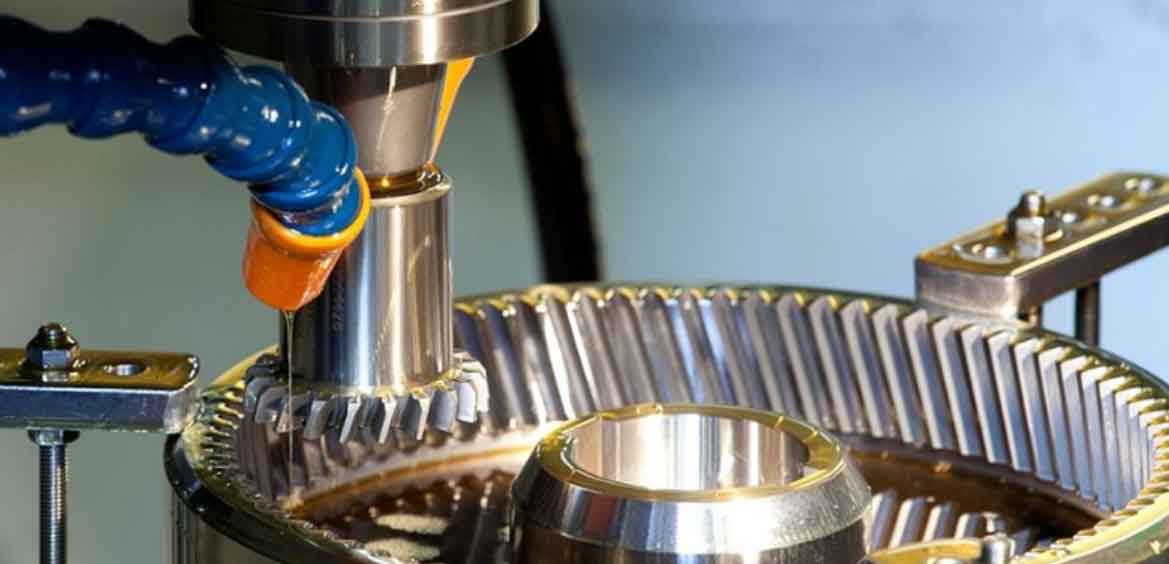
To maximize efficiency and productivity in gear production using gear shaping, several strategies can be implemented. Here are some key considerations:
- Machine Selection: Invest in modern gear shaping machines with advanced features and capabilities. Look for machines that offer high-speed cutting, rapid tool change, and reliable automation options. These features can improve productivity and reduce setup time.
- Tooling Optimization: Utilize high-quality shaper cutters that are specifically designed for the gear shaping process. Work closely with tooling manufacturers to select the most suitable cutter for the gear specifications. Consider using indexable carbide inserts for improved tool life and faster tool changes.
- Cutting Parameters Optimization: Optimize cutting parameters such as cutting speed, feed rate, and depth of cut to achieve the desired balance between productivity and gear quality. Conduct trials and experiments to determine the optimal parameters for different gear materials and tooth profiles.
- Multiple Setups and Tooling: Implement multiple setups and tooling arrangements to enable simultaneous gear shaping operations. This approach can increase productivity by shaping multiple gears in a single setup or by performing rough and finish cuts simultaneously.
- Automation and Robotics: Integrate automation and robotics into the gear shaping process to enhance efficiency and reduce manual intervention. Explore options such as robotic loading and unloading, tool change automation, and in-process inspection systems for faster and more reliable production.
- Process Monitoring and Control: Utilize advanced monitoring and control systems to track process variables, detect abnormalities, and optimize gear shaping performance. Real-time monitoring can help identify issues early, minimize downtime, and ensure consistent production quality.
- Tool Management System: Implement a tool management system that tracks tool life, monitors tool condition, and schedules timely tool maintenance or replacement. This approach ensures that tools are in optimal condition, reducing the risk of unexpected tool failures and downtime.
- Lean Manufacturing Principles: Apply lean manufacturing principles to streamline the gear shaping process. Eliminate waste, optimize workflow, and improve material flow to minimize non-value-added activities and maximize overall productivity.
- Continuous Improvement: Foster a culture of continuous improvement within the gear manufacturing process. Encourage feedback from operators and involve them in identifying opportunities for optimization. Regularly review and analyze production data to identify bottlenecks, inefficiencies, and areas for improvement.
- Training and Skill Development: Provide comprehensive training programs for gear shaping operators to enhance their skills and knowledge. Regularly update their training to keep up with advancements in gear shaping technology and techniques.
By implementing these strategies, gear manufacturers can enhance efficiency, increase productivity, and deliver high-quality gears in a cost-effective manner. Continuous monitoring, analysis, and improvement are essential to maintain and improve the efficiency of the gear shaping process over time.