Heat treatment in gear manufacturing can present various challenges that need to be addressed to ensure the desired properties and performance of the gears. Here are some common challenges encountered during heat treatment and their corresponding solutions:
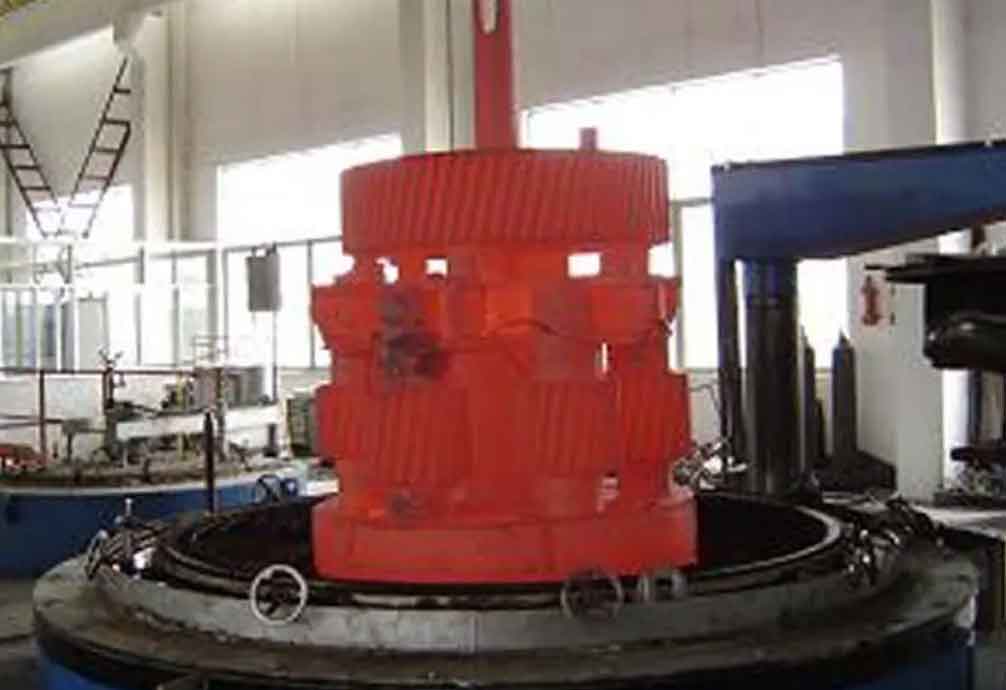
- Distortion: Heat treatment processes can cause distortion in gears due to non-uniform heating and cooling rates, phase transformations, and internal stresses. Distortion can affect the dimensional accuracy and functional performance of the gears.
- Solution: Several techniques can be employed to minimize distortion, such as using controlled heating and cooling methods, utilizing fixtures and jigs to hold the gears in a stable position during heat treatment, and employing specialized quenching techniques like interrupted quenching or using quenching media with controlled cooling rates.
- Surface Decarburization: During heat treatment, the surface of the gear may undergo decarburization, where carbon is lost from the surface layer. This can lead to a reduction in surface hardness and wear resistance.
- Solution: To minimize surface decarburization, protective atmospheres or gas mixtures can be used during heating. These atmospheres prevent oxygen from reacting with the gear surface and minimize carbon loss. Alternatively, surface coatings or protective layers can be applied to the gear prior to heat treatment to prevent decarburization.
- Non-uniform Hardness: Achieving uniform hardness throughout the gear is crucial for consistent performance and load distribution. Non-uniform hardness can occur due to improper heating or quenching techniques.
- Solution: Proper process control and optimization of heating and quenching parameters are essential to ensure uniform hardness. This may involve adjusting heating and holding times, quenching media selection, and controlling quenching rates. Computer simulations and modeling can also aid in optimizing heat treatment parameters to achieve uniform hardness.
- Surface Roughness and Residual Stresses: Heat treatment processes can result in the generation of surface roughness and residual stresses, which can affect the gear’s performance and fatigue life.
- Solution: Post-heat treatment processes such as grinding, polishing, or shot peening can be employed to remove surface roughness and induce compressive residual stresses, improving the fatigue strength of the gears. Controlled cooling rates during quenching can also help in reducing residual stresses.
- Process Control and Quality Assurance: Maintaining consistent process control and ensuring quality assurance throughout the heat treatment process is crucial to meet the required specifications and standards.
- Solution: Employing robust process monitoring and control techniques, such as temperature monitoring, quenching media analysis, and real-time process feedback, can help maintain process parameters within the desired range. Regular inspection, testing, and quality control measures, such as hardness testing, metallurgical analysis, and non-destructive testing, should be implemented to verify the quality and performance of the heat-treated gears.
Addressing these challenges through optimized process parameters, advanced equipment, and stringent quality control measures is essential to produce high-quality gears with the desired properties for aerospace and defense applications.