Normalizing treatment
Normalizing is a heat treatment process in which the steel is heated to 30 ~ 50 ℃ or higher above the upper critical point AC3 or ACCM and cooled in still air after austenitizing. After normalizing, the gear can eliminate the internal stress, improve the toughness, and improve the machinability. Gears made of high quality carbon steel or alloy steel with carbon content of 0.25% ~ 0.50% are usually normalized. After normalizing, the hardness of the gear is moderate (generally hb163-217), which can also meet the requirements of machining. For gears made of this kind of steel, if the force is not large and the performance requirements are not high, normalizing can be used as the final heat treatment to reduce the working procedure, save resources and improve the working efficiency.
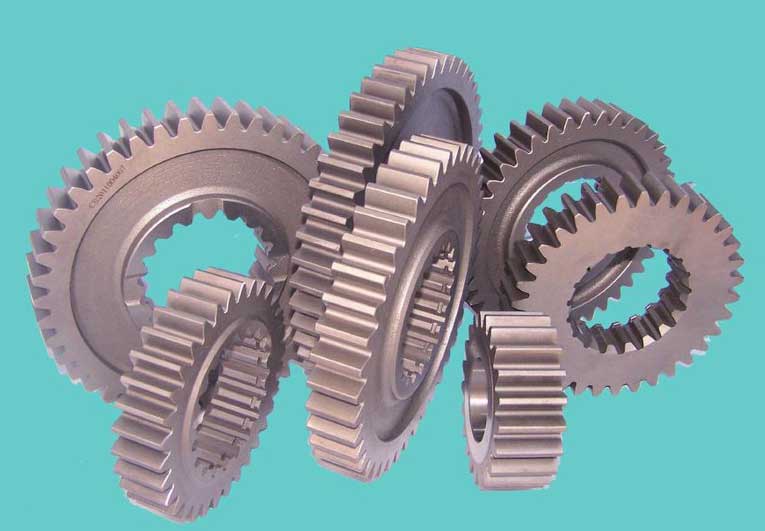
Quenching and tempering
The heat treatment process to obtain tempered sorbite after quenching is called tempering. After quenching and tempering, the material of gear is optimized to a great extent, which has not only high strength and yield limit, but also enough plasticity and toughness, so it has good comprehensive mechanical properties. Quenching and tempering treatment shall be applied to gears made of high-quality carbon steel or alloy steel with carbon content of 0.25% ~ 0.50%. Generally, the Brinell hardness (HB) of tooth surface can reach 220-280 after quenching and tempering. Because gears need to be further processed after tempering, such as milling, inserting, shaving, etc., the hardness requirements can be lower; but for smaller gears, the hardness requirements can be higher. In the process of gear working, in order to reduce the possibility of gear scuffing and make the life of the matched gear equal, the hardened and tempered pinion is usually used to pair with the normalized big gear to maintain a certain hardness difference. In general, the Brinell hardness (HB) of pinion tooth surface is 20-40 higher than that of big gear.
Surface quenching
Surface hardening is a heat treatment method used to strengthen the surface layer of workpiece. It only heats the surface of workpiece to make it hardened and strengthened, while the core still maintains the original structure, so that the workpiece has the characteristics of good wear resistance, high impact toughness and high fatigue strength. Surface hardening is mainly used for gears made of medium carbon steel or medium carbon alloy steel, such as 40, 45, 40Cr, 35Cr Mo steel.
There are many methods of surface quenching, but induction heating is widely used in the current heat treatment production. After induction heating, the gear’s Rockwell hardness (HRC) is 2 ~ 3 higher than that of general quenching; there is a large residual stress in the hardened surface layer, which can increase the fatigue strength of small and medium modulus gear by 2 ~ 3 times. The penetration depth of induction heating into the gear surface layer mainly depends on the current frequency. For example, Jinan Qingqi qm125 series and qm200gy series motorcycles have large sprockets. The drawings require high-frequency quenching treatment of teeth and Rockwell hardness (HRC) of 40-45. The so-called high frequency quenching is the high frequency induction heating surface quenching. The commonly used working frequency of high frequency induction hardening is 200-250 kHz, and the hardened layer of 1-2 mm can be obtained. The Rockwell hardness (HRC) of tooth surface is generally 40-55.
In order to ensure the surface hardness, core strength and toughness of gear after surface quenching, the rough of gear should be normalized or tempered in advance, and then the induction heating surface quenching. After induction heating and quenching, low temperature tempering is generally required to reduce internal stress and brittleness.
Carburizing treatment
Put the gear into the carburized active medium, heat it at 900 ~ 950 ℃ for heat preservation, make the active carbon atoms penetrate into the gear surface to obtain the high carbon surface layer, and then carry out the process of quenching and low temperature tempering, which is called carburizing heat treatment. The purpose of gear carburizing is to make the surface of gear have high hardness and wear resistance, while the center has certain strength and high toughness. The carburized gear steel for motorcycle is low carbon steel and low carbon alloy steel with carbon content of 0.15% ~ 0.25%, such as 20, 20CrMnTi steel.
The surface structure of gear after carburizing is high carbon tempered martensite and fine-grained cementite, and its wear resistance is higher than that of medium carbon tempered martensite. After carburizing, the hardened layer is evenly distributed along the tooth profile, so the impact resistance is better than that of the surface hardened gear. After quenching and low temperature tempering, the surface structure of carburized gear is composed of fine acicular tempered martensite and fine cementite, and the Rockwell hardness (HRC) is 58-62.
Nitriding treatment
Nitriding is a chemical heat treatment process in which the active nitrogen atoms penetrate into the gear surface to form a nitrogen rich hardening layer at a certain temperature. After nitriding, a nitriding layer is formed on the surface of the gear, and the surface Vickers hardness (HV) can reach 950-1200, which is equivalent to the Rockwell hardness (HRC) 65-72, with higher wear resistance. A larger residual compressive stress is formed in the nitriding layer, which makes the gear after nitriding have higher fatigue resistance. The continuous thin film composed of dense nitride is formed on the nitriding surface, which makes the gear have high corrosion resistance. The temperature of nitriding treatment is low, and the nitriding for the purpose of improving wear resistance and fatigue resistance is usually carried out at 500 ~ 570 ℃; the nitriding temperature for the purpose of improving corrosion resistance is not higher than 650 ℃, so the deformation of gears before and after treatment is very small, and the size accuracy can be maintained.
The main materials used for nitriding gears of motorcycles are 20CrMnTi and 45 steel. Gear must be tempered before nitriding and no heat treatment after nitriding. Because the nitrided layer of gear is thin and its bearing capacity is not as high as that of carburized gear, the hardened layer is in danger of peeling off under impact load, so the nitrided gear is suitable for the occasions with stable load and good lubrication.
The selection of motorcycle gear materials and heat treatment process are analyzed above. However, with the development of motorcycle industry, the progress of process technology, and the gradual improvement of customer demand, various gears will appear in the future production, even some gears with special requirements for service performance, This requires designers of enterprises to adhere to the selection principle of motorcycle gear materials, conduct comprehensive analysis and comprehensive consideration, and reasonably select materials and heat treatment process.