Heat treatment optimization in gear production involves finding the right balance between performance and cost. Heat treatment is a critical process that improves the mechanical properties of gears, such as hardness, strength, and durability. However, it can also be expensive and time-consuming. Here are some considerations to achieve an optimal balance:
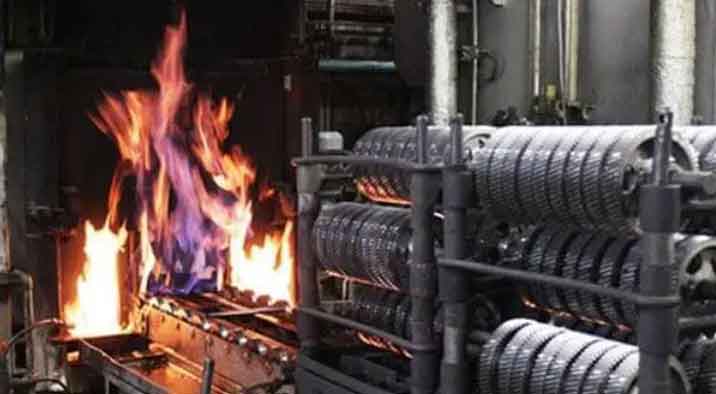
- Material selection: Choosing the right material for gear production is crucial. Some materials naturally possess desirable properties, reducing the need for extensive heat treatment. For example, alloy steels like 4140 or 4340 have good hardenability, which can minimize the required heat treatment steps.
- Process optimization: Work closely with heat treatment experts to optimize the process parameters. Factors such as temperature, holding time, quenching medium, and cooling rate can significantly impact the resulting properties. By fine-tuning these parameters, you can achieve the desired performance while minimizing costs.
- Pre-treatment processes: Prior to heat treatment, consider implementing pre-treatment processes like shot blasting or grinding. These can remove surface defects and improve the material’s response to heat treatment, potentially reducing the need for more expensive treatments.
- Selective heat treatment: Instead of subjecting the entire gear to heat treatment, consider employing selective heat treatment. This involves treating only specific areas that require enhanced performance, such as tooth profiles or high-stress regions. By targeting treatment to critical areas, you can reduce costs associated with treating the entire gear.
- Quenching techniques: Explore alternative quenching methods, such as using different quenching media or employing specialized techniques like martempering or austempering. These techniques can offer advantages in terms of cost and performance compared to traditional oil or water quenching.
- Process automation: Implementing automation and advanced monitoring systems can optimize the heat treatment process, improving consistency and reducing costs associated with manual labor and rework. Real-time monitoring can also help identify and rectify any issues promptly, saving time and resources.
- Cost analysis: Perform a comprehensive cost analysis to evaluate the impact of different heat treatment options. Consider not only the direct costs of heat treatment but also the potential downstream benefits, such as improved product quality, longer service life, and reduced warranty claims. Balancing initial costs with long-term performance benefits is crucial for achieving cost optimization.
Remember, striking the right balance between performance and cost in gear production requires a thorough understanding of the specific application, material properties, and customer requirements. Collaborating with heat treatment experts and leveraging their expertise can greatly assist in achieving the desired outcome.