Abstract:
This paper presents a novel high-order contact analysis method for spiral bevel gears, addressing the limitations of conventional second-order contact analysis and the complexity of implementing high-order contact theories. By integrating the ease-off topological surface equation with the tooth surface equation of spiral bevel gears and leveraging the analytical relationship between transmission error, contact trace, and ease-off, we introduce discrete tooth surface high-order contact analysis with parameters such as higher-order derivatives of transmission ratio and short-range curvature of contact trace. A simplified calculation approach based on the finite difference method is established. The results demonstrate that the proposed method effectively captures the global characteristics of the tooth surface morphology and the complexity of the contact process along the contact trace. The findings not only validate the correctness and effectiveness of the proposed analysis method but also reduce the computational complexity of high-order contact parameters, offering possibilities for global tooth surface design optimization.
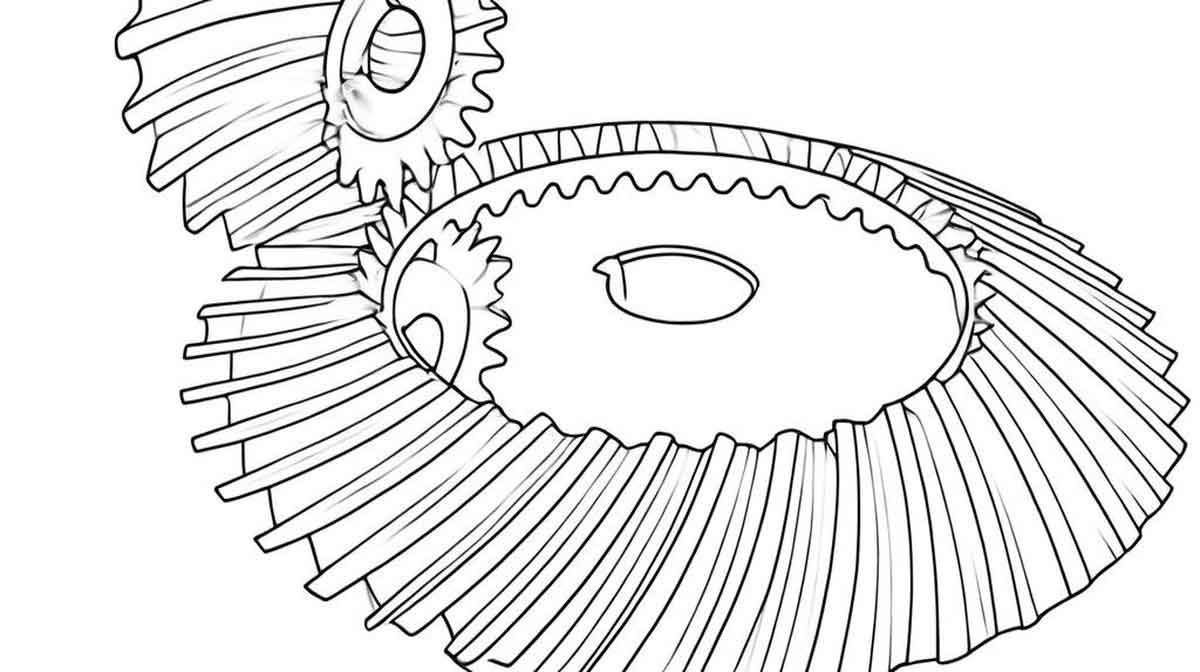
1. Introduction
Spiral bevel gears are widely used in power transmission systems due to their compact structure, high load-carrying capacity, and smooth transmission. The contact behavior between the mating tooth surfaces significantly impacts the overall performance of the gear system, including noise, vibration, and wear. To ensure optimal performance, accurate analysis of the contact behavior is essential. However, current design methodologies primarily rely on second-order contact analysis, which often fails to capture the intricacies of high-order contact phenomena.
1.1 Motivation and Objectives
Traditional second-order contact analysis methods, such as those based on local conjugacy or local synthesis principles, are insufficient for capturing the complex contact behavior of spiral bevel gears. This limitation motivates the need for a more sophisticated high-order contact analysis framework. The objectives of this research are twofold:
- Develop a high-order contact analysis method for spiral bevel gears based on the ease-off concept and differential geometry.
- Implement a simplified computational approach using the finite difference method to facilitate efficient analysis.
1.2 Literature Review
Several research efforts have focused on improving the contact analysis and design of spiral bevel gears. Gleason’s “local conjugacy method” calculates first- and second-order contact parameters at a reference point on the large gear tooth surface . Litvin proposed a “local synthesis method” that presets second-order contact parameters to design tooth surfaces . Other researchers have explored compensation methods for machining errors, ease-off-based active modification designs, and error correction strategies to reduce noise.
