Herringbone gears and internal gears are both types of gears used in mechanical systems, but they have distinct characteristics and applications.
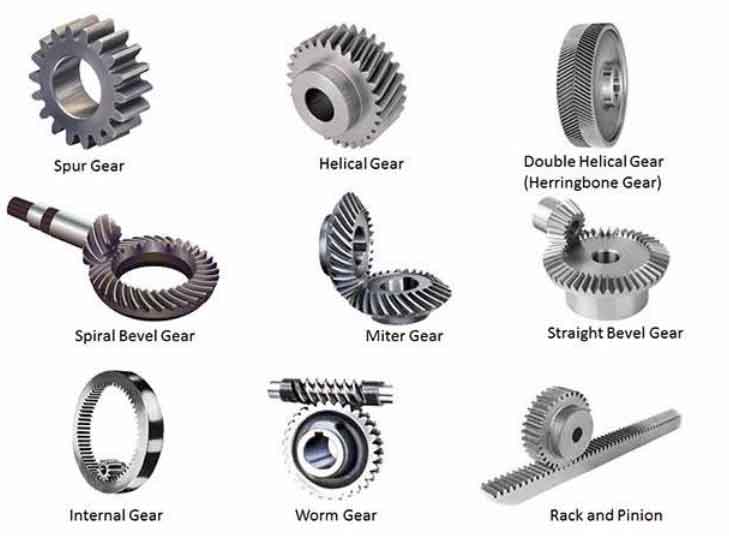
- Herringbone Gears:
- Herringbone gears, also known as double helical gears, have two sets of teeth that are inclined in opposite directions.
- The teeth of herringbone gears are shaped in a “V” or “W” pattern, allowing them to mesh smoothly and reduce axial thrust.
- They offer improved load distribution and higher torque capacity compared to spur gears, as the opposing helix angles cancel out the axial thrust forces.
- Herringbone gears are commonly used in applications requiring high torque transmission and low noise, such as heavy machinery, gearboxes, and turbines.
- The manufacturing process for herringbone gears is more complex compared to other gear types, as it involves cutting teeth in both directions.
- Internal Gears:
- Internal gears have teeth that are cut on the inner surface of a cylindrical ring, and they mesh with external gears that have teeth on the outer surface.
- They are used when space constraints or design requirements call for a gear with a larger diameter and a smaller center gear.
- Internal gears can achieve higher gear ratios in a compact design compared to external gears.
- They are commonly employed in applications like planetary gear systems, where compactness and high gear ratios are critical, such as in automotive transmissions and robotics.
- Manufacturing internal gears can be more challenging than external gears due to the need for specialized cutting tools or processes.
In summary, herringbone gears are advantageous for high torque applications with reduced noise and axial thrust, while internal gears are useful when space-saving and higher gear ratios are necessary. The specific choice between these gear types depends on the requirements and constraints of the mechanical system at hand.