This article delves into the design, modeling, and analysis of high – order non – circular helical gears. It aims to address the issues related to traditional non – circular helical gear design and introduce an improved approach. By using a combination of the conversion method of tooth profile and a new “helix line” (the intersection curve of the involute helicoid and the pitch curve cylinder), a more accurate gear model is established. Through detailed parameter calculation, modeling steps, and motion analysis, the feasibility and effectiveness of the new design are verified. This research provides valuable references for the further study and application of non – circular helical gears.
1. Introduction
Non – circular gears have found wide applications in various fields such as machinery, robotics, and aerospace due to their ability to provide variable – ratio transmission. Among them, non – circular helical gears combine the advantages of non – circular gears and helical gears, such as smooth transmission, large 重合度,and high load – carrying capacity.
The design methods of non – circular gears mainly include the analytical method, the conversion method of tooth profile, and the envelope method. The analytical method calculates the tooth profile equation by solving the meshing angle function, but it has a large amount of calculation and is related to the sampling point interval and quantity of the tooth profile. The conversion method of tooth profile approximates the pitch curve at each tooth position as the pitch circle of a standard spur gear, which has a relatively simple calculation and strong generality. The envelope method simulates the gear – hobbing process to generate the tooth profile, which is more suitable for high – precision manufacturing requirements but is complex in the generation process.
For non – circular helical gears, the traditional design methods also face some problems. For example, when using the conversion method of tooth profile, the helix line projected onto the plane of the pitch curve does not completely coincide with the pitch curve due to the curvature change of the non – circular gear pitch curve, resulting in uneven tooth deviation. This article proposes a new design method to solve this problem.
2. Basic Theory of Non – Circular Gears
2.1 Pitch Curve – Related Parameter Design of Non – Circular Gears
The pitch curves of the driving and driven non – circular gears play a crucial role in determining the gear’s motion characteristics. Let \(O_{1}\) and \(O_{2}\) be the rotation centers of the driving and driven wheels respectively, and \(O_{1}\) and \(O_{2}’\) be their geometric centers. The pitch curves of the two gears are always tangent. When the driving wheel rotates counter – clockwise by an angle \(\theta_{1}\), the driven wheel rotates clockwise by an angle \(\theta_{2}\).
The polar coordinate expressions of the pitch curves of the driving and driven wheels are shown in Table 1:
Gear | Polar Coordinate Expression | Parameter Explanation |
---|---|---|
Driving Wheel | \(\left\{\begin{array}{l} \rho_{1}\left(\theta_{1}\right)=\frac{p_{1}}{1 – k_{1}\cos n_{1}\theta_{1}} \\ p_{1}=A_{1}\left(1 – k_{1}^{2}\right) \end{array}\right.\) | \(n_{1}\), \(n_{2}\): Orders of the driving and driven wheels; \(n = n_{2}/n_{1}\); \(k_{1}\), \(k_{2}\): Eccentricities of the driving and driven wheels; \(A_{1}\), \(A_{2}\): Long semi – axis lengths of the driving and driven wheels |
Driven Wheel | \(\left\{\begin{array}{l} \rho_{2}\left(\theta_{2}\right)=\frac{p_{2}}{1 + k_{2}\cos n_{2}\theta_{2}} \\ p_{2}=\frac{n^{2}p_{1}}{\sqrt{n^{2}-k_{1}^{2}\left(n^{2}-1\right)}} \\ k_{2}=\frac{k_{1}}{\sqrt{n^{2}-k_{1}^{2}\left(n^{2}-1\right)}} \end{array}\right.\) |
When the basic parameters of the driving wheel are determined, the relevant basic parameters of the driven wheel can be calculated through the following relationships:
Parameter | Relationship |
---|---|
Center Distance a | \(a = A_{1}\left[1+\sqrt{n^{2}-k_{1}^{2}\left(n^{2}-1\right)}\right]\) |
