Manufacturing helical gear involves a series of processes that are more complex than those for spur gear, due to the helical angle of the teeth. This comprehensive review will cover the key steps and techniques used in the manufacturing of helical gear:
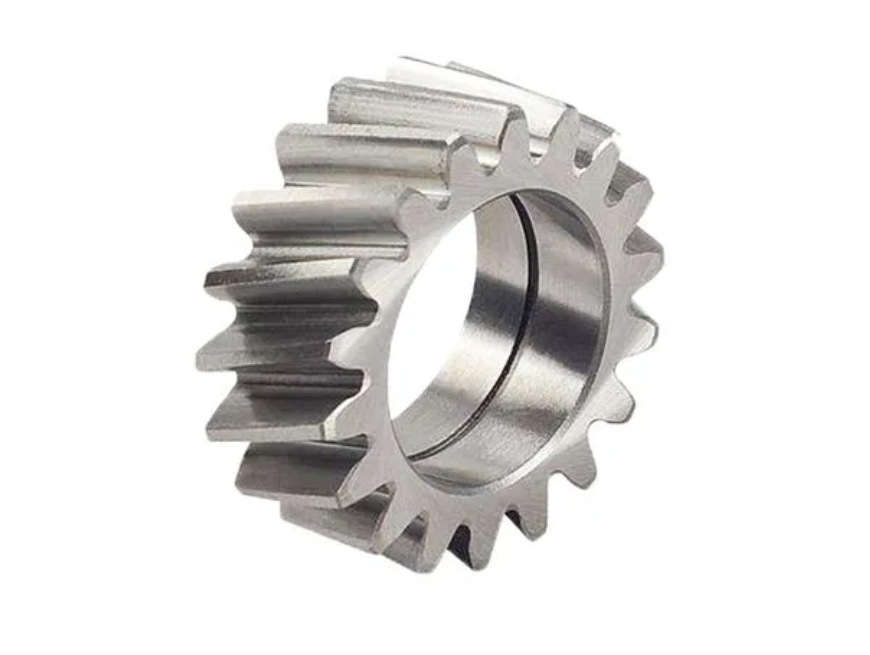
1. Gear Design and Planning
- Computer-Aided Design (CAD): Initial design of helical gear’s dimensions, tooth profile, and helix angle.
- Material Selection: Choosing appropriate materials based on helical gear’s intended application, load requirements, and environmental conditions.
2. Gear Blank Preparation
- Casting or Forging: Initial shaping of helical gear blank, usually through casting (for softer materials) or forging (for stronger metals).
- Machining: Rough machining of helical gear blank to get it close to the desired shape and size.
3. Tooth Cutting
- Hobbing: The most common method for cutting helical gear teeth. A hobbing machine uses a hob (a special milling cutter) to cut the helical teeth into helical gear blank.
- Milling: Sometimes used for lower volume or special gear. It involves using a milling cutter to shape the teeth.
4. Tooth Finishing
- Shaving: A finishing process to improve the precision and surface finish of helical gear teeth.
- Grinding: Used for higher precision and smoother finish, particularly for helical gear that require a high degree of accuracy and smoothness.
5. Heat Treatment
- Case Hardening: Heating helical gear in a carbon-rich environment and then quenching it, which makes the surface layer harder.
- Induction Hardening: Using electromagnetic induction to heat the surface layer, followed by rapid cooling.
6. Surface Treatments and Coating
- Nitriding: Introducing nitrogen into the surface layer to increase hardness and wear resistance.
- Coating: Applying layers such as chromium or nickel for added durability and corrosion resistance.
7. Gear Teeth Grinding and Lapping
- Grinding: For achieving high accuracy and finish.
- Lapping: A process where two gears are run together with a lapping compound to improve the surface finish and fit of the teeth.
8. Quality Control and Inspection
- Dimensional Checks: Ensuring helical gear dimensions are within the specified tolerances.
- Surface Inspection: Checking for defects like cracks or imperfections on helical gear teeth.
- Performance Testing: Assessing helical gear’s performance under simulated working conditions.
9. Post-Treatment Processes
- Deburring: Removing any burrs or sharp edges left after the cutting process.
- Cleaning and Protective Coatings: Applying protective coatings to prevent rust and corrosion.
Conclusion
The manufacturing process of helical gears is intricate and requires precise control at each step to ensure the quality and performance of the final product. The choice of manufacturing method often depends on factors like helical gear’s size, required precision, material, and the intended application. Advances in manufacturing technologies, such as CNC machining and 3D printing, are continually refining these processes, allowing for more complex and precise gear designs.