Helical gears strike a balance between performance and durability, making them well-suited for a wide range of gear applications. They offer several key features that contribute to their performance and durability:
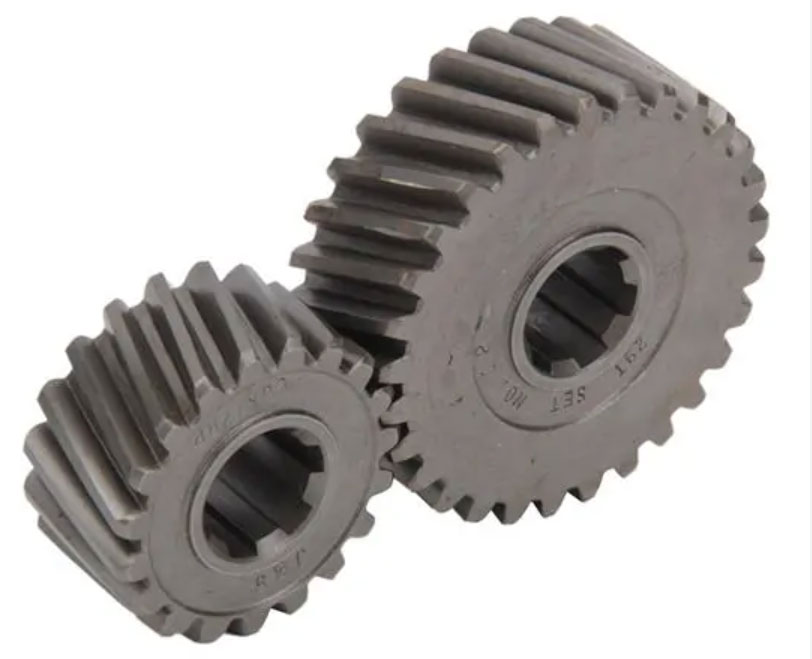
1. Load Distribution:
The helical tooth profile of helical gears allows for multiple teeth to be in contact at any given time, distributing the load over a larger area. This load distribution capability reduces stress concentrations on individual teeth, resulting in improved durability and resistance to wear.
2. Smooth Operation:
The helical tooth design of helical gears facilitates a gradual tooth engagement, resulting in smoother and quieter operation compared to gears with straight teeth. The smooth meshing action minimizes impact forces and vibrations, reducing the risk of gear damage and enhancing durability.
3. Increased Tooth Contact:
Helical gears provide increased tooth contact compared to gears with straight teeth, such as spur gears. The helical tooth profile allows for greater contact area between the mating gears, which distributes the load more evenly. This increased tooth contact contributes to improved load-carrying capacity and reduced tooth stresses, enhancing the durability of the gears.
4. Axial Thrust Management:
Helical gears can be designed with a specific helix angle to manage the axial thrust generated during operation. By carefully selecting the helix angle, designers can balance or offset the axial thrust, reducing the need for additional thrust bearings and minimizing the associated wear and tear.
5. High Torque Transmission:
Helical gears are capable of transmitting high torque due to their inclined tooth profile and increased tooth contact. The inclined teeth distribute the load over multiple teeth, enabling efficient power transmission and reducing the risk of tooth failure or breakage under heavy loads.
6. Material Selection and Heat Treatment:
The choice of materials and appropriate heat treatment processes play a crucial role in enhancing the performance and durability of helical gears. High-quality materials with good strength, hardness, and wear resistance are selected to withstand the demanding conditions of gear applications. Heat treatment processes, such as carburizing or induction hardening, further enhance the surface hardness and wear resistance of the gear teeth.
7. Lubrication and Maintenance:
Proper lubrication is essential for maximizing the performance and durability of helical gears. Lubricants help reduce friction, minimize wear, dissipate heat, and protect against corrosion. Regular maintenance, including lubricant inspection and replacement, gear inspection, and alignment checks, ensures the gears continue to operate optimally and extends their service life.
By balancing performance and durability, helical gears offer reliable and long-lasting operation in various gear applications. Their load distribution capabilities, smooth operation, increased tooth contact, axial thrust management, high torque transmission, appropriate material selection, and proper lubrication contribute to their overall performance and durability. Whether in automotive, industrial, aerospace, or other applications, helical gears provide a reliable and durable solution for efficient power transmission.