Introduction
Gear Shaft components are critical in mechanical systems, transferring torque and rotation between different parts. Their durability directly impacts the performance, efficiency, and longevity of machinery. Heat treatment is a vital process in enhancing the durability of Gear Shaft components. This article explores various heat treatment techniques used to improve the durability of Gear Shaft components, detailing their benefits, processes, and applications.
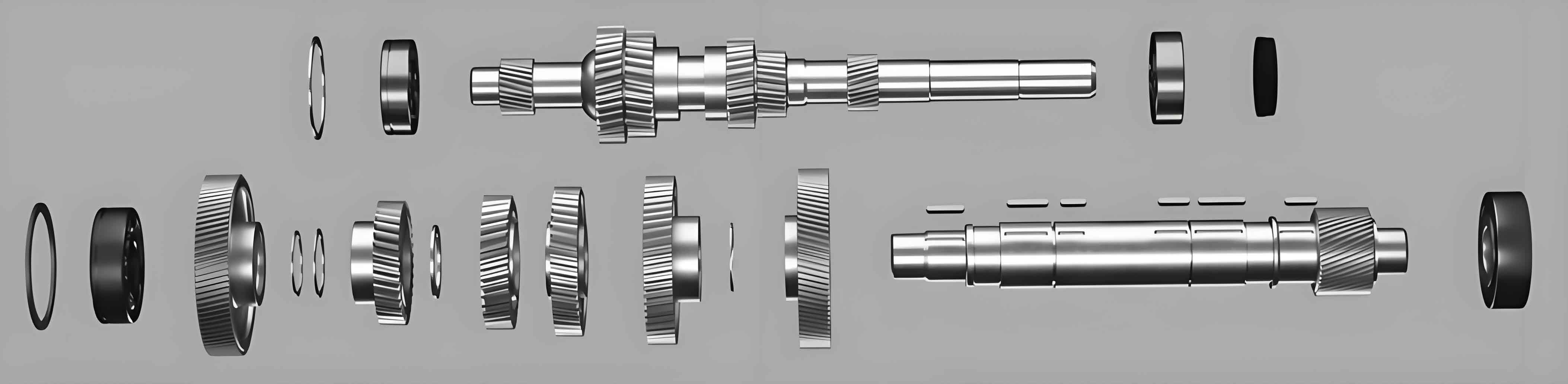
Importance of Heat Treatment for Gear Shaft
Heat treatment alters the physical and mechanical properties of Gear Shaft components to enhance their hardness, strength, and wear resistance. This process is crucial for ensuring the Gear Shaft can withstand high loads, resist wear and fatigue, and maintain optimal performance over time.
Key Benefits of Heat Treatment for Gear Shaft:
- Increased Hardness:
- Enhances resistance to surface wear and deformation.
- Improved Strength:
- Increases the ability to handle high torque and stress.
- Enhanced Toughness:
- Improves resistance to impact and shock loading.
- Extended Lifespan:
- Reduces the frequency of maintenance and replacement.
Heat Treatment Techniques for Gear Shaft
Several heat treatment techniques can be applied to Gear Shaft components to enhance their durability. Each technique offers specific benefits and is suitable for different types of Gear Shaft applications.
1. Carburizing
Carburizing is a heat treatment process that introduces carbon into the surface layer of the Gear Shaft, increasing surface hardness while maintaining a tough core.
Process:
- Preparation:
- The Gear Shaft is cleaned and placed in a carbon-rich environment.
- Heating:
- The Gear Shaft is heated to a temperature where carbon can diffuse into the surface.
- Quenching:
- The Gear Shaft is rapidly cooled to lock the carbon in place, forming a hard surface layer.
Benefits:
- Enhanced surface hardness and wear resistance.
- Maintains a tough core for improved impact resistance.
2. Nitriding
Nitriding is a heat treatment process that introduces nitrogen into the surface of the Gear Shaft, forming a hard, wear-resistant layer without the need for quenching.
Process:
- Preparation:
- The Gear Shaft is cleaned and placed in a nitrogen-rich environment.
- Heating:
- The Gear Shaft is heated to a temperature where nitrogen can diffuse into the surface.
- Cooling:
- The Gear Shaft is allowed to cool slowly, maintaining the hard surface layer.
Benefits:
- High surface hardness and wear resistance.
- Minimal distortion and stress in the Gear Shaft.
