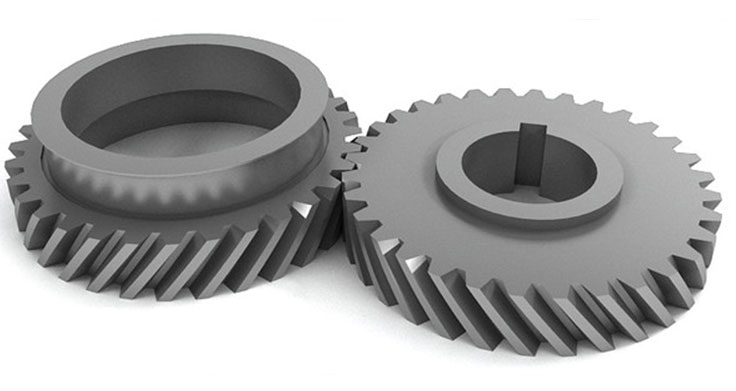
Helical gears are a type of cylindrical gears widely used in various applications to transmit rotational motion and power between parallel shafts. They offer several advantages over other gear types, including smooth operation, higher load-carrying capacity, and reduced noise. Here’s a comprehensive guide to their function and design:
1. Function of Helical Gears:
- Helical gears function by meshing their helical teeth together, resulting in the transfer of rotational motion and torque between two parallel shafts. The helix angle of the teeth allows for gradual engagement, providing smooth and quiet operation compared to straight-cut gears.
2. Helix Angle and Direction:
- The helix angle is the angle formed by the tooth helix and the gear axis. It determines the type of helical gear: left-hand helical gears have a helix angle that rotates counterclockwise, while right-hand helical gears have a helix angle that rotates clockwise.
3. Advantages of Helical Gears:
- Smooth Operation: The gradual engagement of helical gears reduces noise, vibration, and impact forces during meshing, leading to smoother operation.
- Higher Load Capacity: The helical tooth design allows multiple teeth to be in contact simultaneously, distributing the load over a larger area, resulting in improved load-carrying capacity.
- Efficiency: Helical gears generally have higher efficiency compared to other gear types due to reduced sliding friction and improved load distribution.
- Parallel Shaft Configuration: Helical gears are suitable for transmitting power between parallel shafts.
4. Helical Gear Design Considerations:
- Pitch Diameter: The pitch diameter is the diameter at which the gear teeth effectively engage. It determines the gear ratio and must be carefully calculated to achieve the desired transmission characteristics.
- Module (Metric) or Diametral Pitch (Imperial): The module or diametral pitch defines the size of the gear teeth and is crucial for meshing compatibility between gears.
- Number of Teeth: The number of teeth affects the gear ratio and influences the gear’s strength and smoothness of operation.
- Pressure Angle: The pressure angle is the angle between the tooth force vector and the line perpendicular to the gear’s axis. The most common pressure angle for helical gears is 20 degrees.
- Helix Angle: The helix angle influences the gear’s load-carrying capacity, efficiency, and direction of rotation.
5. Manufacturing and Machining:
- Helical gears are commonly manufactured using hobbing, a process that involves using a hob cutter to create the gear teeth. Gear grinding is also employed for high-precision gear finishing.
- The helix angle must be accurately generated during the manufacturing process to ensure proper gear meshing and performance.
6. Lubrication and Maintenance:
- Adequate lubrication is essential to reduce friction, wear, and noise in helical gears. The use of high-quality lubricants and proper maintenance ensures optimal gear performance and longevity.
7. Applications:
- Helical gears find application in a wide range of industries, including automotive transmissions, industrial machinery, robotics, aerospace systems, and more, where smooth operation, high efficiency, and reliability are required.
Helical gears are versatile components that provide smooth, efficient, and reliable power transmission in various applications. Their design considerations, manufacturing techniques, and lubrication play crucial roles in achieving optimal gear performance. As a result, helical gears are widely adopted in modern engineering for their numerous advantages over other gear types.