The tooth profile and design of straight bevel gears are critical factors that directly impact the performance, efficiency, and reliability of the gear system. Here are some key considerations for gear tooth profile and design in straight bevel gears:
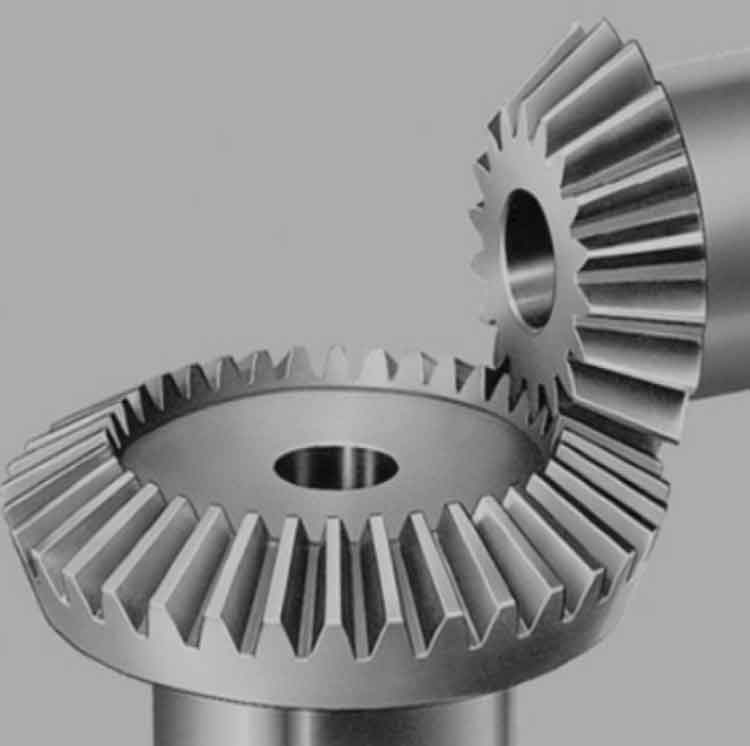
1. Tooth Profile:
- The tooth profile of straight bevel gears is typically generated as an involute curve. This involute tooth profile ensures smooth and uniform contact between mating gear teeth, reducing friction and wear.
2. Pitch Angle and Cone Angles:
- The pitch angle is the angle between the tooth face and the gear’s axis, while the cone angles are the angles between the gear axes. These angles determine the tooth shape and the overall configuration of the straight bevel gears.
3. Tooth Geometry and Size:
- The geometry and size of the gear teeth are critical for achieving the desired gear ratio and ensuring proper meshing between the driving and driven gears. The number of teeth, pitch diameter, and addendum (tooth height) are key design parameters.
4. Backlash and Clearance:
- Backlash is the clearance between the mating teeth when there is no load on the gears. Properly controlling backlash is essential to minimize noise, vibration, and errors in gear positioning.
5. Tooth Modifications:
- Tooth modifications such as crowning or tip relief can be incorporated to improve gear performance. Crowning helps distribute the load more evenly across the tooth width, reducing stress concentration and increasing load capacity. Tip relief is used to prevent interference between teeth.
6. Contact Ratio:
- The contact ratio is the number of teeth in contact at any given moment during gear rotation. A higher contact ratio ensures smoother gear meshing and reduced noise. Designing for a suitable contact ratio is essential to avoid gear failure and ensure proper load distribution.
7. Materials and Heat Treatment:
- Selecting appropriate gear materials and heat treatment processes is crucial for enhancing the gear’s strength, wear resistance, and durability. Hardened and case-hardened steels are commonly used for straight bevel gears.
8. Gear Accuracy and Tolerances:
- Precision manufacturing and tight tolerances are vital for achieving smooth and efficient gear meshing. Proper gear finishing processes, such as grinding or honing, help improve tooth surface finish and accuracy.
9. Lubrication:
- Adequate gear lubrication is essential for reducing friction, wear, and heat generation. Properly selected lubricants and lubrication systems ensure smooth gear operation and extend gear life.
10. Application Considerations:
- Design considerations should also take into account the specific application requirements, including load conditions, speed, torque, operating environment, and expected service life.
Overall, the tooth profile and design of straight bevel gears should be carefully engineered to meet the specific needs of the gear system, ensuring efficient power transmission, minimal noise, and maximum reliability in various industrial applications. It is crucial to work with experienced gear designers and manufacturers to optimize the tooth profile and design for the intended use of the straight bevel gears.