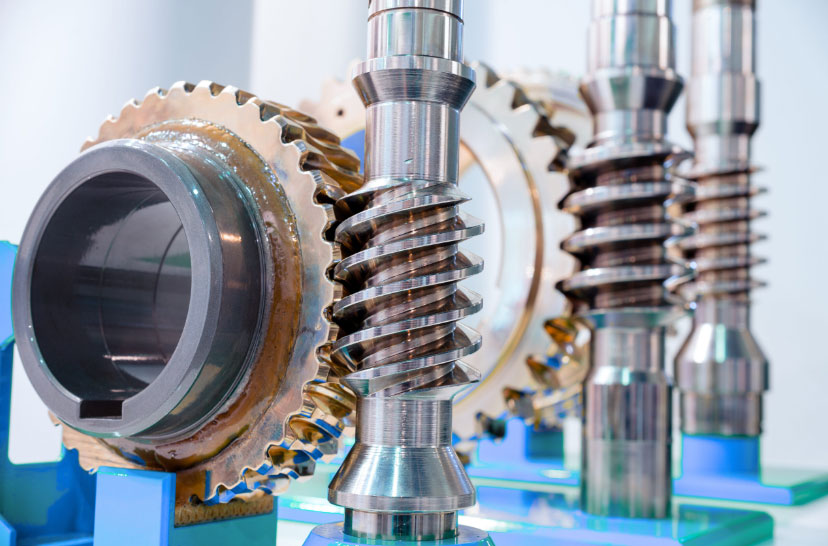
Helical gears are a type of mechanical gear used in various applications to transmit power between shafts. They are particularly effective in handling heavy loads and high torque due to their unique design. Unlike spur gears, which have straight teeth and engage abruptly, helical gears have angled teeth that gradually engage with each other. This design feature offers several advantages, making them suitable for heavy-duty applications:
- Increased contact area: The helical gear’s angled teeth create a larger contact area between the mating gears compared to spur gears. This enhanced contact allows for a more efficient transfer of torque and helps distribute the load over a broader surface area, reducing stress on individual teeth.
- Smoother engagement: The gradual engagement of helical gears leads to a smoother and quieter operation. This gradual contact reduces noise and vibration, which is essential when dealing with heavy loads and high torques that can amplify these issues in spur gears.
- Higher load-carrying capacity: Due to the larger contact area and improved tooth engagement, helical gears can withstand heavier loads and transmit higher torques without compromising performance.
- Better alignment: Helical gears tend to self-align during operation, which helps maintain a consistent and proper meshing of the teeth. This self-alignment ability is especially beneficial when dealing with heavy loads that might cause misalignment issues in other gear types.
- Improved efficiency: Although helical gears experience slightly higher axial and radial forces due to the helix angle, their improved load distribution and smoother engagement result in higher overall gear efficiency. The increased efficiency is essential for heavy-load applications, as it helps reduce energy losses and heat generation.
While helical gears are excellent for handling heavy loads and high torques, they do have some drawbacks. The main challenges associated with helical gears are higher manufacturing costs and axial thrust, which requires the use of thrust bearings to counteract the axial forces generated during operation. Additionally, due to the helical angle, the axial forces may cause some axial sliding, leading to slight axial movement of the gear along the shaft during operation.
Overall, helical gears are a reliable and preferred choice for applications that require handling heavy loads and high torque, such as heavy machinery, industrial equipment, and automotive transmissions.