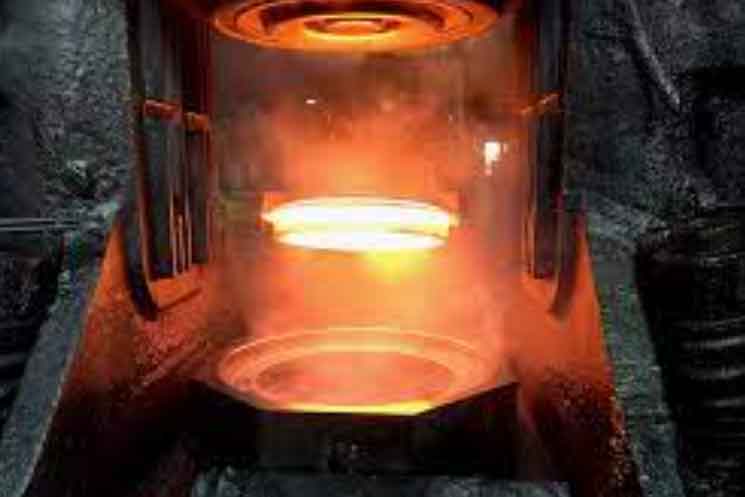
The gear forging process involves transforming raw material into finished gears through a series of steps that shape and strengthen the metal. Here’s an overview of the gear forging process:
- Raw Material Selection: The process begins with selecting the appropriate raw material, which is usually a metal alloy such as carbon steel, alloy steel, stainless steel, or non-ferrous metals like brass or aluminum. The choice of material depends on the application and desired gear properties.
- Heating the Material: The selected raw material is heated to a precise temperature in a furnace to make it more malleable for forging. The heating temperature is critical as it affects the material’s plasticity and ease of forming during the forging process.
- Die Preparation: The die, also known as the forging die or tooling, is a precision-machined mold used to shape the heated material into the desired gear form. The die is typically made from high-strength tool steel.
- Pre-Forming: In this step, the heated material is placed into the forging die, and a hydraulic or mechanical press exerts a compressive force to shape the material into a pre-form. This pre-form typically resembles the approximate shape of the final gear.
- Impression Die Forging: In the next stage, the pre-formed gear undergoes impression die forging. The pre-form is placed into the impression die, and the die is closed around it. The press applies intense pressure to shape the gear to the exact dimensions of the die cavity.
- Trimming: After impression die forging, the forged gear may have excess flash or material on its edges. Trimming removes this excess material to achieve the final gear shape.
- Heat Treatment: The forged gear is then heat-treated to improve its mechanical properties, such as hardness and toughness. The heat treatment process involves heating the gear to a specific temperature and then cooling it at a controlled rate.
- Machining (Optional): Depending on the gear’s complexity and required accuracy, additional machining processes such as drilling, milling, or grinding may be performed to achieve precise gear tooth profiles and other critical dimensions.
- Surface Finishing (Optional): Surface finishing processes, such as shot peening or polishing, may be employed to improve the gear’s surface texture and reduce the risk of fatigue failures.
- Quality Inspection: Throughout the gear forging process, the gears are subject to stringent quality control measures. Non-destructive testing (NDT) methods, dimensional inspections, and material testing ensure the gears meet the required specifications and performance standards.
- Final Assembly (Optional): In some applications, the forged gears may undergo final assembly with other components to form complete gear assemblies or gearboxes.
- Finishing and Coating (Optional): Depending on the application, the gear’s surface may be finished with specific coatings, such as plating or painting, to enhance its performance and durability.
The completed forged gears are then ready for use in various industries, where their superior strength, durability, and reliability make them essential components in critical gear-driven systems. The gear forging process is a precise and controlled method of producing high-quality gears suitable for demanding applications.
Pages: 1 2