The manufacturing process of helical gears involves several steps, including material selection, gear cutting, heat treatment, and finishing. Here’s a closer look at each stage of the manufacturing process:
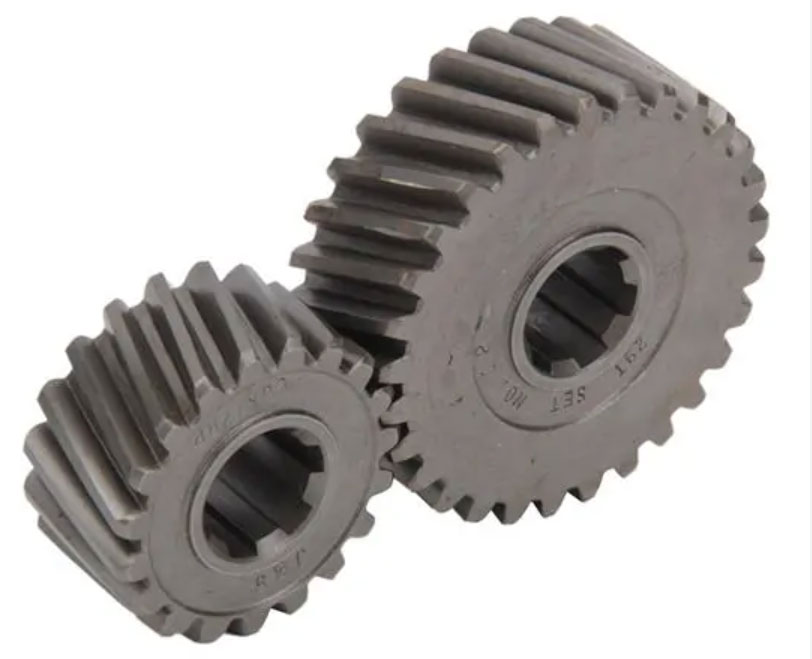
1. Material Selection:
The process begins with selecting the appropriate material for the helical gears. The choice of material depends on the application requirements, load capacity, and operating conditions. Common materials used for helical gears include various grades of carbon steel, alloy steel, stainless steel, and non-ferrous metals.
2. Gear Cutting:
The primary method for cutting helical gears is gear hobbing. Gear hobbing is a precision machining process that uses a specialized tool called a hob to cut the gear teeth into the workpiece. The hob has a helical shape that matches the desired helix angle of the gear. During hobbing, the workpiece rotates, and the hob is gradually fed into the workpiece, generating the helical tooth profile.
3. Heat Treatment:
After gear cutting, the gears undergo heat treatment to improve their mechanical properties and increase their hardness and wear resistance. The heat treatment process typically involves quenching and tempering. Quenching rapidly cools the gears to harden the material, and tempering relieves internal stresses while maintaining some level of toughness.
4. Finishing Operations:
After heat treatment, the gears undergo finishing operations to achieve the required precision and smoothness of the gear teeth. Finishing operations may include grinding, shaving, lapping, or honing. These processes help to achieve precise gear tooth profiles and improve gear meshing and performance.
5. Inspection and Quality Control:
Throughout the manufacturing process, various inspection and quality control measures are implemented to ensure that the gears meet the specified tolerances and quality standards. This may involve dimensional measurements, hardness testing, surface finish inspection, and gear tooth profile verification.
6. Surface Coating (Optional):
In certain applications, helical gears may undergo surface coating to enhance their performance further. Surface coatings, such as nitriding or carburizing, can increase the gear’s wear resistance and reduce friction during operation.
7. Final Assembly:
Once the gears have undergone all necessary manufacturing processes and inspections, they are ready for final assembly. Helical gears are typically paired with other gears, such as spur gears or other helical gears, to form a gear train within the gear system.
It’s important to note that the manufacturing process may vary depending on the specific requirements of the gear, the complexity of the gear design, and the level of precision needed. Skilled operators and advanced machinery are crucial for achieving high-quality helical gears that meet the performance and reliability expectations of various industries and applications.