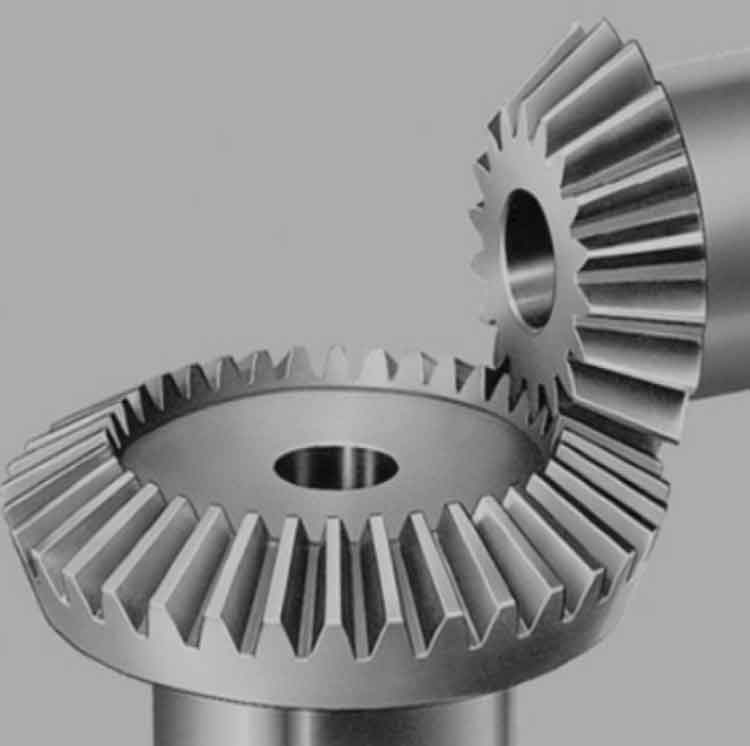
Straight bevel gears play a crucial role in enhancing gearbox efficiency in various mechanical systems. Gearboxes with well-designed straight bevel gears can achieve higher power transmission efficiency, smoother operation, and increased overall performance. Here’s a guide to understanding how straight bevel gears contribute to gearbox efficiency:
1. Gear Tooth Profile:
- Straight bevel gears have straight and parallel teeth that allow for uniform contact and efficient power transmission.
- The tooth profile design is critical to achieving minimal friction losses during meshing.
2. Gear Arrangement:
- Straight bevel gears are commonly used in right-angle gear arrangements, where the input and output shafts intersect at a 90-degree angle.
- This configuration allows for compact and efficient power transfer in various mechanical systems.
3. Load Distribution:
- Proper load distribution across the gear teeth is essential for efficient and uniform power transmission.
- Well-designed straight bevel gears ensure even distribution of the transmitted loads, minimizing stress concentrations and wear.
4. Gear Ratio Optimization:
- Gear ratio optimization is a key factor in improving gearbox efficiency.
- By selecting the appropriate gear ratios, the gearbox can be tailored to match the specific speed and torque requirements of the application.
5. Material Selection and Gear Quality:
- High-quality materials and precision manufacturing techniques contribute to lower friction losses and higher gear efficiency.
- Quality materials with suitable hardness and wear resistance help reduce losses due to gear wear and surface fatigue.
6. Lubrication and Surface Finish:
- Proper gear lubrication is essential for reducing friction and heat generation during gear operation.
- Smooth gear surfaces achieved through precise manufacturing and surface finishing reduce frictional losses.
7. Alignment and Gear Meshing:
- Accurate gear alignment ensures proper meshing and reduces misalignment losses.
- Well-aligned gears have improved contact patterns, leading to more efficient power transmission.
8. Noise Reduction:
- Reducing gear noise is an indirect but essential aspect of improving gearbox efficiency.
- Quieter gears often indicate smoother meshing and lower friction, leading to better overall performance.
9. Application-Specific Design:
- Customizing the gearbox design based on the specific application requirements enhances overall efficiency.
- Engineers can optimize gear dimensions, materials, and other factors to achieve the desired performance.
10. Regular Maintenance and Inspection:
- Regular maintenance and inspection of the gearbox are crucial to ensure optimal performance and longevity.
- Timely detection and correction of any issues prevent efficiency losses and potential failures.
By considering these factors and optimizing the design, lubrication, and manufacturing of straight bevel gears and gearboxes, engineers can achieve higher efficiency, reduced energy losses, and improved reliability in various industrial applications. As a result, gearboxes with straight bevel gears contribute significantly to more sustainable and efficient mechanical systems.