Gear Tooth Number – Related | \(\left\{\begin{array}{l} A_{i}=\frac{\pi m z_{i}}{n_{i}M_{i}I_{i}} \\ I_{i}=4\int_{0}^{\frac{\pi}{2}}\sqrt{1 – K_{i}^{2}\sin^{2}\varphi}d\varphi \end{array}, i = 1,2\) \(\theta_{2}=2\arctan\left(\sqrt{\frac{a – p_{1}+a k_{1}}{a – p_{1}-a k_{1}}}\tan\frac{n_{1}\theta_{1}}{2}\right)/n_{2}\) |
2.2 Related Checks of Non – Circular Gears
Non – circular gears need to be checked in terms of pressure angle, undercutting, and convex – concavity to ensure their normal operation. The check formulas are shown in Table 2:
Check Item | Check Formula | Requirements |
---|---|---|
Pressure Angle Check | \(\left\{\begin{array}{l} i_{12}=\frac{k_{1}\left(k_{1}-\cos n_{1}\theta_{1}\right)+\left(1 – k_{1}\cos n_{1}\theta_{1}\right)\sqrt{n^{2}-\left(n^{2}-1\right)k_{1}^{2}}}{1 – k_{1}^{2}} \\ \gamma_{1}=\arctan\left(-\frac{i_{12}+1}{i_{12}’}\right) \\ \alpha_{12L}=-\gamma_{1}+\alpha+\frac{\pi}{2} \end{array}\right.\) | \(\alpha_{12L}\leq65^{\circ}\) |
Undercutting Check | \(\left\{\begin{array}{l} r_{min}=r(\theta)_{min}=\min\left\{\frac{\left[\rho^{2}(\theta)+\left(\frac{d\rho}{d\theta}\right)^{2}\right]^{3/2}}{\rho^{2}(\theta)+2\left(\frac{d\rho}{d\theta}\right)^{2}-\frac{d^{2}\rho}{d\theta^{2}}}\right\} \\ h_{d}^{*}m\leq r_{min}\sin^{2}\alpha \end{array}\right.\) | – |
Convex – Concavity Check | \(k_{i}\leq\frac{1}{n_{i}^{2}-1}, n_{i}>1, i = 1,2\) | When \(n_{i}=1\), the gear is a first – order elliptical gear and has no inward concavity |
2.3 Helix Line Improvement of Non – Circular Helical Gears
2.3.1 Defects of the Helix Line of Non – Circular Helical Gears
In cylindrical helical gears, the helix line obtained by intersecting the tooth profile surface and the pitch cylinder coincides with the pitch circle when projected onto the plane of the pitch circle. However, for non – circular helical gears designed by the conversion method of tooth profile, due to the different curvatures of the pitch curve at each tooth position, the helix lines at different positions have different deviations. As shown in Figure 1, when the helix lines are projected onto the plane of the pitch curve, at the position \(a_{1}\) where the curvature of the pitch curve \(\rho\) is small, the helix line \(L_{1}\) is inward – biased, and at the position \(a_{2}\) where the curvature is large, the helix line \(L_{2}\) is outward – biased. This uneven tooth deviation has a great impact on the meshing performance of non – circular helical gears, so it is necessary to improve the helix line.
2.3.2 Characteristics of the Involute Helical Surface
The involute helical surface is formed when a generating surface rolls purely along a base cylinder. In a relative coordinate system \(\sigma_{1}x_{1}y_{1}z_{1}\), when a generating surface KMN rolls purely along a base cylinder \(R_{b}\) with a radius \(r_{b}\), a straight line KM on the generating surface that makes an angle \(\beta_{b}\) (the base cylinder helix angle) with the busbar JKN of the base cylinder generates an involute helical surface ABCDE. The intersection of the straight line KM and the busbar JKN is point K, and the path ABC formed by point K is the base cylinder helix line. The straight line KM is always tangent to the base cylinder helix line ABC.
When an arbitrary spatial plane \(z_{1}=C\) (C is an arbitrary constant) intersects the involute helical surface, the intersection line is an involute. For a cylindrical helical gear, when \(C = 0\), the intercepted involute AE is the involute of the end face of the helical gear, and when \(C = B\) (B is the tooth width), the intercepted involute is the involute of the other end face of the helical gear. The space curve AC obtained by intersecting the cylinder formed by the base cylinder corresponding to the pitch circle r and the involute helical surface ABCDE is the helix line of the helical gear. The parameter equation of the involute helical surface in the relative coordinate system \(\sigma_{1}x_{1}y_{1}z_{1}\) is.
