Helical gears offer several advantages and disadvantages in their design, making them suitable for specific applications while posing challenges in others. Let’s explore the key advantages and disadvantages of helical gears:
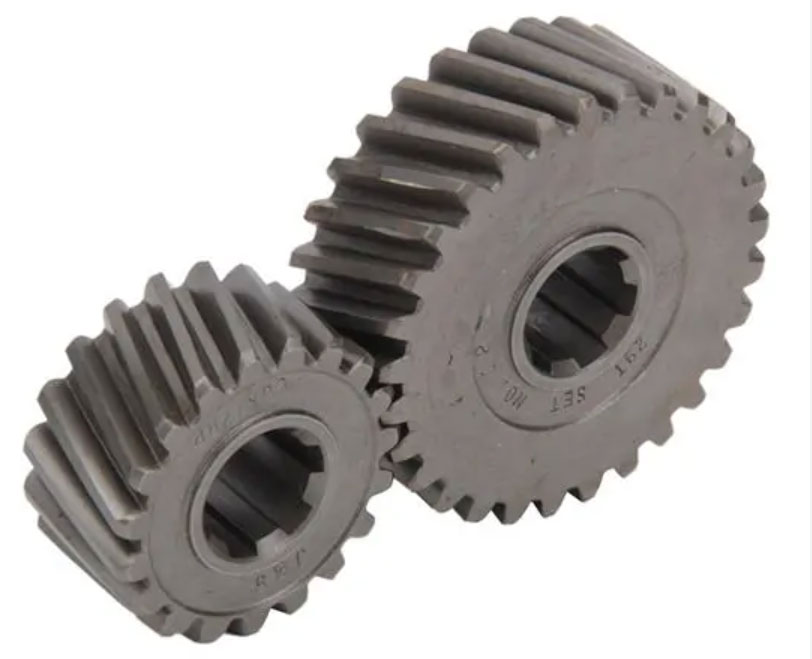
Advantages:
- Smooth and Quiet Operation: The helical tooth design allows gradual tooth engagement, leading to smoother and quieter operation compared to spur gears. The gradual contact between teeth reduces impact and vibration, resulting in less noise during gear meshing.
- High Load-Carrying Capacity: Helical gears have more teeth in contact at any given time than spur gears, distributing the load over a larger area. This increased contact ratio enhances the gear’s load-carrying capacity, making them suitable for transmitting higher loads.
- Efficiency: Due to their improved tooth engagement and reduced sliding friction, helical gears generally have higher efficiency compared to spur gears. This efficiency is particularly beneficial in applications where energy conservation is critical.
- Versatility in Shaft Configurations: Helical gears can be used in parallel shaft configurations (parallel helix gears) or crossed shaft configurations (intersecting helix gears), offering versatility in designing gear systems for various applications.
- Higher Speeds and Torque Transmission: Helical gears can handle higher rotational speeds and transmit higher torques than other gear types, making them suitable for applications requiring high power transmission.
Disadvantages:
- Axial Thrust: The helical angle in helical gears creates an axial thrust force along the gear axis. This axial thrust requires additional support, such as thrust bearings, to absorb and counteract the force, leading to more complex gear designs.
- Axial Space Requirement: The helical design requires more axial space compared to spur gears for a given gear ratio, which may be a limitation in some compact or space-constrained applications.
- Manufacturing Complexity: The production of helical gears involves more intricate machining processes compared to spur gears. Achieving precise helix angles and tooth profiles can be more challenging, increasing manufacturing complexity and costs.
- Potential Side-Thrust: Helical gears may generate radial forces on shafts due to their helix angle. These side-thrust forces may require additional measures to counteract and maintain proper gear alignment.
- Lower Efficiency at Small Ratios: For low gear ratios, helical gears may experience reduced efficiency due to the larger helix angle and increased sliding between teeth.
Overall, helical gears’ advantages, such as smooth operation, high load capacity, and efficiency, make them suitable for various applications. However, considerations must be made for the axial thrust, manufacturing complexity, and potential side-thrust, especially in specific gear systems where these factors may impact the gear’s performance and design.