Heat treatment is a critical process in the manufacturing of gears for aerospace and defense applications. It involves the controlled heating and cooling of the gear material to alter its mechanical properties, such as hardness, strength, and toughness. The specific heat treatment processes used for gears in aerospace and defense applications may vary depending on the material, design requirements, and performance specifications. However, I can provide you with a general overview of the typical heat treatment methods used for gears in these industries.
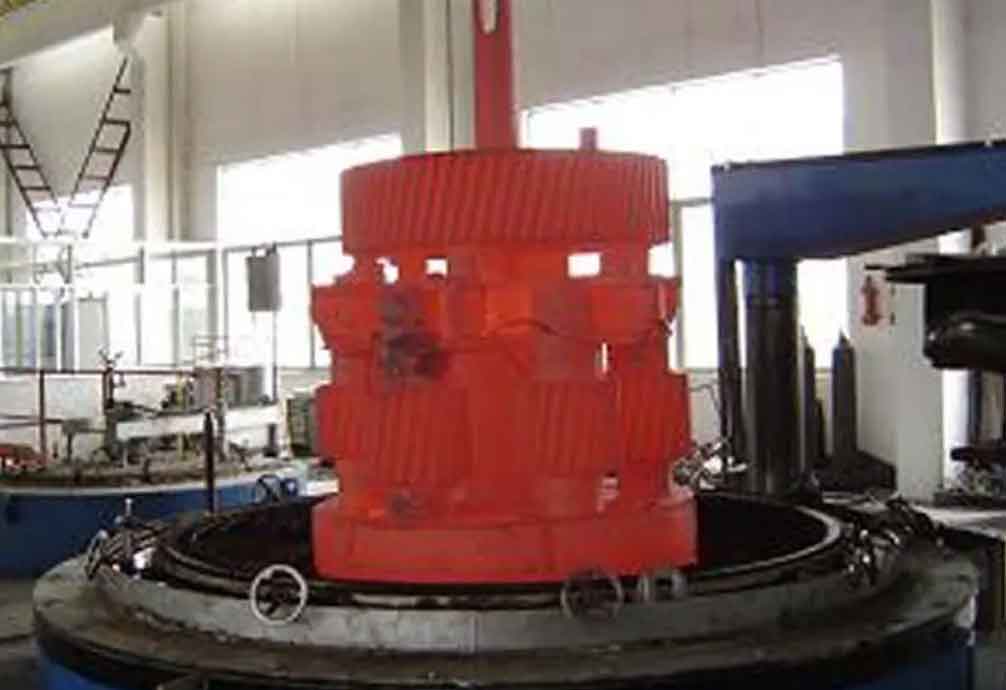
- Carburizing: Carburizing is a widely used heat treatment process for gears. It involves introducing carbon into the surface layer of the gear material to increase its hardness and wear resistance. The gears are heated in a carbon-rich environment, typically with the use of a gas or liquid carburizing medium. The carbon diffuses into the surface of the gear, forming a hardened case. After carburizing, the gears are usually quenched to achieve the desired hardness and then tempered to enhance toughness.
- Nitriding: Nitriding is another common heat treatment method for gears in aerospace and defense applications. It is a surface hardening process that involves introducing nitrogen into the gear material. The gears are heated in a nitrogen-rich atmosphere, typically at temperatures below the transformation range of the base material. The nitrogen diffuses into the surface, forming a hard layer of nitrides, which significantly improves wear resistance and fatigue strength. Nitrided gears often exhibit excellent dimensional stability and resistance to adhesion and scoring.
- Induction Hardening: Induction hardening is a localized heat treatment process used to selectively harden specific areas of the gear, such as the teeth and critical contact surfaces. It involves the use of high-frequency induction heating to rapidly heat the desired regions, followed by quenching to achieve the desired hardness. Induction hardening provides precise control over the hardened depth and minimizes distortion, making it suitable for complex gear geometries.
- Austempering: Austempering is a heat treatment technique that provides a combination of high strength and ductility. It involves quenching the gears from a high temperature into a bath or fluid maintained at a specific temperature range. The gears are held at this temperature for a sufficient time to transform the microstructure into a bainitic structure, which offers excellent toughness and fatigue resistance.
- Shot Peening: Shot peening is a surface treatment process that involves bombarding the gear’s surface with small spherical media, known as shot. The impacts from the shot create compressive stresses on the surface, which improves the gear’s fatigue life and resistance to stress corrosion cracking. Shot peening is often used in conjunction with other heat treatment methods to further enhance the performance and durability of gears.
It’s important to note that the selection of a specific heat treatment process depends on several factors, including the gear material, application requirements, and industry standards. The aerospace and defense industries have stringent quality and performance standards, and the heat treatment processes are carefully chosen to meet these requirements while ensuring the reliability and durability of the gears in demanding operating conditions.