1. Experimental methods and data collection
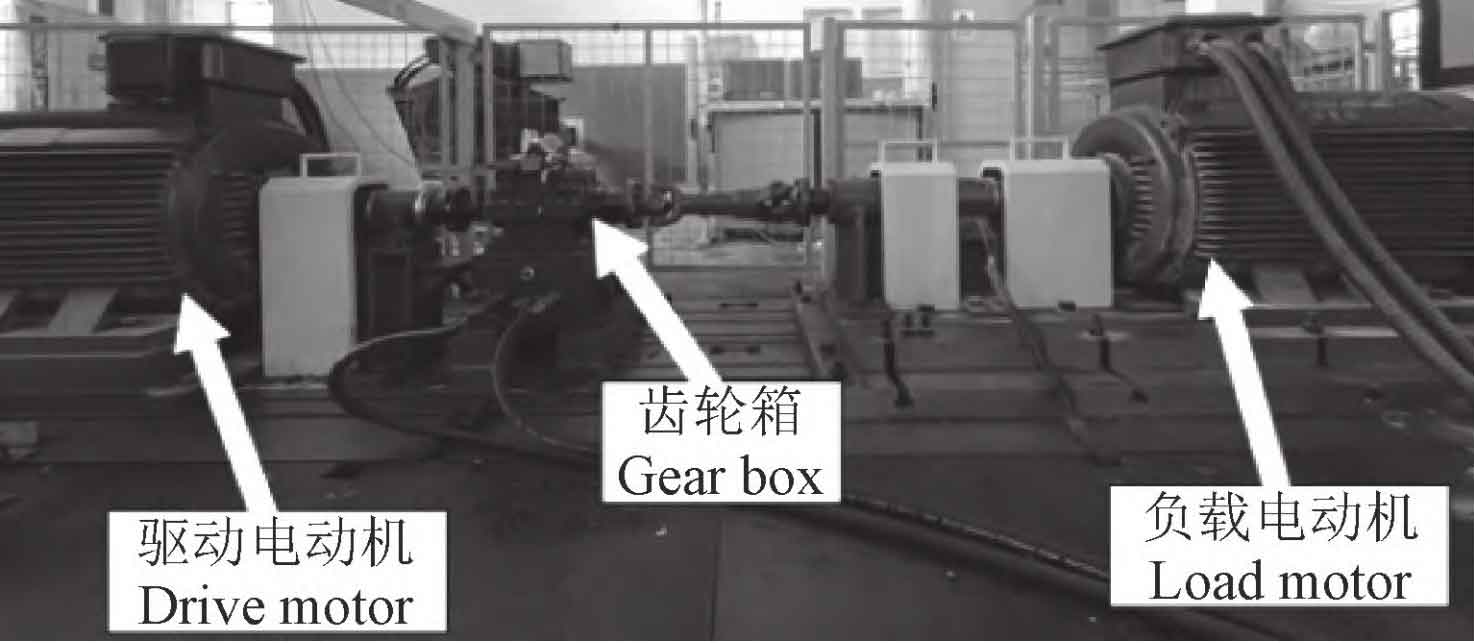
A helical gear pitting experimental platform (Figure 1) corresponding to the proposed dynamic model was constructed to verify the accuracy of the pitting fault helical gear dynamic model. Use a three-way vibration acceleration sensor with a sampling frequency of 12000 Hz to collect vibration acceleration signals at the input and output shaft end caps. The installation position is shown in Figure 2. The experimental conditions are 2500 r/min and an input torque of 240 N · m (output torque of 840 N · m).
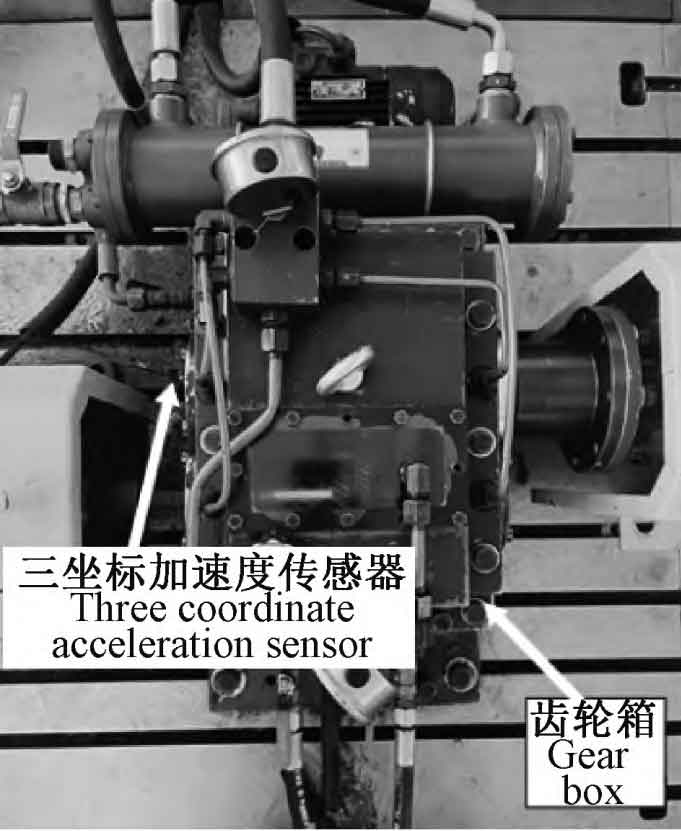
2. Analysis of experimental signals for different degrees of pitting on a single tooth surface
According to the proposed experimental method, the full life cycle vibration acceleration data of the helical gear was collected, and the data near the end cover of the faulty helical gear were analyzed in both time and frequency domains. The envelope spectrum analysis method was still used for frequency domain analysis.
