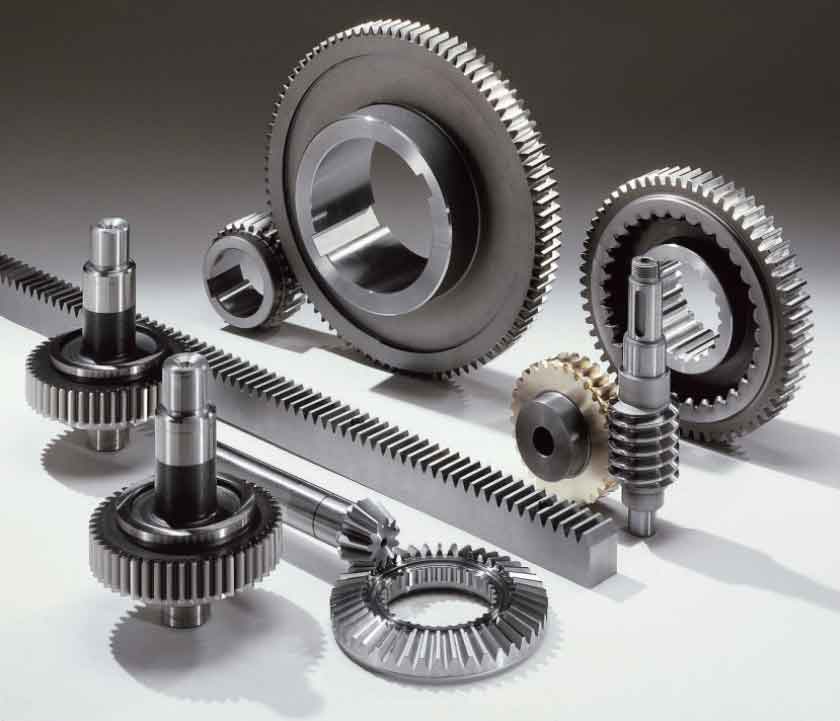
Proper maintenance is crucial for ensuring the longevity and performance of spur gear in various applications. Here’s a detailed guide on effective maintenance strategies to prolong the life of spur gears:
1. Regular Inspection and Monitoring
- Visual Inspections: Conduct regular visual inspections to check for signs of wear, such as pitting, scuffing, or tooth deformation. This can help in early detection of potential issues.
- Vibration Analysis: Use vibration analysis tools to detect abnormal vibrations that might indicate misalignment, imbalance, or wear in spur gear.
- Thermal Imaging: Employ thermal cameras to monitor the temperature distribution of spur gear systems during operation. Overheating can be a sign of excessive friction or misalignment.
2. Lubrication Management
- Appropriate Lubrication: Choose the right type and viscosity of lubricant based on spur gear material, load, speed, and environmental conditions. High-quality lubricants can significantly reduce wear and tear.
- Regular Lubrication: Establish a schedule for regular lubrication to ensure that spur gear is consistently lubricated, reducing friction and wear. Automated lubrication systems can be installed for continuous and consistent lubrication.
- Lubricant Analysis: Periodically analyze the lubricant for signs of contamination and degradation. This helps in assessing the condition of both the lubricant and spur gear system.
3. Load Management
- Operational Parameters: Monitor and control the operational parameters such as load, speed, and torque to ensure they do not exceed the design specifications of the gear system. Overloading gears can lead to premature wear and failure.
- Dynamic Balancing: Ensure that the gears and associated components are properly balanced. Imbalance can increase mechanical stress and lead to premature failure.
4. Environmental Control
- Dust and Debris Control: Keep spur gear environment clean to prevent dust, debris, and other contaminants from entering spur gear system. Use seals and housings where necessary.
- Corrosion Prevention: In corrosive environments, use corrosion-resistant materials for spur gears or apply protective coatings. Also, control humidity and exposure to corrosive chemicals to prevent spur gear deterioration.
5. Alignment and Installation
- Proper Installation: Ensure that spur gear is correctly installed with accurate alignment. Misalignment can cause uneven load distribution and increased wear.
- Re-Alignment: Periodically check and adjust the alignment of spur gear, especially after maintenance activities or operational impacts that could shift the positioning.
6. Wear and Damage Repair
- Surface Reconditioning: Techniques such as grinding or polishing can be used to restore the surface quality of worn gear, extending their service life.
- Tooth Repair: Small chips or damage to spur gear teeth can sometimes be repaired without needing to replace the entire gear. Techniques include welding, followed by machining to restore the tooth profile.
7. Replacement Strategy
- Scheduled Replacement: Based on historical data and manufacturer recommendations, schedule replacement of spur gear at the end of their service life before catastrophic failure occurs.
- Spare Parts Management: Maintain an inventory of critical spare parts, such as spur gear and bearings, to minimize downtime during maintenance or unexpected failures.
8. Training and Documentation
- Maintenance Training: Train maintenance personnel on proper gear maintenance procedures, including inspection, lubrication, and troubleshooting.
- Documentation: Keep detailed records of maintenance activities, inspections, and replacements. This documentation can help in tracking wear trends and predicting future maintenance needs.
By implementing these maintenance strategies, the life of spur gear can be significantly extended, reducing the total cost of ownership and increasing the reliability of the machinery they operate within. Regular maintenance not only helps in avoiding unexpected gear failures but also ensures optimal performance and efficiency of spur gear system.