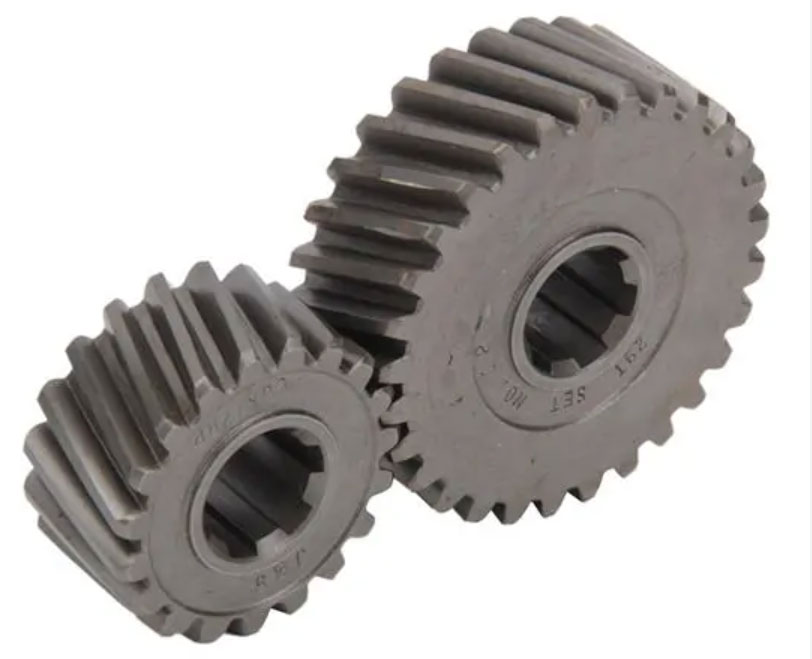
Helical gears are essential elements in heavy machinery and industrial equipment due to their ability to handle high loads, transmit power efficiently, and provide smooth operation. They play a critical role in various industrial applications, enabling the reliable and precise operation of heavy machinery. Let’s explore why helical gears are essential in heavy machinery and industrial equipment:
1. Load Handling Capability:
Helical gears are designed to handle heavy loads and transmit high torque. The inclined tooth profile and increased contact area allow for efficient load distribution across multiple gear teeth. This load-handling capability makes helical gears suitable for heavy-duty applications such as mining equipment, construction machinery, steel mills, and material handling systems.
2. Power Transmission Efficiency:
Helical gears offer high power transmission efficiency. The inclined tooth engagement reduces sliding friction, resulting in less power loss compared to other gear types. This efficiency is crucial in heavy machinery and industrial equipment, where maximizing power transfer and minimizing energy waste are important for overall system performance and productivity.
3. Smooth Operation:
The gradual tooth engagement of helical gears provides smooth and quiet operation. Unlike spur gears that experience sudden tooth impact during meshing, helical gears engage gradually, reducing noise and vibration. This is especially beneficial in heavy machinery and industrial equipment where smooth operation is essential for precision, safety, and operator comfort.
4. Durability and Reliability:
Helical gears are known for their durability and reliability in demanding industrial environments. They are designed to withstand heavy loads, shock loads, and harsh operating conditions. High-quality materials, precision manufacturing processes, and stringent quality control ensure the longevity and performance of helical gears, making them reliable components in heavy machinery and industrial equipment.
5. Versatility in Gear Arrangements:
Helical gears offer versatility in gear arrangements, allowing for various configurations to suit specific industrial applications. They can be used in parallel shaft arrangements, crossed-axis arrangements, or right-angle configurations. This flexibility in design enables engineers to optimize gear systems for different machinery layouts and space constraints.
6. Precision Control and Positioning:
In industrial equipment that requires precision control and positioning, such as robotics, CNC machines, or automated manufacturing systems, helical gears deliver accurate motion control. The gradual tooth engagement and smooth operation ensure precise gear shifting, accurate positioning, and consistent performance, enhancing the overall efficiency and productivity of the equipment.
7. Reducing Backlash:
Helical gears have overlapping tooth engagement, which helps reduce backlash. Backlash is the play or clearance between mating gear teeth, and it can lead to inaccuracies in motion and positioning. The overlapping engagement of helical gears minimizes backlash, ensuring better control, improved accuracy, and repeatability in heavy machinery and industrial equipment.
The robustness, efficiency, and smooth operation of helical gears make them essential elements in heavy machinery and industrial equipment. Their load-handling capability, power transmission efficiency, durability, and precision control contribute to reliable and high-performance operation. By incorporating helical gears, engineers can ensure the optimal functioning of heavy machinery and industrial equipment in various industries, enhancing productivity, safety, and overall operational efficiency.