Gear shaping is indeed considered the cornerstone of industrial gear production. It is a widely used and versatile method for manufacturing high-precision gears that are crucial components in various industries. Here are some reasons why gear shaping is considered the cornerstone of industrial gear production:
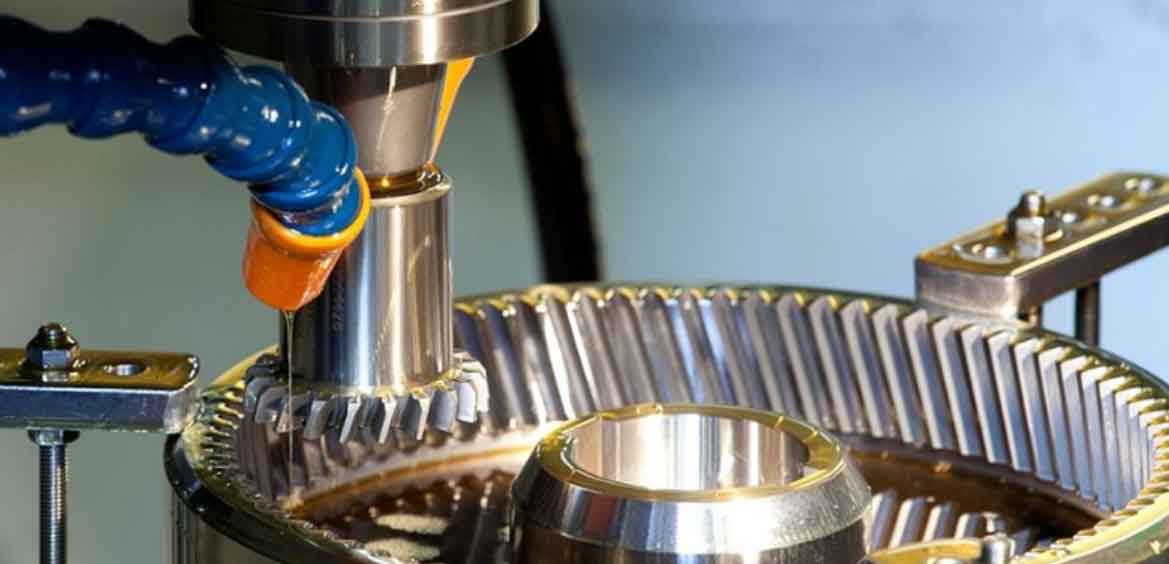
- Accuracy and Precision: Gear shaping offers exceptional accuracy and precision in producing gear teeth. The gear shaping process involves using a specially designed cutting tool (shaper cutter) and a gear shaping machine to generate the gear tooth profile. This results in highly precise gear teeth with tight dimensional tolerances and excellent tooth surface finish, ensuring smooth and efficient power transmission.
- Wide Range of Gear Types: Gear shaping is capable of producing a wide range of gear types, including spur gears, helical gears, internal gears, and more. This versatility allows manufacturers to meet the diverse gear requirements of different applications and industries. Gear shaping machines can be adapted to produce gears of various sizes, tooth profiles, and configurations, making it suitable for both small-scale and large-scale gear production.
- High Production Efficiency: Gear shaping is a highly efficient gear manufacturing process. It allows for the simultaneous cutting of multiple gear teeth, reducing cycle times and increasing production output. Gear shaping machines can be equipped with advanced features such as automatic tool changing systems, in-process monitoring, and CNC control, further enhancing production efficiency and reducing downtime.
- Suitability for Mass Production: Gear shaping is well-suited for mass production of gears. Once the gear shaping machine is set up and properly calibrated, it can continuously produce gears with consistent quality and high repeatability. The ability to produce large quantities of gears efficiently makes gear shaping a preferred method in industries that require a high volume of gears, such as automotive, heavy machinery, and power transmission.
- Capability for Complex Gear Profiles: Gear shaping can produce complex gear profiles that are essential for specific applications. This includes gears with custom tooth modifications, optimized tooth contact patterns, and specialized geometries. Gear shaping machines can be programmed to generate gear teeth with intricate shapes and profiles, ensuring that gears meet the unique requirements of the intended application.
- Strength and Durability: Gears produced through gear shaping exhibit high strength and durability. The cutting process in gear shaping ensures that the gear teeth have excellent load-bearing capabilities and can withstand the demands of heavy-duty applications. The precise tooth engagement achieved through gear shaping results in reduced wear and extended gear life, enhancing the overall durability and reliability of the gear system.
- Compatibility with Various Materials: Gear shaping can accommodate a wide range of gear materials, including alloy steels, carbon steels, stainless steels, and non-ferrous metals. This versatility allows manufacturers to select the most suitable material for specific application requirements, considering factors such as strength, wear resistance, and compatibility with operating conditions.
- Integration with Modern Manufacturing Technologies: Gear shaping can be seamlessly integrated with modern manufacturing technologies, such as computer-aided design (CAD), computer-aided manufacturing (CAM), and automation systems. This integration enables efficient design, simulation, and optimization of gear profiles, as well as automated production processes for enhanced productivity and quality control.
In summary, gear shaping is considered the cornerstone of industrial gear production due to its accuracy, versatility, efficiency, and ability to produce high-quality gears. It is a reliable method for manufacturing gears used in a wide range of applications, from automotive and aerospace to machinery and robotics. Gear shaping ensures that the gears meet stringent requirements for performance, reliability, and durability, making it a fundamental process in the industrial gear manufacturing industry.