In the time domain, analyze Figure 3, where the vibration acceleration of a normal helical gear [Figure 3 (a)] is stable without impact; The overall amplitude distribution of the vibration acceleration time-domain diagram of a helical gear with slight pitting on a single tooth surface [Figure 3 (b)] becomes sparse, and there is still no significant impact; The helical gear with severe pitting corrosion on a single tooth surface [Figure 3 (c)] showed an overall amplitude increase of 10% and a significant periodic impact with an impact period of 0 024 seconds, with the same rotation cycle as the faulty helical gear.
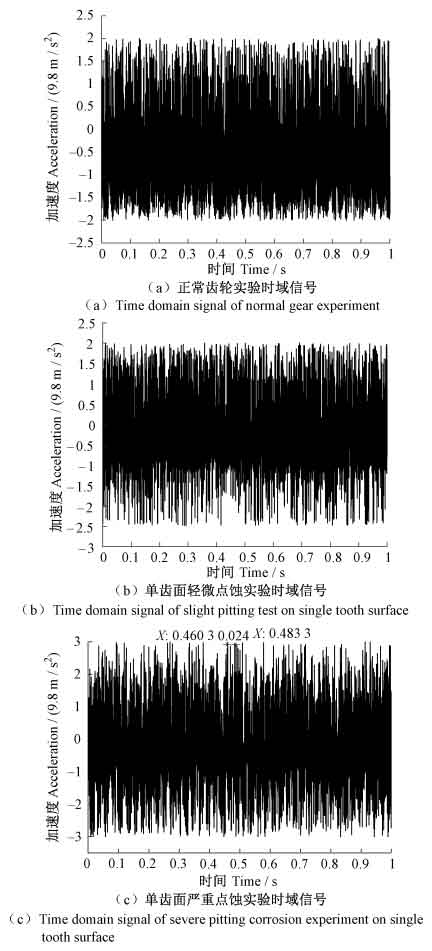
In the frequency domain, analyzing Figure 4, the normal helical gear [Figure 4 (a)] only shows significant peaks in the high-frequency region with a meshing frequency fm and twice the meshing frequency 2fm. For helical gears with slight pitting on a single tooth surface [Figure 4 (b)], significant peaks of rotational frequency fr, twice the rotational frequency 2fr, and three times the rotational frequency 3fr were observed in the low frequency range. In the high frequency range, sidebands with a difference of fr were observed near the meshing frequency fm and twice the meshing frequency 2fm. For helical gears with severe pitting on a single tooth surface [Figure 4 (c)], the phenomenon is basically consistent with slight pitting on a single tooth surface, but the number of sidebands is increasing, and the overall amplitude increases by 15%.
