Using ansys12 0 finite element analysis software to analyze the contact stress of gear surface in the process of gear meshing.
Due to the structural shape and bearing characteristics of helical gear, and the meshing contact line of gear teeth is inclined line, the load of meshing line is non-uniform distribution. It is obviously not suitable to use two-dimensional finite element method to analyze the contact of helical gear, and three-dimensional model must be used for analysis. After the solid model is imported into ANSYS, the model needs to be divided into finite element mesh for finite element analysis.
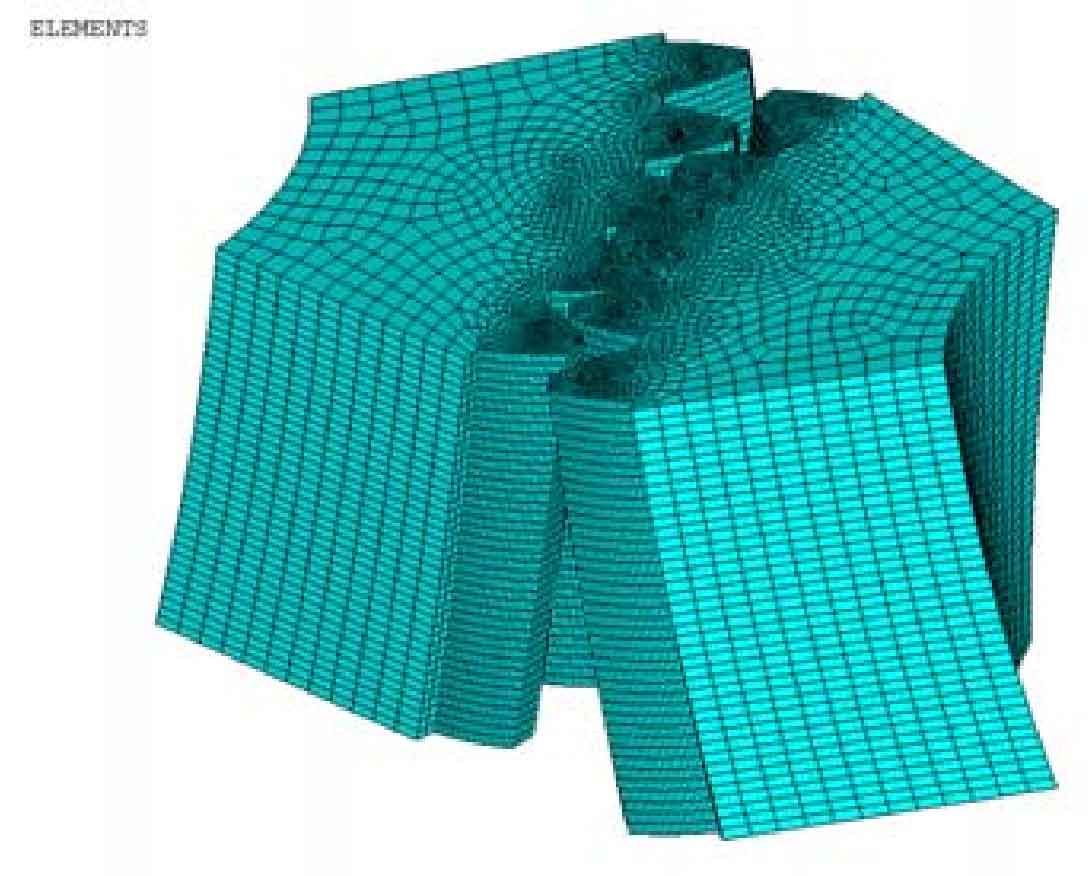
Because the helical gear tooth profile is an involute helical surface, the pre-processing function of ANSYS is limited, and the grid quality plays a vital role in the contact simulation of helical gear. HyperMesh has good speed, adaptability and customization in dealing with the efficiency and quality of geometric model and finite element grid, and the model scale is not limited by software. Many other finite element pre-processing software take a long time to read the data for some complex and large-scale models, and in many cases, they can not successfully import the model, resulting in the failure of subsequent CAE analysis.
HyperMesh can quickly read the model data with very complex structure and large scale, which greatly improves the work efficiency of CAE analysis engineers, and makes many problems that are difficult or can not be solved by other pre-processing software easily. Therefore, this paper uses HyperMesh software to mesh its solid model.