2.3.3 Solution of the Helix Line of Non – Circular Helical Gears
To overcome the problem of uneven helix line deviation of non – circular helical gears, a pitch curve cylinder is determined to intersect with the involute helical surface ABCDE. The obtained intersection curve \(A^{*}C^{*}\) (referred to as the intersection curve) is no longer a helix line. When the intersection curve \(A^{*}C^{*}\) is projected onto the plane of the pitch curve, it coincides with the pitch curve, solving the problem of uneven helix line deviation. The solution steps of the intersection curve are as follows:
Step | Operation |
---|---|
Step 1 | Fix the absolute coordinate system \(\sigma xyz\) at the rotation center o of the non – circular helical gear, and expand the relative coordinate system \(\sigma_{1}x_{1}y_{1}z_{1}\) to \(\sigma_{j}x_{j}y_{j}z_{j}\) (j represents the tooth number, that is, the j – th tooth) and fix it at the curvature center c of the tooth on the end face of the non – circular helical gear. |
Step 2 | Obtain the vector representation of the curvature center of the j – th tooth in the coordinate system \(\sigma xyz\). Given the polar coordinates \((\theta_{j},\rho_{j}(\theta_{j}),0)\) of the j – th tooth on the pitch curve, the coordinates \(c_{j}=(\sigma\sigma_{j})\) of the curvature center \(c_{j}\) in the absolute coordinate system \(\sigma xyz\) are \(\left(\begin{array}{c}x_{j}\left(\theta_{j}\right) \\ y_{j}\left(\theta_{j}\right) \\ 0\end{array}\right)=\left(\begin{array}{c}\rho_{j}\left(\theta_{j}\right)\cos\theta_{j}-r_{j}\left(\theta_{j}\right)\cos n_{j}\left(\theta_{j}\right) \\ \rho_{j}\left(\theta_{j}\right)\sin\theta_{j}-r_{j}\left(\theta_{j}\right)\sin n_{j}\left(\theta_{j}\right) \\ 0\end{array}\right)\), and \(n_{j}\left(\theta_{j}\right)=\left.\arctan\left(-\frac{\rho'(\theta)\cos\theta-\rho(\theta)\sin\theta}{\rho'(\theta)\sin\theta+\rho(\theta)\cos\theta}\right)\right|_{\theta=\theta_{j}}\). Then, obtain the curvature – center coordinate set matrix \(C_{3\times2}=(c_{1}\cdots c_{j}\cdots c_{z})\). |
Step 3 | According to the parameter equation of the involute helical surface, find its vector – form equation. The vector – form equation of the involute helical surface \((ABCDE)_{j}\) at the j – th tooth is \(p_{j}=\sigma_{j}P=(x_{j}(\varphi_{j}),y_{j}(\varphi_{j}),z_{j}(\varphi_{j}))^{T}\), and its parameter – form equation is \(\left\{\begin{array}{l} x_{j}\left(\varphi_{j},u_{j}\right)=r_{hj}\cos\varphi_{j}+u_{j}\cos\beta_{b}\sin\varphi_{j} \\ y_{j}\left(\varphi_{j},u_{j}\right)=r_{bj}\sin\varphi_{j}-u_{j}\cos\beta_{b}\cos\varphi_{j} \\ z_{j}\left(\varphi_{j},u_{j}\right)=p_{j}\varphi_{j}-u_{j}\sin\beta_{b} \end{array}\right.\), where \(p_{j}=r_{b_{j}}\tan\beta_{1}\), \(r_{bj}\) is the base – circle radius corresponding to the j – th tooth. Then, obtain the vector – set matrix \(P_{3\times z}=(p_{1}\cdots p_{j}\cdots p_{z})\) of other teeth’s involute helical surfaces. |
