of the spiral bevel gear transmission system.
6. Conclusion and Outlook
6.1 Research Conclusions
- The mechanical models of the key components of the spiral bevel gear transmission system are established, which provides a theoretical basis for the performance analysis of the transmission system.
- The static and dynamic characteristics of the spiral bevel gear transmission system are analyzed, and the analysis methods and models are verified by experimental results.
- The test experiment of the spiral bevel gear transmission system is carried out, and the experimental results are in good agreement with the theoretical analysis results, which verifies the accuracy and effectiveness of the theoretical analysis method and the dynamic model of the transmission system.
6.2 Research Prospects
- In the future research, the accuracy of the calculation of the meshing misalignment of the transmission system can be improved by increasing the number of meshing force nodes on the contact trace.
- The influence of time-varying stiffness on the dynamic characteristics of the transmission system can be further studied to improve the accuracy of the analysis results.
- Other dynamic indicators can be considered in the dynamic characteristics analysis of the transmission system to improve the performance of the transmission system.
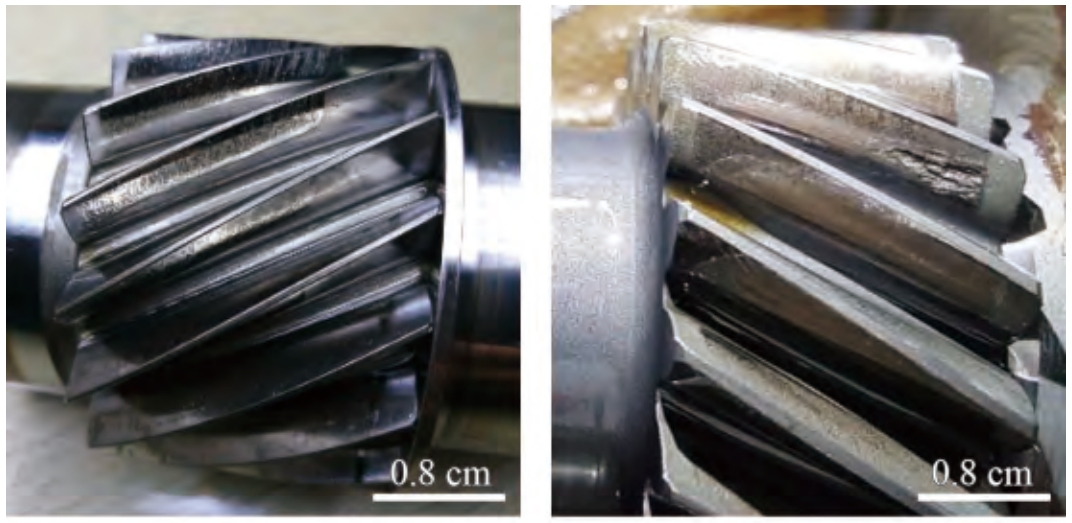