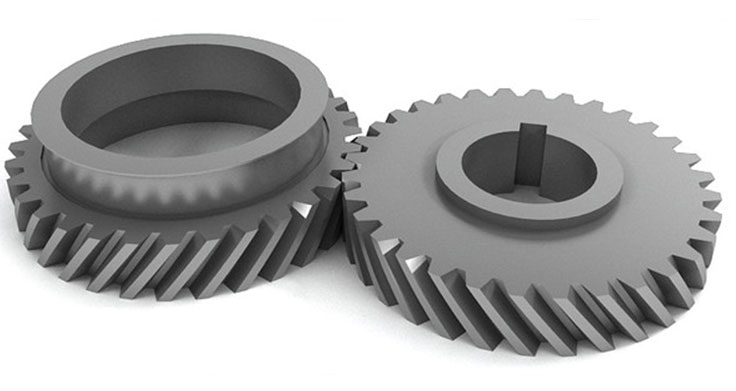
Gearbox noise reduction is a critical aspect of engineering design, as noise generated during gear meshing can be undesirable and affect the overall performance and comfort of the system. Helical gears play a significant role in improving acoustic performance in gearboxes due to their unique design characteristics. Here’s how helical gears contribute to gearbox noise reduction:
1. Smooth Tooth Engagement:
- The helical tooth profile of helical gears allows for gradual and continuous tooth engagement during meshing. This results in a smoother transfer of power and reduced impact forces compared to spur gears, which have instantaneous tooth engagement. The smoother engagement reduces gear meshing noise.
2. Reduced Gear Whine:
- Helical gears exhibit lower gear whine, a high-frequency noise caused by gear meshing. The helix angle of helical gears distributes the vibration over a larger area, reducing the amplitude of the noise and making it less noticeable.
3. Lower Vibration Levels:
- The gradual meshing action of helical gears helps reduce vibration levels in the gearbox. Lower vibration not only contributes to noise reduction but also improves overall gearbox performance and longevity by minimizing wear and fatigue.
4. Minimized Backlash:
- Helical gears generally have lower backlash compared to spur gears. Backlash refers to the clearance between gear teeth when they are not in mesh. Lower backlash leads to quieter operation and improved positional accuracy.
5. Enhanced Load Distribution:
- The helix angle of helical gears provides multiple teeth in contact at any given time, distributing the load more evenly along the gear tooth surfaces. This improved load distribution reduces localized stresses and noise generation during gear meshing.
6. Surface Contact:
- Helical gears have a larger area of contact between the mating teeth compared to spur gears, resulting in reduced contact stresses and noise.
7. Improved Lubrication:
- Helical gears benefit from better lubrication due to the helical tooth orientation, allowing for more effective lubricant distribution. Proper lubrication reduces friction, wear, and noise in the gearbox.
8. Damping Characteristics:
- The helix angle of helical gears introduces a self-locking feature, providing some inherent damping capabilities. This dampening effect helps reduce gear vibration and noise.
9. Reduction of Resonance:
- The design of helical gears can be optimized to avoid resonance frequencies that may amplify gear noise. Proper tooth profile design and tooth modification can minimize resonant conditions.
10. High-Quality Manufacturing:
- Precision manufacturing techniques, such as gear grinding and honing, ensure accurate tooth profiles and surface finishes, contributing to quieter gear operation.
By combining these design and manufacturing features, helical gears offer superior acoustic performance in gearboxes, making them a popular choice in applications where noise reduction is essential, such as automotive transmissions, industrial machinery, and robotics. The quieter operation of helical gears improves the overall user experience and extends the service life of the gearbox.