Step 4 | Represent the involute helical surface \((ABCDE)_{j}\) of the j – th tooth in the absolute coordinate system \(\sigma xyz\) and write the pitch – curve cylinder equation. The involute helical surface \((ABCDE)_{j}\) in the absolute coordinate system \(\sigma xyz\) is \(o_{j}=\sigma P=c_{j}+p_{j}\), and its function form is \(F_{j}(x_{j}(\theta_{j},\varphi_{j},u_{j}),y_{j}(\theta_{j},\varphi_{j},u_{j}),z_{j}(\varphi_{j},u_{j})) = 0\). The vector – set matrix \(O_{3\times z}=(o_{1}\cdots o_{j}\cdots o_{z})\) of all involute helical surfaces is \(O_{3\times z}=C_{3\times z}+P_{3\times z}\). The rectangular – coordinate cylinder equation of the plane pitch curve \(\rho(\theta)\) is \(\left\{\begin{array}{l} x(\theta)=\rho(\theta)\cos(\theta) \\ y(\theta)=\rho(\theta)\sin(\theta) \\ z(\theta)=C(\text{constant}) \end{array}\right.\), and its function form is \(F(x(\theta),y(\theta),z(\theta)) = 0\). |
Step 5 | Calculate the intersection curve \(A_{j}^{*}C_{j}^{*}\) at the j – th tooth. Combine the pitch – curve cylinder equation and the involute helical surface equation of the j – th tooth to obtain the general equation \(G_{j}(\theta_{j},\varphi_{j},u_{j},\theta,\rho(\theta))\) of the intersection curve. Then, integrate all the intersection – curve equations to get the vector – set \(G=(G_{1}\cdots G_{j}\cdots G_{z})\). Although the intersection – curve equation is complex, it can be obtained by the intersection operation of the pitch – curve cylinder and the involute helical surface in subsequent modeling. |
3. Modeling Process of High – Order Non – Circular Helical Gears
3.1 Basic Parameter Setting of Non – Circular Helical Gears
The main parameters of the driving non – circular helical gear are given in Table 3:
Name | Symbol | Value |
---|---|---|
Normal Module | \(m_{n}\) | 3mm (Given) |
Driving Wheel Tooth Number | \(z_{1}\) | 21 (Given) |
Tooth Width | B | 50mm (Given) |
Helix Angle | \(\beta\) | \(15^{\circ}\) Right – Hand (Given) |
Normal Tooth Profile Angle | \(\alpha_{n}\) | \(20^{\circ}\) (Given) |
Normal Addendum Coefficient | \(h_{an}^{*}\) | 1 (Given) |
Normal Clearance Coefficient | \(c_{n}^{*}\) | 0.25 (Given) |
Driving Wheel Eccentricity | ( |
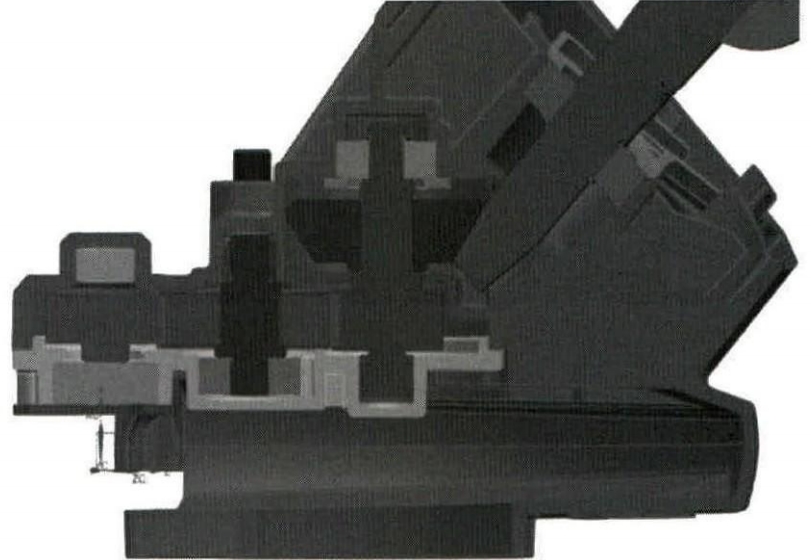