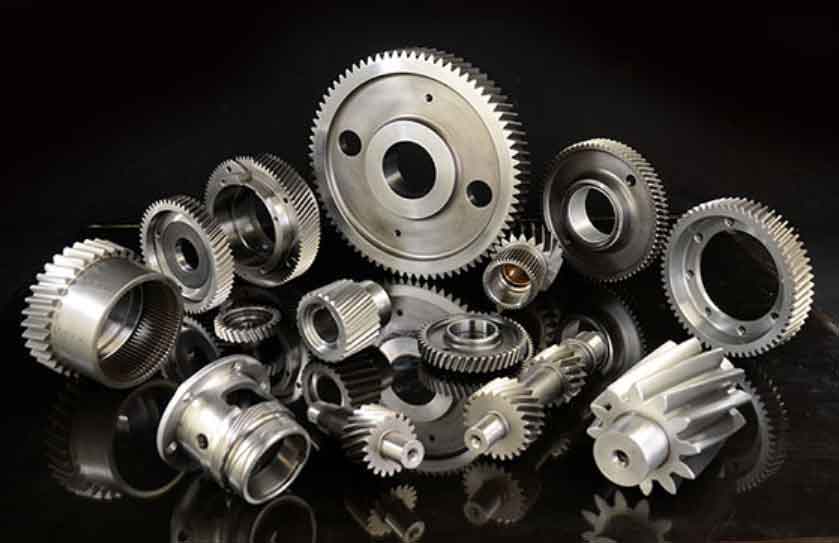
Optimizing gear meshing is crucial for smooth and efficient operation of helical gears. Here are some tips to achieve this:
- Accurate Gear Design: Ensure precise gear design, including the helix angle, module, number of teeth, and tooth profile. Accurate design minimizes the risk of interference and ensures proper meshing between the gears.
- Proper Gear Alignment: Align the helical gears accurately to avoid misalignment issues. Misalignment can lead to increased noise, vibration, and reduced gear life. Proper alignment is critical for efficient power transmission.
- Gear Tooth Profile and Finish: Use high-quality gear cutting tools and machinery to achieve precise gear tooth profiles. A smooth surface finish reduces friction and wear, enhancing gear performance and efficiency.
- Appropriate Lubrication: Choose the right lubricant for the application and ensure proper lubrication of the gear teeth. Adequate lubrication reduces friction and heat, improving gear efficiency and extending the gear’s lifespan.
- Gear Preload Adjustment: In some cases, adjusting the gear preload can optimize gear meshing. Proper preload ensures proper tooth engagement and minimizes backlash.
- Avoid Overloading: Helical gears have a higher load-carrying capacity, but overloading can still lead to premature failure. Avoid excessive loads and ensure the gears are operating within their design limits.
- Minimize Backlash: Keep backlash to a minimum to reduce play between gear teeth during meshing. Low backlash improves precision and reduces noise in gear operation.
- Surface Hardening: Consider surface hardening or heat treatment of gear teeth to enhance wear resistance and reduce the risk of pitting and scoring.
- Vibration Damping: Implement effective vibration damping techniques to minimize vibration and noise during gear operation. Vibration can lead to accelerated wear and reduced gear performance.
- Regular Maintenance: Regularly inspect and maintain helical gears to detect any wear or damage early. Timely maintenance can prevent serious issues and extend the gears’ life.
- Avoid Excessive Speeds: Operating helical gears at excessively high speeds can lead to increased noise and wear. Ensure the gears are operated within their recommended speed limits.
- Use High-Quality Gears: Work with reputable gear manufacturers that produce high-quality gears with precise tolerances and excellent materials.
By implementing these tips, you can optimize the gear meshing of helical gears, resulting in smoother and more efficient gear operation, reduced wear, and extended gear life. This, in turn, enhances the overall performance of the machinery or equipment where the helical gears are used.