The evolution of ball mill gear manufacturing techniques over the years reflects advancements in engineering, materials science, and technology. These improvements have led to more efficient, durable, and reliable gear systems for ball mills, which are crucial for grinding materials in various industries, including mining, cement, and power generation. Let’s explore the key developments in this area:
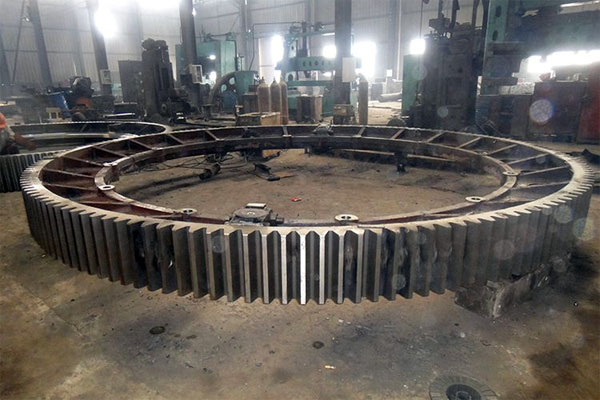
Early Stages: Manual Processes and Cast Iron Gears
- Manual Craftsmanship: Initially, ball mill gears were made through manual processes. Skilled workers would hand-craft each gear, ensuring proper fit and functionality. This process was labor-intensive and time-consuming.
- Material Use: Early gears were often made from cast iron. Cast iron offered the necessary durability and wear resistance for the gears’ operational demands but had limitations in terms of strength and longevity.
Industrial Revolution: Standardization and Steel
- Introduction of Steel: With the Industrial Revolution, steel became the preferred material for manufacturing ball mill gears. Steel offered superior strength and durability compared to cast iron, allowing for the development of larger and more reliable gears.
- Standardization of Parts: The era also saw the beginning of parts standardization, which significantly improved the efficiency of gear production and maintenance. Standardization allowed for the interchangeability of parts, reducing downtime and maintenance costs.
Mid-20th Century: Machining and Heat Treatment Improvements
- Advanced Machining Techniques: The development of advanced machining techniques, such as precision cutting and grinding, enabled the production of gears with tighter tolerances and smoother surface finishes. This resulted in more efficient and quieter operation.
- Heat Treatment Processes: Innovations in heat treatment processes, like case hardening and induction hardening, improved the wear resistance and lifespan of ball mill gears. These processes enhanced the hardness of the gear surfaces while maintaining the core’s toughness.
Late 20th Century: Computer-Aided Design and Manufacturing
- CAD and CAM: The advent of computer-aided design (CAD) and computer-aided manufacturing (CAM) technologies revolutionized gear manufacturing. These tools allowed for more complex and precise designs, reduced production times, and facilitated the manufacturing of gears with intricate shapes and features.
- Quality Control: Advanced inspection and quality control techniques, including computerized tomography (CT) scans and 3D scanning, were introduced. These technologies ensured higher precision and reliability of the final products.
21st Century: Additive Manufacturing and Smart Manufacturing
- Additive Manufacturing: The latest developments in gear manufacturing include additive manufacturing (3D printing), which allows for the creation of gears with complex geometries that would be difficult or impossible to produce with traditional methods. This technique also reduces material waste and can accelerate the prototype phase.
- Smart Manufacturing: Integration of IoT (Internet of Things) devices and AI (Artificial Intelligence) in the manufacturing process leads to what is often called smart manufacturing. This enables predictive maintenance, real-time monitoring, and optimization of production processes, further enhancing efficiency and reducing costs.
Future Directions
Looking forward, the evolution of ball mill gear manufacturing will likely continue to focus on improving efficiency, reducing environmental impact, and integrating new materials and technologies. Innovations in materials science, such as the development of high-performance alloys and composites, could offer further improvements in gear performance and longevity. Additionally, the ongoing advancement of digital and smart manufacturing technologies will continue to transform production processes, making them more flexible, efficient, and sustainable.