1. Establishment of dynamic contact model and meshing
The solid model is imported into HyperMesh for meshing. The mesh model is shown in Figure. Finally, the divided mesh model is directly imported into ANSYS / LS-DYNA software.
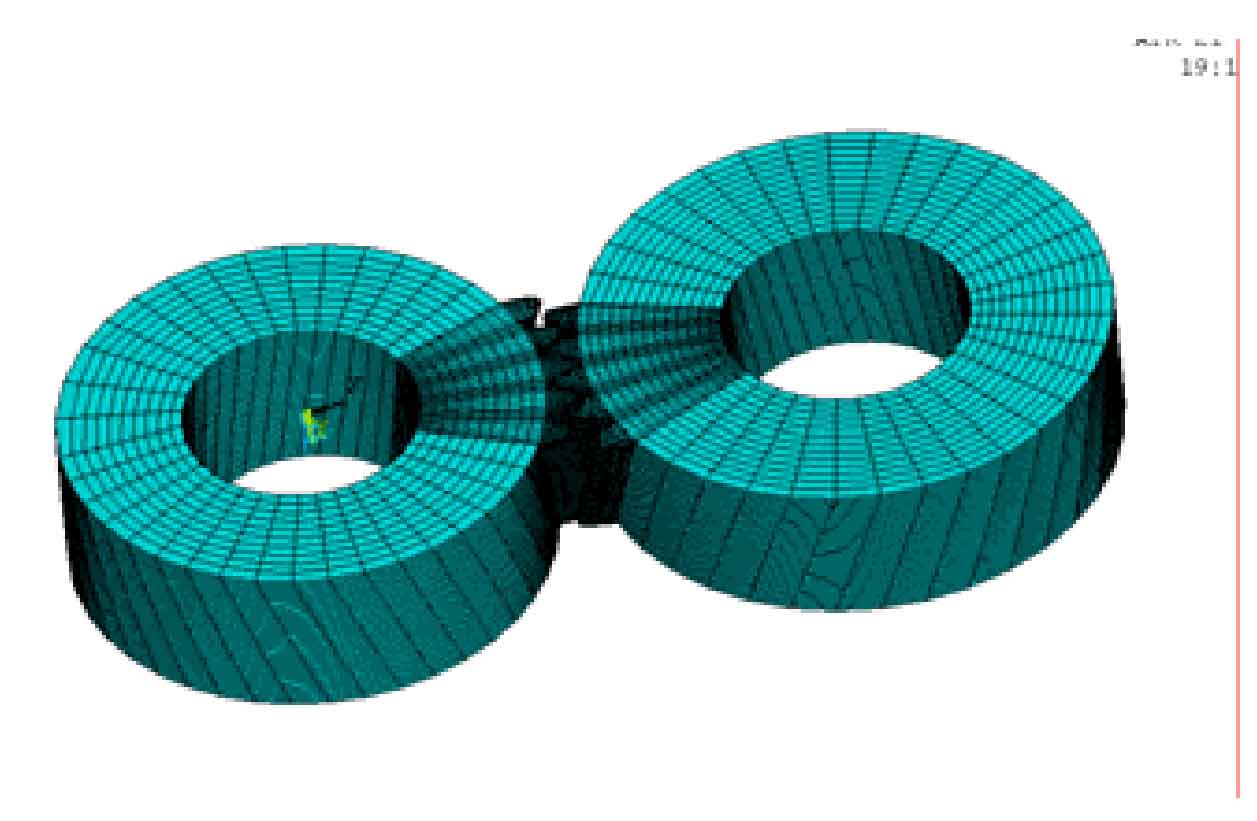
2. Define unit type, real constant and material properties
The solid element selected in the dynamic contact analysis is solid164, and the element is set as a full integral element to avoid hourglass. Solid164 element is an 8-node hexahedral element. In order to reduce the calculation time and improve the work efficiency, the helical gear solid model is defined as a rigid body in ANSYS / LS-DYNA, because the degrees of freedom of all nodes in the rigid body will be coupled to the center of mass of the rigid body. No matter how many nodes are defined by the rigid body, the rigid body has only 6 degrees of freedom. The mass, center of mass and inertia of all rigid bodies are automatically calculated by the volume of rigid bodies and the density of materials. The force and moment acting on the rigid body are synthesized by the node force and moment in each time step, and then the motion of the rigid body is calculated. The displacement of the node is converted by the displacement and rotation angle of the rigid body center. Since solid164 element has no rotational freedom, it cannot be directly applied with speed and torque to rotate the helical gear for contact analysis. In order to facilitate the application of speed and torque, shell163 element is used to divide the inner ring of helical gear and define it as a rigid body. Shell163 element is a thin shell element with 4-node display structure. There are 12 algorithms. Different algorithms are defined with different keyopt (1) values, In this paper, the fastest s / R Hughes Liu in-plane multi integral point improved element algorithm is selected. Because it can reasonably explain distortion and other deformation, simplified integral can be selected instead of one point integral controlled by hourglass.
