Choosing the right ball mill gear for your mining operation involves several critical considerations. The correct selection can improve efficiency, reduce downtime, and extend the lifespan of your equipment. Here are key factors to consider when selecting a ball mill gear for your mining operation:
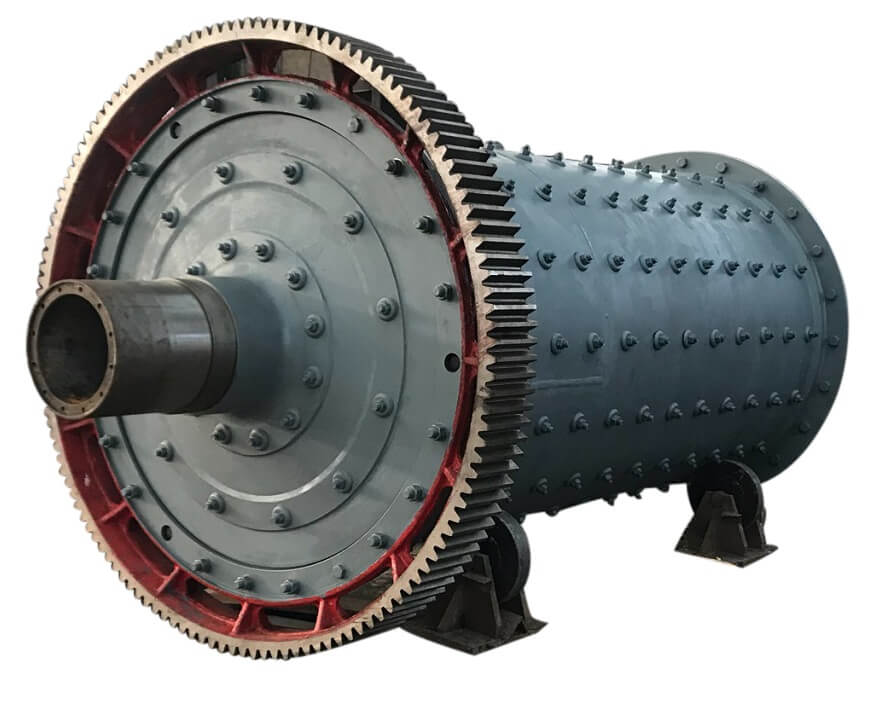
1. Type of Ball Mill Gear
- Spur Gears: Simplest type of gear with straight teeth. Best suited for low-speed applications due to high noise levels at higher speeds.
- Helical Gears: Have angled teeth, resulting in smoother and quieter operation. Suitable for high-speed applications.
- Ring Gears: A type of gear that encircles the mill. Used in larger ball mills and essential for heavy-duty operations.
2. Material Quality
- Cast Steel: Offers good durability and shock resistance. Suitable for various mining operations but can be heavy.
- Forged Steel: Provides superior strength and durability. Ideal for heavy-duty applications where the gear is subject to high loads.
- Alloy Steels: High-performance materials that offer excellent wear resistance and strength. Suitable for extreme conditions.
3. Manufacturing Process
- Machining Accuracy: Precision in manufacturing ensures that the gear meshes correctly with its counterpart, reducing wear and extending service life.
- Heat Treatment: Processes like case hardening or induction hardening increase the surface hardness of the gear teeth, improving wear resistance.
4. Gear Size and Power Capacity
- Power Transmission Requirements: Consider the maximum power transmission requirements of your ball mill. The gear must be capable of transmitting the necessary power without failure.
- Size and Weight: Larger gears can transmit more power but may require more space and stronger support structures.
5. Operational Conditions
- Load Conditions: Evaluate the typical and peak load conditions the gear will face. Opt for gears designed to handle the expected load with an adequate safety margin.
- Environmental Conditions: Consider the environmental conditions, such as temperature, humidity, and exposure to dust or chemicals. Certain materials and treatments offer better resistance to these conditions.
6. Maintenance and Lifespan
- Ease of Maintenance: Choose a gear design that allows for easy inspection and maintenance to minimize downtime.
- Expected Lifespan: Consider the expected lifespan of the gear and compare it against its cost. Longer-lasting gears may offer better value over time.
7. Supplier Reputation and Support
- Reliable Supplier: Choose a supplier with a good reputation for quality and service. Ensure they have a proven track record in the mining industry.
- After-Sales Support: Look for suppliers that offer excellent after-sales support, including spare parts availability, technical assistance, and warranty services.
8. Cost Consideration
- Initial Cost vs. Operational Cost: While the initial cost is an important factor, also consider the operational costs, including maintenance and energy consumption. A more expensive gear that offers lower operational costs can be more economical in the long run.
Conclusion
Selecting the right ball mill gear involves a balance between initial cost, operational efficiency, maintenance needs, and long-term durability. It’s essential to conduct a thorough analysis of your operation’s specific requirements, consider the total cost of ownership, and select a gear that meets your operational needs while providing the best value over its lifecycle. Consulting with engineering experts and gear manufacturers can provide valuable insights and help make an informed decision.