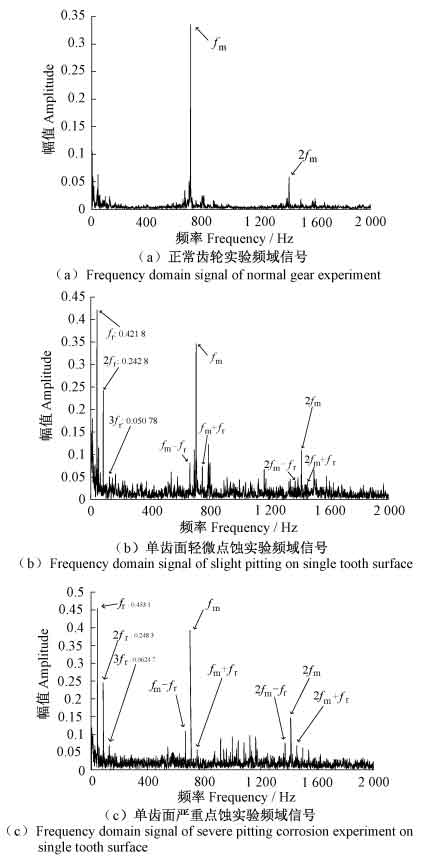
When the single tooth surface of the helical gear begins to experience pitting corrosion, from the frequency domain observation, the low-frequency region begins to exhibit 1, 2, and 3 times the rotational frequency, while the high-frequency region can observe the meshing frequency and 2 times the meshing frequency. The corresponding amplitude increases with the degree of pitting corrosion. Observing in the time domain, the overall amplitude is stable. Observing in the frequency domain, only the peak values of the meshing frequency in the high-frequency region and twice the meshing frequency can be observed, indicating that it is a normal helical gear; Observing the overall amplitude from the time domain to be stable, and observing from the corresponding frequency domain, except for the low-frequency region phenomenon, when there is a difference of 1 times the rotational frequency and other low amplitude sidebands near the meshing frequency and 2 times the meshing frequency in the high-frequency region, it is judged that slight pitting corrosion has occurred on the single tooth surface of the helical gear; From the time domain, it can be observed that there is a periodic impact on the overall amplitude, and the impact period is the same as the rotation period of the faulty helical gear. Observing the corresponding frequency domain, except for the low-frequency phenomenon, when there are a large number of high amplitude sidebands near the meshing frequency and twice the meshing frequency in the high-frequency region, it is judged that serious pitting corrosion has occurred on the single tooth surface of the helical gear.
3. Signal analysis of multi tooth surface pitting experiment
In the time domain, analyzing Figure 5, the vibration acceleration of the helical gear with double tooth surface pitting [Figure 5 (a)] is relatively denser than that of the helical gear with severe pitting on a single tooth surface [Figure 3 (c)], but periodic impacts can still be observed with an impact period of 0 024 seconds, corresponding to the rotation cycle of the faulty helical gear. The vibration acceleration of the helical gear with multiple tooth surface pitting corrosion [Figure 5 (b)] increased by 100% overall, reaching the maximum value of the entire life cycle of the experimental helical gear. The number of impacts increased and showed a periodic change, with a period of 0 At 024 seconds, the overall distribution became sparse.
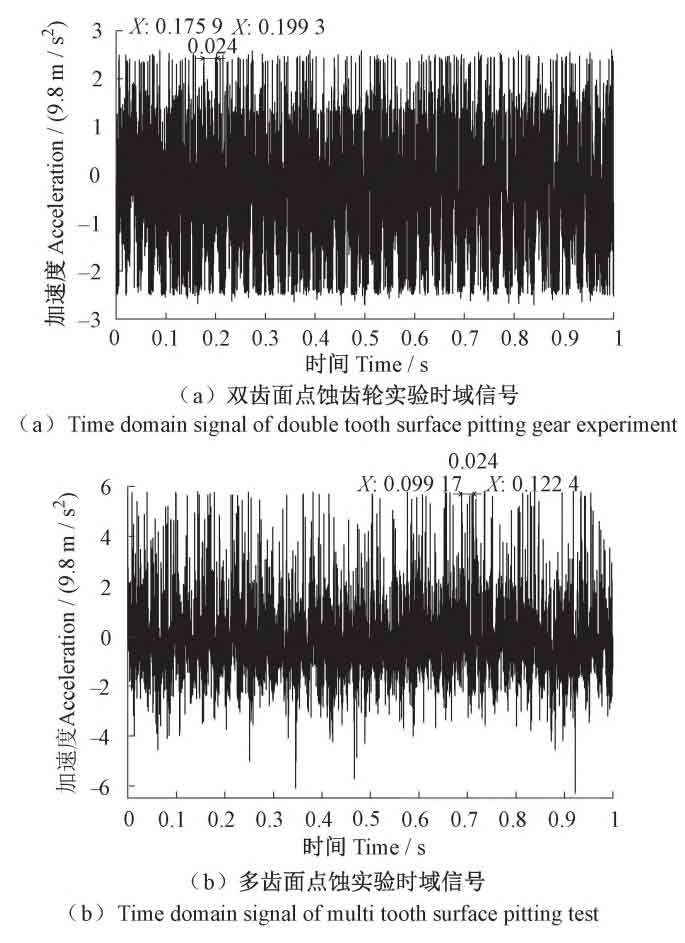
In the frequency domain, analyzing Figure 6, comparing the helical gears with double tooth surface pitting [Figure 6 (a)] and those with severe single tooth surface pitting [Figure 4 (c)], the amplitudes of the rotational frequencies fr, 2fr, and 3fr in the low frequency range increased by 12%, while the amplitudes of the meshing frequencies fm and 2fm in the high frequency range increased by 11%. The number of nearby sidebands increased and the amplitudes increased. The helical gear with multiple tooth surface pitting [Figure 6 (b)] shows a similar pattern of variation compared to the helical gear with double tooth surface pitting. In the high-frequency region, the number of sidebands near the meshing frequency fm and twice the meshing frequency 2fm reaches the maximum, and the amplitude reaches the maximum. When more than one tooth surface undergoes pitting, the number and amplitude of the sidebands between 0 and 800 Hz increase with the increase of the number of pitting tooth surfaces.
