Gearbox optimization with spiral bevel gears is an important aspect of improving the performance, efficiency, and reliability of various mechanical systems. Here are some case studies and applications showcasing how spiral bevel gears are used in gearbox optimization:
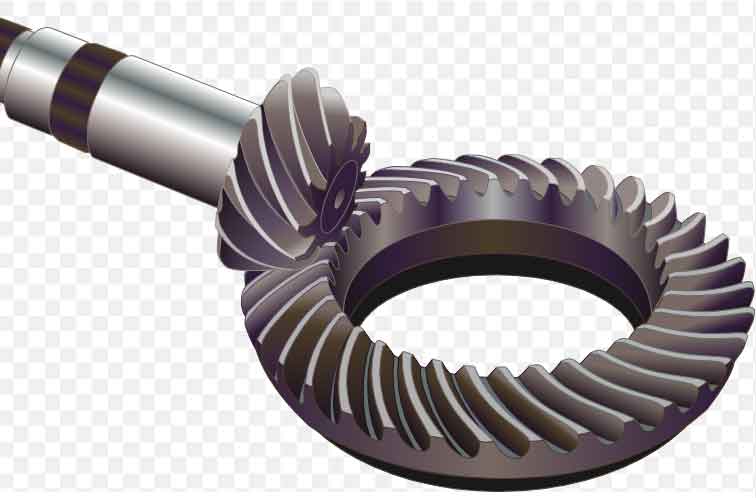
1. Automotive Transmissions:
Automotive manufacturers utilize spiral bevel gears in transmission gearboxes to transfer power from the engine to the wheels. In some high-performance vehicles, limited-slip differentials with optimized spiral bevel gears are employed to enhance traction, handling, and overall driving experience.
2. Aerospace Gearboxes:
In aerospace applications, gearbox optimization with spiral bevel gears is crucial to ensure smooth power transmission and reduce weight while maintaining high torque capacity. Helicopter main rotor gearboxes, for example, use spiral bevel gears to convert power from the engine to the rotor system efficiently.
3. Robotics and Automation:
Robots and automated machinery often require compact and high-performance gearboxes to achieve precise motion control. Spiral bevel gears are employed in robotic gearboxes to provide smooth and accurate motion, making them ideal for applications like industrial arms, articulated robots, and collaborative robots.
4. Marine Propulsion:
In marine propulsion systems, spiral bevel gears play a critical role in optimizing the performance of marine gearboxes. They enable efficient power transmission from the engine to the propeller, allowing ships to achieve optimal speed and maneuverability.
5. Heavy Machinery:
Heavy machinery, such as construction equipment and mining machinery, relies on robust and reliable gearboxes to handle heavy loads and challenging working conditions. Spiral bevel gears are often used in gearboxes for excavators, loaders, and cranes to optimize torque transmission and ensure durability.
6. Wind Turbine Drives:
Wind turbines require gearboxes that can handle varying wind speeds and efficiently convert rotational motion to electrical power. Gearbox optimization with spiral bevel gears enables smooth power transmission and helps enhance the overall energy conversion efficiency of wind turbines.
7. Machine Tools:
Machine tools, such as lathes and milling machines, rely on precise and reliable gearboxes to achieve accurate machining operations. Spiral bevel gears are used in these gearboxes to ensure smooth motion and improve the accuracy of cutting or shaping processes.
8. Printing Presses:
High-speed printing presses require optimized gearboxes to handle rapid movements and deliver precise paper feeding. Spiral bevel gears are utilized in the gearboxes of printing presses to enable efficient power transmission and precise control of paper movement.
In each of these applications, gearbox optimization with spiral bevel gears leads to improved performance, reduced noise and vibration, increased efficiency, and enhanced reliability. Engineers and designers carefully consider factors like gear tooth geometry, material selection, and heat treatment to achieve the desired performance characteristics in these gearboxes. As technology continues to advance, further innovations in spiral bevel gear design and manufacturing techniques will likely lead to even more efficient and high-performing gearboxes across various industries.