Herringbone gears and miter gears are both types of gears commonly used in mechanical systems. While they serve similar functions, there are some differences in their design and applications. Let’s explore each type in more detail:
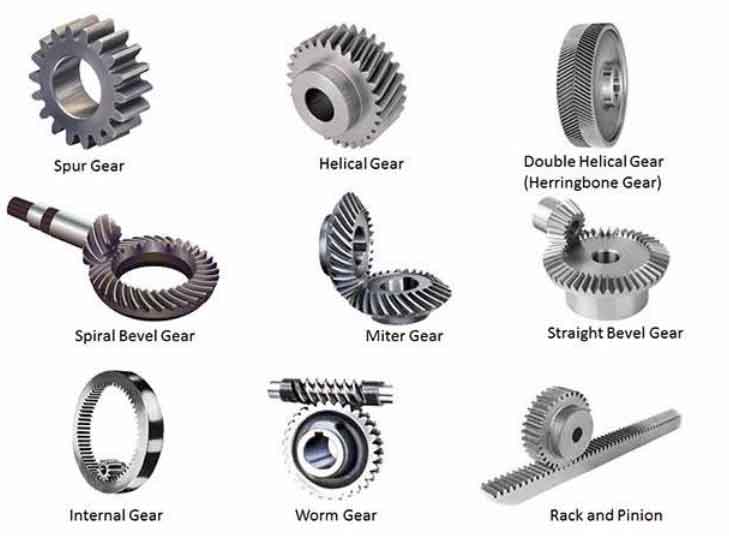
- Herringbone Gears:
- Design: Herringbone gears, also known as double helical gears, have teeth that are cut in a “V” or herringbone pattern. This results in two sets of teeth that are angled in opposite directions, resembling the letter “W.” The angled teeth allow for smoother operation and better load distribution compared to straight-cut gears.
- Advantages:
- Reduced noise and vibration: The opposing helical teeth help to cancel out axial thrust, reducing noise and vibration during operation.
- High load capacity: The angled teeth provide better load distribution, making herringbone gears suitable for high-torque applications.
- Increased tooth contact: The herringbone design increases the tooth contact area, resulting in improved power transmission and reduced wear.
- Applications: Herringbone gears are commonly used in heavy machinery, such as industrial equipment, power transmission systems, and automotive applications.
- Miter Gears:
- Design: Miter gears are a type of bevel gear with straight-cut teeth. They have intersecting shafts positioned at a 90-degree angle to each other. The teeth of the gears are cut at an angle, allowing for power transmission between non-parallel shafts.
- Advantages:
- Transmit motion at right angles: Miter gears are primarily used to transmit rotational motion between shafts that are positioned perpendicular to each other.
- Compact design: The 90-degree orientation of the shafts enables the transfer of motion in tight spaces where other gear configurations might not be suitable.
- No axial thrust: Unlike herringbone gears, miter gears do not generate axial thrust, which can simplify the design of supporting structures.
- Applications: Miter gears are commonly found in various applications, including power tools, printing machinery, hand drills, and other devices that require motion transfer at right angles.
Herringbone gears and miter gears have different tooth designs and applications. Herringbone gears are suitable for high-torque, heavy-load applications due to their improved load distribution and reduced noise. Miter gears, on the other hand, are used to transmit motion at right angles between intersecting shafts and are often employed in compact and space-constrained systems.