3. Induction Hardening
Induction hardening is a heat treatment process that uses electromagnetic induction to heat the surface of the Gear Shaft rapidly, followed by immediate quenching.
Process:
- Heating:
- An induction coil is used to rapidly heat the surface of the Gear Shaft.
- Quenching:
- The heated surface is quickly cooled to form a hard, wear-resistant layer.
Benefits:
- Localized hardening with minimal impact on the core properties.
- Suitable for complex shapes and localized areas.
4. Case Hardening
Case hardening involves heating the Gear Shaft in the presence of a carburizing or nitriding agent to create a hard outer layer while maintaining a tough interior.
Process:
- Preparation:
- The Gear Shaft is cleaned and placed in a carburizing or nitriding environment.
- Heating:
- The Gear Shaft is heated to the required temperature.
- Quenching:
- The Gear Shaft is quenched to form the hard outer layer.
Benefits:
- Increased surface hardness and wear resistance.
- Maintains a tough and ductile core.
Comparison of Heat Treatment Techniques for Gear Shaft
Technique | Process | Benefits | Applications |
---|---|---|---|
Carburizing | Heating in a carbon-rich environment, followed by quenching | Enhanced surface hardness, tough core | Automotive, industrial machinery |
Nitriding | Heating in a nitrogen-rich environment, slow cooling | High surface hardness, minimal distortion | Aerospace, precision engineering |
Induction Hardening | Rapid heating with induction coil, followed by quenching | Localized hardening, minimal impact on core properties | Automotive, heavy machinery |
Case Hardening | Heating in carburizing/nitriding environment, followed by quenching | Increased surface hardness, tough interior | General industrial applications |
Applications of Heat-Treated Gear Shaft
Heat-treated Gear Shaft components are used in various industries where durability and performance are critical. The choice of heat treatment technique depends on the specific application requirements.
1. Automotive Industry
Heat-treated Gear Shaft components in the automotive industry ensure reliable transmission of power in engines, gearboxes, and drivetrains.
Benefits:
- Enhanced wear resistance for longer service life.
- Improved performance under high torque and stress.
2. Aerospace Industry
In the aerospace industry, Gear Shaft components must withstand extreme conditions and high loads. Heat treatment techniques like nitriding are commonly used.
Benefits:
- High surface hardness with minimal distortion.
- Reliable performance in demanding environments.
3. Industrial Machinery
Industrial machinery requires Gear Shaft components that can handle heavy loads and continuous operation. Induction hardening and carburizing are popular choices.
Benefits:
- Increased durability and wear resistance.
- Reduced maintenance and downtime.
4. Precision Engineering
In precision engineering, Gear Shaft components require high accuracy and minimal distortion. Nitriding provides the necessary surface hardness without affecting the core properties.
Benefits:
- Precision and reliability in high-performance applications.
- Enhanced surface properties without compromising core toughness.
Best Practices for Heat Treating Gear Shaft
To achieve optimal results, certain best practices should be followed during the heat treatment of Gear Shaft components.
1. Material Selection
Choose materials that respond well to heat treatment processes, such as alloy steels, stainless steels, and tool steels.
2. Process Control
Maintain precise control over temperature, time, and atmosphere conditions during heat treatment to ensure consistent results.
3. Quality Inspection
Conduct thorough inspections before and after heat treatment to ensure the Gear Shaft meets the required specifications and standards.
4. Post-Treatment Processes
Implement post-treatment processes like tempering, stress relieving, and surface finishing to enhance the properties of the heat-treated Gear Shaft.
Common Heat Treatment Defects and Solutions
Defect | Cause | Solution |
---|---|---|
Cracking | Rapid cooling, improper quenching | Optimize quenching process, gradual cooling |
Distortion | Uneven heating, rapid temperature changes | Use controlled heating and cooling rates |
Surface Decarburization | Prolonged exposure to high temperatures | Protect surface with suitable atmosphere |
Overheating | Excessive heat during treatment | Monitor and control heating temperatures |
Conclusion
Heat treatment is a crucial process in enhancing the durability of Gear Shaft components, ensuring they can withstand the demands of various industrial applications. By understanding and applying the appropriate heat treatment techniques, manufacturers can significantly improve the hardness, strength, and wear resistance of Gear Shaft components. This results in increased operational efficiency, reduced maintenance costs, and extended service life. Ongoing advancements in heat treatment technologies and practices continue to push the boundaries of Gear Shaft performance, contributing to the overall reliability and success of mechanical systems across industries.