Exploring the efficiency and performance improvements of helical gear in motion involves understanding how these gear operate and the various factors that impact their performance. Helical gear, with their unique design and tooth orientation, offer several advantages over traditional spur gear, leading to improvements in efficiency and overall performance in various mechanical systems.
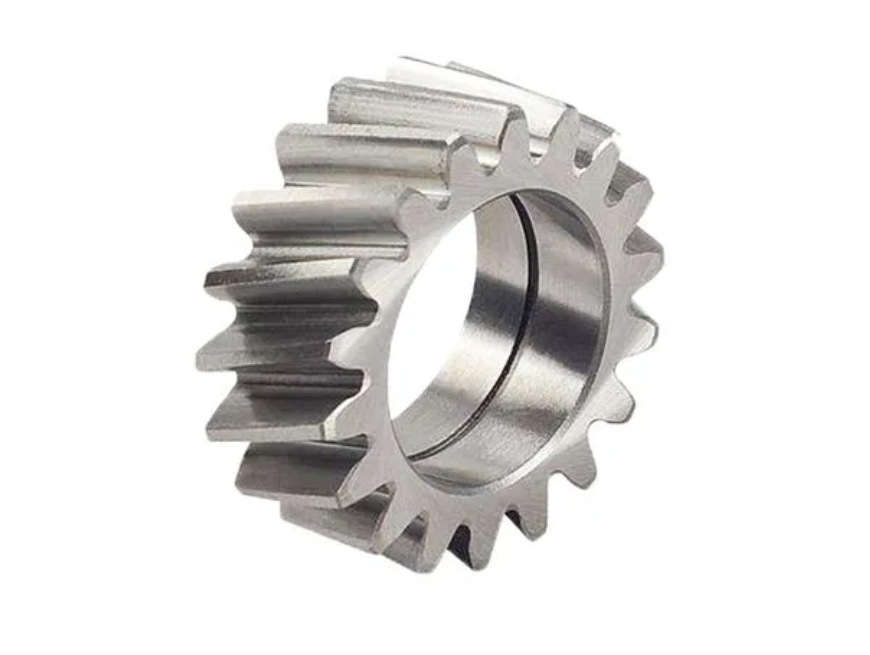
Efficiency of Helical Gears
- Gradual Engagement: Helical gear engage more gradually than spur gear, reducing the impact stress on gear teeth. This smoother operation leads to less vibration and noise, contributing to a more efficient helical gear system.
- Increased Load Distribution: The angled teeth of helical gear allow for more teeth to be in contact at any given time. This spreads the load across multiple teeth, reducing the stress on individual teeth and enhancing the gear’s ability to handle higher loads.
- Reduced Slipping: The helical design offers increased tooth contact area compared to spur gear, which reduces the chances of slipping, especially under high-load conditions.
Performance Improvements
- Higher Load Capacity: Due to the increased surface contact between teeth, helical gear can handle heavier loads compared to spur gear, allowing for the transmission of more power.
- Lower Noise Levels: The gradual engagement of teeth makes helical gear much quieter. This is particularly beneficial in applications where noise reduction is a priority, such as in automotive or consumer electronics.
- Suitability for High-Speed Applications: Helical gear is preferred in high-speed applications due to their smoother operation and ability to maintain stability and performance at higher rotational speeds.
Advanced Design and Manufacturing Techniques
- Optimized Tooth Design: Advances in helical gear design, including variable helix angles and modified tooth profiles, can maximize load distribution and minimize stress concentrations.
- Precision Manufacturing: Technologies like CNC machining and 3D printing enable the production of helical gear with extremely tight tolerances, ensuring smoother meshing and improved performance.
- Surface Treatments and Coatings: Implementing advanced coatings and surface treatments can reduce friction, wear, and tear, thereby enhancing the efficiency and longevity of helical gear.
Overcoming Efficiency Losses
While helical gear is generally more efficient than spur gear, they do have some drawbacks, such as:
- Axial Thrust: The helical design generates axial forces, which can be addressed by using appropriate thrust bearings to absorb these forces without compromising efficiency.
- Heat Generation: The sliding contact between teeth can generate more heat, which needs to be effectively managed through lubrication and cooling systems.
Applications
Helical gear is used in a wide range of applications where their advantages in load capacity, efficiency, and noise reduction are crucial, such as:
- Automotive Transmissions: For smooth operation and noise reduction.
- Industrial Machinery: Where reliability and power transmission efficiency are essential.
- Consumer Electronics: In devices like printers where quiet operation is valued.
In conclusion, helical gear offer significant efficiency and performance improvements due to their unique design. By leveraging advanced manufacturing techniques and materials, these improvements can be further enhanced, making helical gear a suitable choice for a wide range of applications, especially where noise reduction, higher load capacity, and high-speed operation are critical.