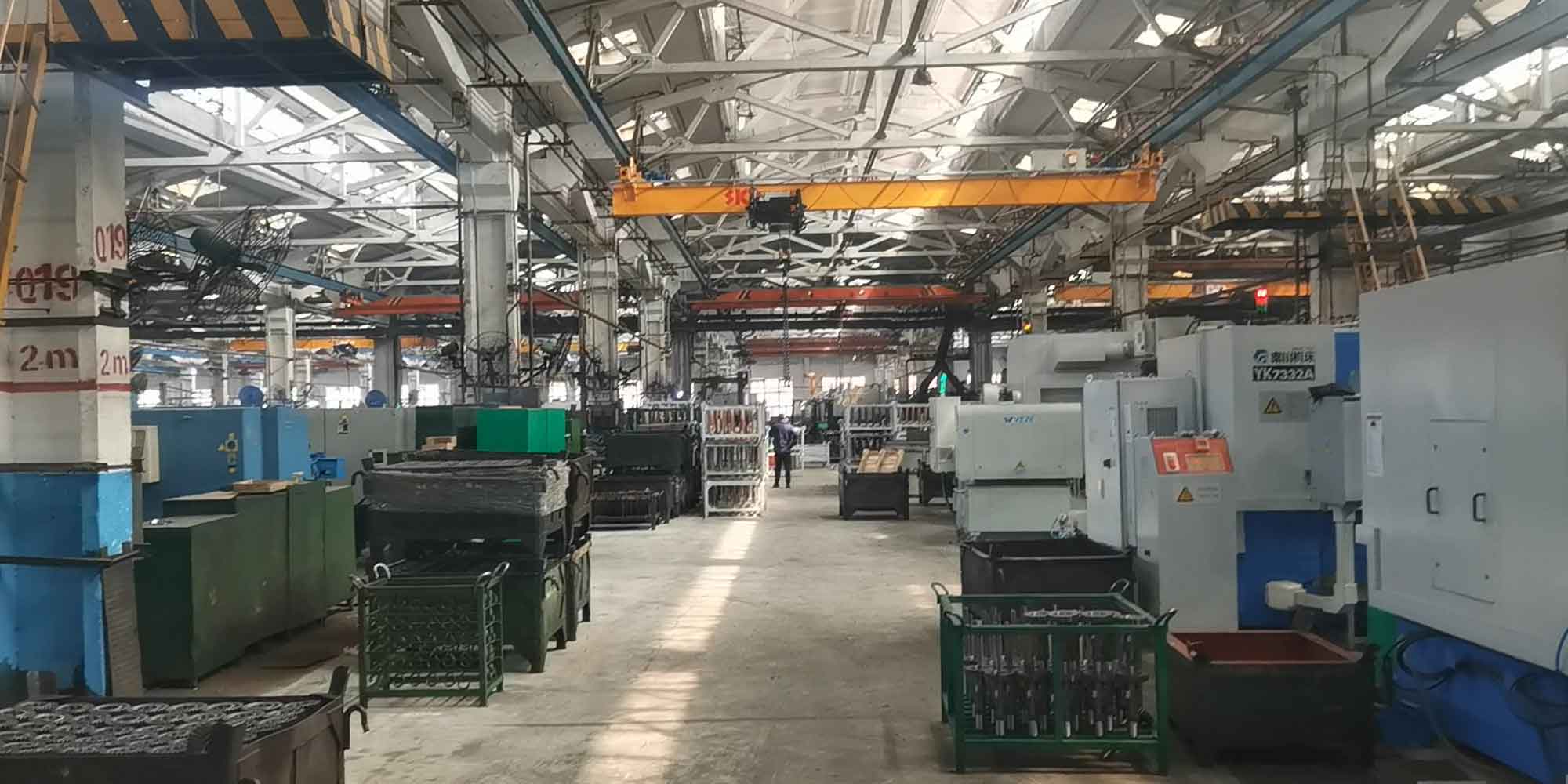
Gear manufacturer play a crucial role in enhancing the efficiency of wind turbines. Here are several key aspects where their contribution is significant:
- Precision Engineering: The manufacturing of gears requires high precision to ensure that they fit perfectly and operate smoothly within the wind turbine. Any imperfection in the gear can lead to energy losses due to friction or misalignment. Precision engineering helps in minimizing these losses, thereby improving the efficiency of the turbine.
- Material Selection: The choice of materials used in gear manufacturing impacts the durability and performance of wind turbines. Advanced materials that can withstand higher stresses and have lower wear rates are crucial for long-term performance and reliability. Using stronger, lighter materials can also reduce the weight of the turbine, which can enhance its efficiency.
- Innovative Designs: Gear manufacturer is continually innovating to create more efficient gear designs. For example, helical or planetary gears are often used in place of traditional spur gears to increase load capacity and reduce noise, which can indirectly improve the efficiency and environmental compatibility of wind turbines.
- Thermal Management: Managing the heat produced by gear friction is vital for maintaining efficiency. Gear manufacturer can implement design features that improve heat dissipation, such as using heat-tolerant materials or integrating cooling channels within the gear system.
- Lubrication Systems: Effective lubrication reduces friction and wear in gear systems, which is essential for the smooth operation of wind turbines. Advances in lubrication technologies, such as the use of synthetic oils or lubricants with nanoparticles, can significantly enhance the efficiency and lifespan of gears.
- Maintenance and Monitoring: Gear manufacturer can also contribute by designing gears that are easier to maintain and monitor for wear and tear. This can reduce downtime and maintenance costs, ensuring continuous and efficient operation of wind turbines.
- Customization: Customizing gear systems to the specific needs of a wind turbine based on its location, expected wind speeds, and other environmental factors can optimize its performance and efficiency.
- Noise Reduction: Noise is a significant concern for wind turbines, especially in populated areas. Gear manufacturer can play a crucial role by designing gears that operate more quietly. This involves refining gear tooth design, using materials that dampen sound, and implementing precision assembly techniques to reduce vibrations. Lower noise levels can lead to fewer restrictions on turbine placement and potentially larger installations, thereby increasing overall energy production efficiency.
- Integration with Advanced Control Systems: Modern wind turbines use sophisticated control systems to optimize their operation based on real-time wind conditions. Gears that are designed to be compatible with these control systems can better handle variable loads and speeds. This adaptability can prevent excessive wear and tear while maintaining optimal efficiency under diverse operating conditions.
- Scalability of Design: As wind turbine technology progresses, the demand for larger turbines capable of generating more power increases. Gear manufacturer must ensure that their designs are scalable to accommodate these larger sizes without compromising efficiency. This involves strengthening gear materials and designs to handle higher stresses and loads without a significant increase in weight or cost.
- Sustainability Practices: Sustainability in gear manufacturing not only refers to the production of gears themselves but also to the lifecycle of the product. Gear manufacturer can enhance turbine efficiency by using recyclable materials, reducing waste during production, and ensuring that the gears can be easily dismantled and recycled at the end of their service life. Sustainable practices help reduce the overall environmental impact of wind turbines.
- Collaboration with Turbine Manufacturer: Close collaboration between gear manufacturer and turbine manufacturer can lead to better integrated and optimized systems. This partnership allows for real-time feedback and continuous improvement in gear design and performance, directly impacting the efficiency of wind turbines.
By addressing these areas, gear manufacturer contribute significantly to the advancement and optimization of wind turbine technology. Their efforts in design, materials science, and gear manufacturing techniques play a pivotal role in making wind energy a more viable and efficient alternative to traditional power generation methods.