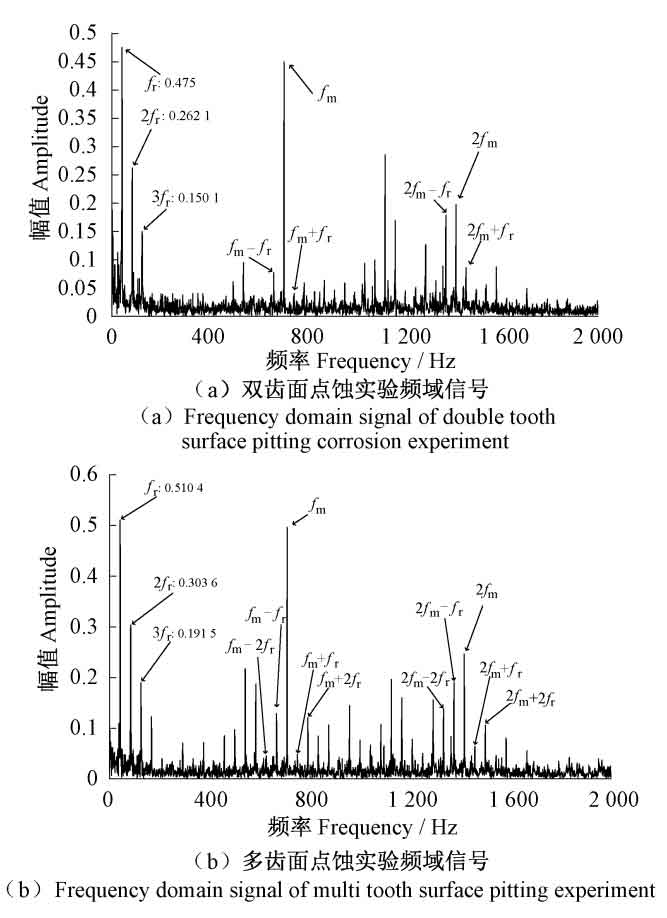
For multiple tooth surface pitting, by comparing simulation and experiments, if a significant number of target sidebands are found between 0 and 800 Hz, it can be determined that more than one tooth surface pitting has occurred. In the time domain, the double tooth surface pitting helical gear signal has a large and dense amplitude of large impacts. The impact period is the rotation period of the faulty helical gear, and the overall amplitude increases slightly compared to the amplitude of severe pitting on a single tooth surface; The time-domain signal of multi tooth surface pitting helical gears has a large number of sparsely distributed large amplitude impacts, and the impact period is the rotation period of the faulty helical gear, with the overall amplitude further increasing. In the frequency domain, the amplitude of the meshing frequency fm and twice the meshing frequency 2fm of helical gears with double tooth surface pitting corrosion decreases moderately compared to helical gears with severe pitting corrosion on a single tooth surface. However, the number and amplitude of nearby sidebands increase, and the amplitudes of fr, 2fr, and 3fr in the low-frequency region increase; The amplitude of the meshing frequency fm and twice the meshing frequency 2fm of the helical gear with multiple tooth surface pitting corrosion is significantly reduced compared to the helical gear with double tooth surface pitting corrosion. The amplitude of fr, 2fr, and 3fr in the low frequency range, as well as the number and amplitude of the sidebands near fm and 2fm, reach the maximum value of the entire lifecycle of the helical gear.
For pitting of two or more helical gear tooth surfaces, there will also be 1, 2, and 3 times the rotational frequency in the low-frequency region, and the corresponding amplitude will increase with the increase of the number of pitting tooth surfaces. When a large number of large and dense impacts occur in the time domain, and the impact period is the same as the rotation period of the faulty helical gear, observing the corresponding frequency domain, except for the basic phenomenon in the low-frequency region, it is found that a small number of sidebands begin to appear between the rotation frequency and the meshing frequency. The amplitude of the meshing frequency and twice the meshing frequency in the high-frequency region is relatively higher than that of a single tooth surface pitting corrosion, and there are many sidebands with higher amplitudes nearby, it can be concluded that double tooth surface pitting corrosion has occurred; When a large number of large and sparse impacts are observed in the time domain, and the impact period is the same as the rotation period of the faulty helical gear, phenomena other than the low-frequency region are observed in the corresponding frequency domain. It is found that a large number of high amplitude sidebands begin to appear between the rotation frequency and the meshing frequency, and the meshing frequency and twice the meshing frequency amplitude in the high-frequency region reach their highest values, When a large number of high amplitude sidebands appear nearby, it can be inferred that multiple tooth surface pitting corrosion of helical gears has occurred.