Manufacturing tolerances play a critical role in the performance of worm gear. Tight control over tolerances ensures optimal meshing, load distribution, and overall efficiency of worm gear system. Here’s a detailed look at the impact of manufacturing tolerances on worm gear performance:
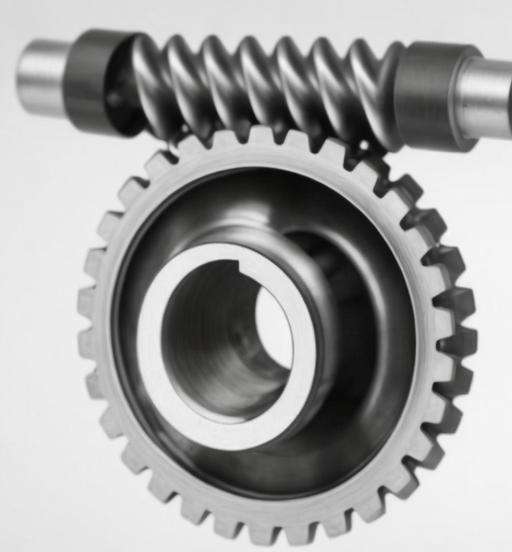
Key Performance Aspects Affected by Manufacturing Tolerances
- Meshing and Contact:
- Tight Tolerances: Precise tolerances ensure that the worm and wheel teeth mesh accurately, leading to smooth and consistent contact. This reduces vibration, noise, and wear.
- Loose Tolerances: Poor control over tolerances can result in misalignment and improper meshing, causing increased friction, noise, and uneven wear.
- Load Distribution:
- Optimal Load Distribution: Accurate manufacturing tolerances lead to uniform load distribution across worm gear teeth. This enhances load-carrying capacity and reduces localized stress, extending worm gear’s lifespan.
- Uneven Load Distribution: Inconsistent tolerances can cause uneven load distribution, leading to premature wear and potential gear failure.
- Efficiency:
- High Efficiency: Precise tolerances minimize backlash and ensure smooth engagement, leading to higher efficiency and lower energy losses.
- Low Efficiency: Loose tolerances increase backlash and friction, reducing the overall efficiency of the worm gear system.
- Noise and Vibration:
- Reduced Noise and Vibration: Tight tolerances result in better alignment and smoother operation, minimizing noise and vibration.
- Increased Noise and Vibration: Poor tolerance control leads to misalignment and irregular meshing, increasing noise and vibration levels.
- Heat Generation:
- Minimal Heat Generation: Proper tolerances ensure smooth contact and reduced friction, minimizing heat generation and maintaining optimal operating temperatures.
- Excessive Heat Generation: Loose tolerances increase friction, leading to higher heat generation, which can affect lubricant performance and gear longevity.
Specific Tolerance Considerations
- Tooth Profile Tolerances:
- Involute Profiles: Maintaining tight tolerances on the involute profile of the teeth ensures proper meshing and load distribution.
- Helix Angle: Accurate control of the helix angle is essential for smooth engagement and reducing axial thrust loads.
- Pitch and Lead Tolerances:
- Pitch Accuracy: Precise control of the pitch ensures consistent tooth spacing, which is crucial for smooth operation.
- Lead Tolerance: Accurate lead tolerances ensure that the worm progresses uniformly along its axis, preventing misalignment and uneven wear.
- Surface Finish:
- Smooth Surface Finish: Achieving a fine surface finish on worm gear teeth reduces friction and wear, enhancing efficiency and longevity.
- Rough Surface Finish: Poor surface finish increases friction and noise, reducing the performance and lifespan of worm gear.
Manufacturing Techniques for Tight Tolerances
- Advanced Machining:
- CNC Machining: Using computer numerical control (CNC) machines allows for high precision and repeatability in gear manufacturing.
- High-Precision Grinding: Grinding processes can achieve tight tolerances and smooth surface finishes on worm gear teeth.
- Quality Control:
- Inspection Systems: Implementing automated inspection systems ensures that each gear meets stringent tolerance requirements.
- Non-Destructive Testing: Techniques like ultrasonic testing and laser scanning can detect deviations and ensure compliance with tolerance specifications.
- Material Selection and Treatment:
- Stable Materials: Using materials with minimal thermal expansion and high dimensional stability ensures that tolerances are maintained under operational conditions.
- Heat Treatment: Proper heat treatment processes like carburizing or nitriding can enhance material properties and ensure dimensional accuracy.
Impact of Tolerance Deviations
- Backlash and Lost Motion:
- Excessive Backlash: Loose tolerances increase backlash, leading to lost motion and reduced precision in applications requiring high positional accuracy.
- Minimized Backlash: Tight tolerances minimize backlash, ensuring precise control and smooth operation.
- Durability and Maintenance:
- Reduced Durability: Deviations from specified tolerances can lead to increased wear and the need for frequent maintenance.
- Enhanced Durability: Maintaining tight tolerances improves durability, reducing maintenance requirements and operational downtime.
By maintaining strict control over manufacturing tolerances, worm gear systems can achieve optimal performance, reliability, and longevity, ensuring efficient operation in demanding applications.