Despite these advancements, high-order contact analysis remains challenging due to its computational complexity and the lack of a comprehensive theoretical framework. Early attempts at third-order contact analysis, while theoretically insightful, did not fully consider all high-order contact parameters and were difficult to implement in practice.
2. Theoretical Background
2.1 Ease-Off Concept
Ease-off refers to the normal relative modification amount between mating tooth surfaces. It provides a versatile tool for shaping and optimizing tooth surfaces to achieve desired contact patterns and transmission characteristics.
2.2 Differential Geometry of Surfaces
Differential geometry offers a mathematical framework for analyzing the local and global properties of surfaces. Key concepts such as principal curvatures, Gaussian curvature, and short-range curvature are essential for characterizing surface geometry and contact behavior.
3. Proposed High-Order Contact Analysis Method
3.1 Discrete Tooth Surface Representation
We represent the spiral bevel gear tooth surfaces as discrete meshes, allowing for efficient numerical computations. The tooth surface equations are derived from the meshing geometry and machining parameters.
3.2 Ease-Off-Based Topological Surface Transformation
We transform the discrete tooth surfaces using the ease-off concept to create modified tooth surfaces with desired contact characteristics. The ease-off transformation is applied along predefined grid lines on the tooth surfaces.
3.3 High-Order Contact Parameters
The proposed high-order contact analysis focuses on two key parameters:
- Higher-Order Derivatives of Transmission Ratio: These parameters quantify the variation in the transmission ratio over small angular intervals, reflecting the magnitude of short-term transmission errors.
- Short-Range Curvature of Contact Trace: This parameter measures the local bending of the contact trace, indicating the complexity of the contact process.
3.4 Computational Approach Using Finite Difference Method
We adopt the finite difference method to numerically compute the high-order contact parameters. By discretizing the tooth surfaces into a grid and applying numerical differentiation, we obtain the higher-order derivatives of transmission ratio and short-range curvature along the contact trace.
4. Methodology and Implementation
4.1 Discrete Tooth Surface Construction
The tooth surface equations are derived from the meshing geometry and machining parameters of the spiral bevel gear pair. The tooth surfaces are discretized into a fine grid for numerical analysis.
4.2 Ease-Off Surface Modification
The ease-off transformation is applied to the discrete tooth surfaces along predefined grid lines. The modification amounts are determined based on the desired contact characteristics and optimized using design parameters.
4.3 High-Order Contact Parameter Computation
The higher-order derivatives of transmission ratio and short-range curvature are computed using the finite difference method. The transmission error is first calculated based on the modified tooth surfaces, followed by numerical differentiation to obtain the required high-order contact parameters.
5. Results and Discussion
5.1 Validation of the Proposed Method
The proposed high-order contact analysis method is validated using a test case involving a spiral bevel gear pair from a helicopter transmission system. The initial tooth surfaces are analyzed, and the computed high-order contact parameters are compared with theoretical expectations.
5.2 Analysis of Modified Tooth Surfaces
Three sets of ease-off modification parameters are applied to the initial tooth surfaces, resulting in modified tooth surfaces with desired contact characteristics. The high-order contact parameters of the modified tooth surfaces are computed and compared with those of the initial tooth surfaces.
5.3 Comparative Analysis
The computed high-order contact parameters for the initial and modified tooth surfaces are presented in tables and graphs for comparison. Key findings include:
- The higher-order derivatives of transmission ratio for the modified tooth surfaces exhibit reduced fluctuations compared to the initial tooth surfaces, indicating improved transmission smoothness.
- The short-range curvature of the contact trace varies significantly along the contact path, highlighting the complexity of the contact process.
- The proposed method effectively captures the global characteristics of the tooth surfaces and their impact on the contact behavior.
6. Conclusion
This paper presents a novel high-order contact analysis method for spiral bevel gears based on the ease-off concept and differential geometry. By combining the ease-off topological surface equation with the tooth surface equation and leveraging the analytical relationship between transmission error, contact trace, and ease-off, we develop a discrete tooth surface high-order contact analysis framework. A simplified computational approach using the finite difference method is implemented to facilitate efficient analysis.
The results demonstrate that the proposed method accurately captures the global characteristics of the tooth surfaces and the complexity of the contact process along the contact trace. The computed high-order contact parameters, including higher-order derivatives of transmission ratio and short-range curvature of contact trace, provide valuable insights into the contact behavior of spiral bevel gears. The findings validate the correctness and effectiveness of the proposed method and offer possibilities for global tooth surface design optimization.