Solid164 has no real constant. Shell163 provides the following real constants: sHRF is the shear factor, 5 / 6 is recommended, and the default value is 1; Nip is the integral point value through the thickness of the element, the maximum value is 100, and the default value is 2; T1-T4 is the shell thickness at each of the four nodes. In this paper, shell163 element is set as uniform thickness, the thickness at the node is defined as 0.05mm, and shrl is 5 / 6.
The material properties of the helical gear are the same as those in table 1.3. For shell163 rigid body element, when setting material properties, it is necessary to set its translation and rotation constraint parameters at the same time. For the two helical gears, select translation constraint parameter-7 (constraining displacement in X, y and Z directions) and rotation constraint parameter-4 (constraining rotation in X and Y directions) respectively to realize that the helical gear has only rotational degrees of freedom.
3. Defining part
In ANSYS / LS-DYNA, a group of elements with the same element, real constant and material number are given a part number. The later definition of helical gear contact, the constraints of boundary conditions and the application of load are created under different parts.
4. Defining contact
There is no contact element in ANSYS / LS-DYNA. Just define the possible contact surface, the contact type between them and some parameters related to the contact. In the process of program calculation, it can ensure that the contact interfaces do not penetrate each other. At the same time, when the contact interface has relative movement, the effect of friction is considered.
LS-DYNA divides all contact types into the following three categories: single-sided contact, point-to-surface contact and surface-to-surface contact. It has been analyzed and determined to select the type of surface to surface contact. Due to the space relationship, only normal and automatic contact are introduced below. The difference between the two lies in the different treatment of the contact force of the shell element. When calculating the contact force, the ordinary contact does not need to consider the thickness of the shell. The calculation speed is fast and reliable. When using, it only needs to care about the direction of the contact surface. The direction of the contact surface defines which side of a surface is the real body and which side is the void.
The automatic contact allows the contact to appear on both sides of the shell unit, automatically determines the direction of the contact surface of the shell unit, and automatically checks each side of the shell unit. Due to the complexity of helical gear contact analysis, it is sometimes very difficult to judge the direction of contact, so automatic contact should be used as much as possible. The contact type selected in this paper is automatic contact in surface to surface contact – asts (automatic surface to surface contact), static friction coefficient, dynamic friction coefficient and other settings adopt their default settings.
5. Applied load
In ANSYS / LS-DYNA, the application of load is different from static contact. Array parameters need to be established before loading the structure. Array parameters are the collection of time interval and corresponding load values. It is composed of two parts: time interval and load value corresponding to time interval. According to the load of helical gear under normal working conditions, the driving wheel has angular speed and the driven wheel has resistance torque. Therefore, to apply constant speed on the driving wheel and constant load torque on the driven wheel, plus time array, three array parameters need to be defined: angular speed, torque and time array. Once the load in the direction of 33.01m/s of the circular element model is applied to the inner ring, the load in the direction of 33.01m/s of the inner ring can be applied to the driving wheel respectively.
6. Analysis and solution
In the simulation analysis of helical gear meshing dynamic contact, considering that sudden speed and torque will usually make the calculation process unstable, the loading process is assumed to be completed within a period of time, and the calculation time is 0.05s.
ANSYS / LS-DYNA can connect ANSYS post-processing POST1 and post26, and can also connect ls-prepare of LS-DYNA post-processing. because. Rst file capacity is very large. In order to use ls-prepost post-processing software, this paper only outputs binary files for ls-prepost. After completing the pre appeal processing setting, use the solver of LS-DYNA to directly solve the output K file. After solving, read the result file under the ls-prepare post processor to view the calculation results and export the meshing video file of helical gear.