Hypoid gears are commonly used in heavy-duty applications where high torque and loads are encountered. Their unique tooth geometry and design characteristics make them well-suited for such demanding operating conditions. Here are some key aspects to consider when using hypoid gears in heavy-duty applications:
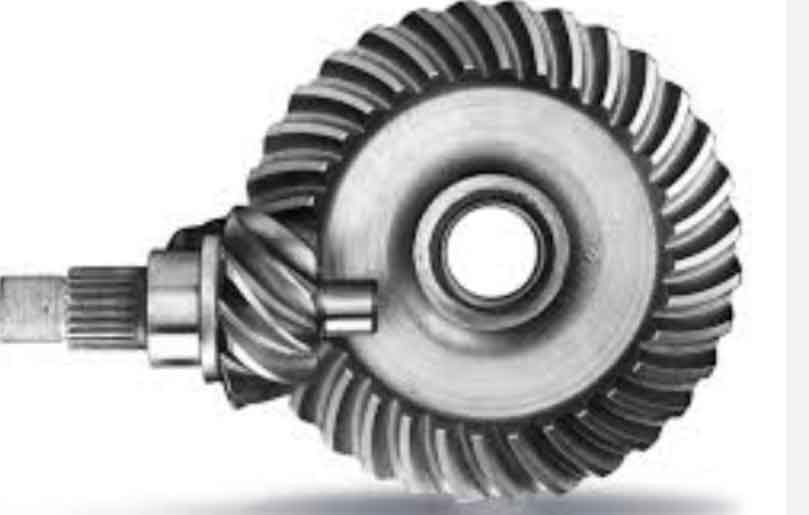
- Material Selection: The choice of materials for hypoid gears is critical to handle high torque and loads. High-strength steel alloys, such as alloy steel or carburizing steel, are commonly used due to their excellent strength, fatigue resistance, and load-carrying capacity. The material selection should consider factors like gear size, operating conditions, and desired gear life.
- Gear Geometry: The geometry of hypoid gears can be optimized to handle high torque and loads. Parameters such as gear ratio, tooth profile, and tooth thickness should be carefully designed to distribute the load evenly across the gear teeth. This ensures that no individual teeth or sections of the gear are subjected to excessive stress.
- Gear Size and Tooth Dimensions: The size of the hypoid gears should be appropriately determined to handle the required torque and loads. Larger gear sizes allow for greater surface contact area and increased load-carrying capacity. Additionally, the tooth dimensions, such as tooth width and thickness, should be designed to accommodate the expected torque and loads without exceeding the material’s limits.
- Bearing Selection and Support: Hypoid gears in heavy-duty applications require robust bearing systems to handle the applied loads. Careful selection of high-capacity bearings with adequate load ratings is essential. The bearings should be properly supported within the gear assembly to ensure even load distribution and minimize misalignment.
- Lubrication and Cooling: Adequate lubrication and cooling are crucial for heavy-duty hypoid gear applications. The lubricant should have sufficient viscosity, load-carrying capacity, and thermal stability to provide proper film thickness and reduce friction and wear. Effective cooling systems, such as oil circulation or forced-air cooling, may be necessary to dissipate heat generated by high torque and loads.
- Heat Treatment: Heat treatment processes like carburizing or induction hardening can enhance the hardness and fatigue resistance of hypoid gears. These treatments increase the surface hardness and provide a tough core, enabling the gears to withstand heavy loads and resist wear and fatigue failure.
- Robust Gearbox Design: The design of the gearbox or gear system should consider the overall load path and distribution. Robust housings, shafts, and support structures should be designed to handle the high torque and loads encountered. Structural analysis and finite element methods can be employed to ensure the gearbox design can withstand the applied forces.
- Rigorous Testing and Analysis: Rigorous testing, such as load testing, endurance testing, and vibration analysis, is essential to validate the performance and durability of hypoid gears in heavy-duty applications. These tests help identify potential weaknesses, optimize the design, and ensure the gears meet the required specifications.
- Maintenance and Inspection: Regular maintenance and inspection are crucial to ensure the continued performance of hypoid gears in heavy-duty applications. Periodic inspections, lubricant analysis, and gear condition monitoring can help identify any signs of wear, misalignment, or other issues that may affect gear performance and reliability.
It’s worth noting that heavy-duty applications can vary widely, and specific considerations may differ based on factors such as industry, equipment type, and operating conditions. Consulting with experienced gear designers, engineers, and manufacturers who specialize in heavy-duty applications can provide valuable insights and guidance for optimizing the performance and longevity of hypoid gears in such scenarios.