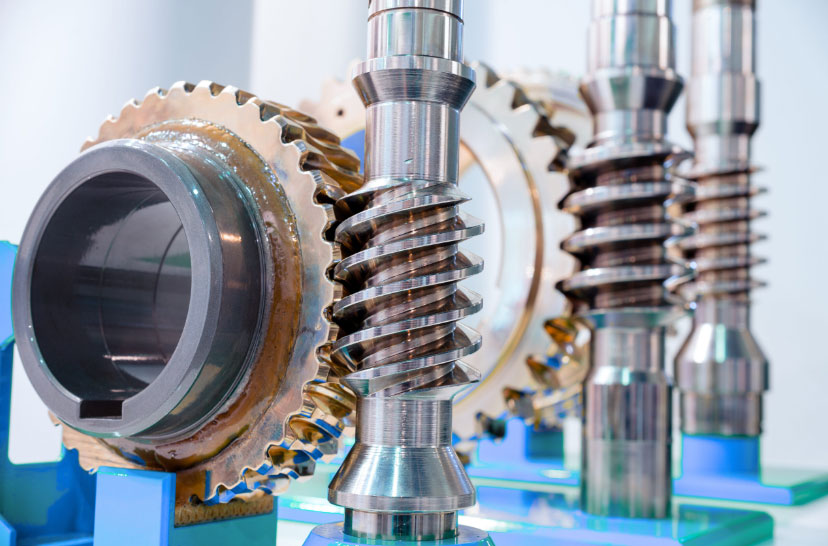
Helical gears are essential components in modern machinery and play a critical role in transmitting power and motion between rotating shafts. They are a type of gear with helical teeth, meaning the teeth are cut at an angle to the gear’s axis, forming a helix shape. This design allows for smoother and quieter operation compared to spur gears (gears with straight teeth) and also provides higher load-carrying capacity and efficiency.
Precision engineering is of paramount importance when it comes to helical gears. Achieving accurate gear profiles, tooth spacing, and alignment is crucial to ensure smooth and efficient power transmission and to minimize wear and noise during operation. Here are some key aspects of precision engineering in relation to helical gears:
- Gear Design and Calculation: Precision engineering starts with the design and calculation of the gear system. Engineers use advanced software and tools to determine the appropriate gear size, number of teeth, helix angle, and other parameters based on the application’s requirements and load conditions.
- Gear Manufacturing: The manufacturing process is critical in achieving precision in gear production. CNC (Computer Numerical Control) machines and other advanced manufacturing techniques are used to produce high-quality gears with accurate tooth profiles and spacing. Precision machining ensures the gears mesh correctly, minimizing noise and increasing efficiency.
- Material Selection: Choosing the right material for gear manufacturing is essential. High-strength and wear-resistant materials, such as alloy steels, are commonly used for helical gears to ensure they can withstand the stresses of heavy-duty applications.
- Heat Treatment: After manufacturing, the gears undergo heat treatment processes like carburizing or induction hardening to increase their surface hardness and wear resistance while maintaining the core’s toughness.
- Gear Inspection and Quality Control: Quality control processes, including gear inspection, are critical to ensure that the gears meet the required specifications and tolerances. Gear inspection involves various techniques like coordinate measuring machines (CMM), gear analyzers, and gear testers to check tooth profile, pitch, runout, and backlash.
- Lubrication: Proper lubrication is essential to reduce friction and wear between gear teeth during operation. Precision engineering also involves selecting the appropriate lubricant for specific applications to optimize gear performance and extend their service life.
- Noise and Vibration Control: Helical gears inherently produce less noise compared to spur gears due to their helical tooth arrangement. However, precision engineering further helps in reducing noise and vibrations through careful design and manufacturing practices.
Helical gears are vital components in modern machinery, and precision engineering plays a fundamental role in ensuring their performance, reliability, and longevity. By using advanced design and manufacturing techniques, engineers can create helical gears that meet the highest standards of quality, enabling the efficient operation of various machines across industries like automotive, aerospace, manufacturing, and more.