Noise and vibration reduction are critical considerations in gear systems, as excessive noise and vibration can lead to reduced efficiency, increased wear, and potential damage to the equipment. Spiral bevel gears offer several solutions to address these challenges and provide a quieter and smoother gear operation. Here’s how spiral bevel gears contribute to noise and vibration reduction:
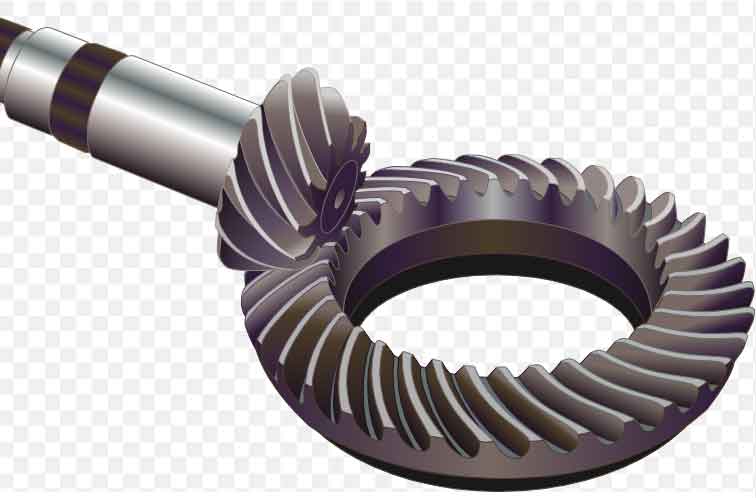
1. Curved Tooth Profile: The curved tooth profile of spiral bevel gears allows for gradual and continuous tooth engagement as the gears mesh. This results in a more gentle and uniform distribution of forces, reducing sudden impacts and minimizing gear rattle, which are common sources of noise and vibration in straight bevel gears.
2. Smooth Operation: The continuous engagement of the teeth in spiral bevel gears leads to smoother operation. The gradual transfer of load between the teeth reduces abrupt changes in contact forces, thereby lowering vibrations and noise levels during gear meshing.
3. Axial Overlap: Spiral bevel gears typically have axial overlap, where multiple teeth are in contact simultaneously. This axial overlap results in smoother load transfer during gear meshing, reducing the likelihood of gear teeth slamming into each other and generating noise.
4. Reduced Sliding Friction: The curved tooth profile of spiral bevel gears allows for a rolling action during meshing, reducing sliding friction between the gear teeth. Lower sliding friction leads to less wear and heat generation, which can contribute to quieter gear operation.
5. Precision Manufacturing: The manufacturing process of spiral bevel gears involves high-precision machining techniques, resulting in accurate tooth profiles and gear geometry. Well-matched gears with precise tooth profiles lead to better gear meshing and reduced noise generation.
6. Quality Materials and Heat Treatment: Using high-quality materials and applying appropriate heat treatment processes ensures that spiral bevel gears have the required hardness and durability to withstand loads without excessive wear or deformation, further reducing noise and vibration levels.
7. Gear Mesh Alignment: Proper alignment of the spiral bevel gears is crucial to minimize misalignment and ensure even contact along the gear teeth. Proper alignment reduces tooth edge loading and contributes to quieter gear operation.
8. Lubrication and Maintenance: Using appropriate lubrication and regular maintenance help maintain optimal gear performance and reduce noise levels by preventing excessive wear and ensuring smooth gear operation.
9. Damping Techniques: In some cases, additional damping techniques, such as the use of vibration-damping materials or isolators, can further reduce gear noise and vibration in specific applications.
The curved tooth profile, smooth operation, precision manufacturing, and other design considerations in spiral bevel gears make them effective solutions for noise and vibration reduction in gear systems. Their ability to provide quieter and smoother gear meshing enhances overall equipment performance, efficiency, and reliability in various industrial applications.