Bevel gears and internal gears are two common types of gears used in various mechanical systems. While both serve the purpose of transmitting rotational motion and power between shafts, they have distinct design characteristics and applications. Let’s compare and analyze these gear types:
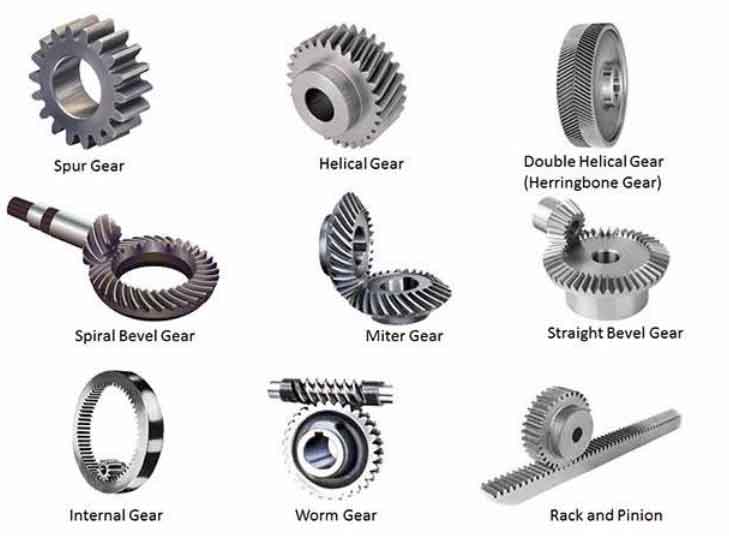
- Design and Meshing:
- Bevel Gears: Bevel gears have conical-shaped teeth and are used to transmit motion between intersecting shafts. They are available in straight and spiral tooth forms. Straight bevel gears have straight teeth, while spiral bevel gears have curved teeth for smoother engagement and reduced noise. Bevel gears can have different cone angles depending on the application.
- Internal Gears: Internal gears have teeth cut on the inner surface of the gear, with the teeth facing inward. They are often used in applications where space constraints are present, such as planetary gear systems or gearboxes. The external gear meshes with the internal gear, transmitting rotational motion.
- Direction of Shaft Rotation:
- Bevel Gears: Bevel gears are typically used to change the direction of shaft rotation. They can transmit motion between perpendicular shafts at various angles, such as 90 degrees.
- Internal Gears: Internal gears are primarily used in applications where the direction of shaft rotation needs to be maintained. They enable the power transmission without changing the direction of rotation.
- Load Distribution and Torque Transmission:
- Bevel Gears: Bevel gears are excellent for transmitting high torque loads and distributing the load evenly across the gear teeth. They can handle both radial and axial loads effectively.
- Internal Gears: Internal gears are also capable of transmitting high torque loads, but they have the advantage of better load distribution compared to external gears. The load is distributed over a greater number of teeth, resulting in reduced stress on individual teeth.
- Efficiency and Speed:
- Bevel Gears: Bevel gears can achieve high efficiency due to their precise tooth engagement. However, in some cases, there may be a slight decrease in efficiency due to the sliding motion of the teeth along the gear face. They can operate at high speeds, but the efficiency may decrease as the speed increases.
- Internal Gears: Internal gears can have high efficiency, especially in planetary gear systems, where the load is shared among multiple gear sets. They can handle high speeds and transmit power smoothly.
- Lubrication and Maintenance:
- Bevel Gears: Bevel gears generally require proper lubrication to minimize friction and wear between the mating teeth. Lubrication maintenance is crucial for their optimal performance and longevity.
- Internal Gears: Internal gears benefit from the oil splash lubrication within the gear housing or gearbox, which helps in reducing friction and wear. This internal lubrication mechanism simplifies maintenance requirements.
Bevel gears are commonly used to change the direction of rotation between intersecting shafts, while internal gears maintain the direction of rotation and are often employed in space-constrained applications. Bevel gears excel in load distribution, while internal gears provide better load distribution and are useful in high-speed applications. The choice between these gear types depends on specific design requirements and operational considerations.