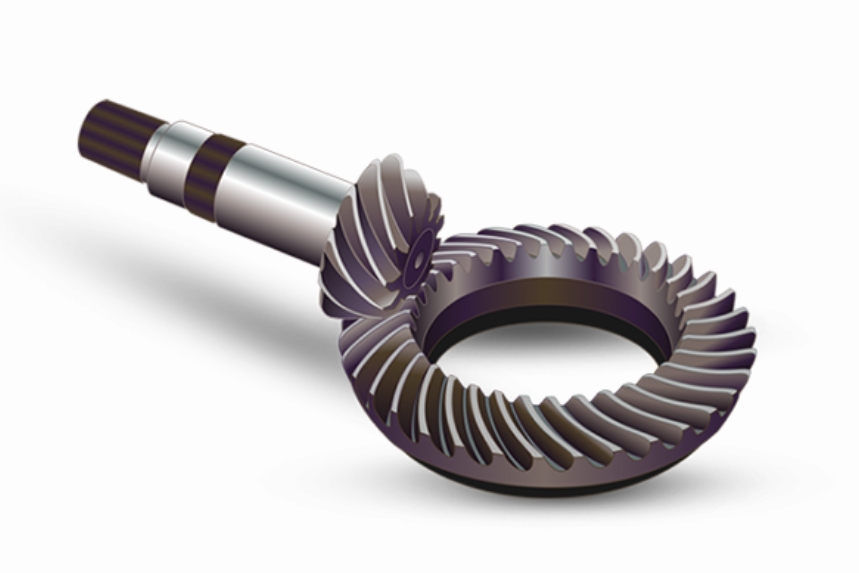
Implementing lean manufacturing principles in the production of spiral bevel gears at ZHY Gear Manufacturing can lead to significant improvements in efficiency, cost reduction, and product quality. Lean manufacturing focuses on eliminating waste, optimizing processes, and continuously improving production practices. Here’s how lean principles can be effectively implemented in the production of spiral bevel gears:
1. Value Stream Mapping (VSM)
- Identify and Analyze: Start by creating a value stream map for the production of spiral bevel gears. This tool helps identify all the actions (both value-added and non-value-added) currently involved in the manufacturing process from raw material to finished product delivery.
- Eliminate Waste: Use VSM to pinpoint areas of waste such as excessive inventory, waiting times, unnecessary transport or motion, overproduction, over-processing, defects, and underutilized talent.
2. 5S Methodology for Workplace Organization
- Sort, Set in Order, Shine, Standardize, Sustain: Implement the 5S system to organize and manage the production environment effectively. This includes keeping only necessary items in the work area, arranging tools and materials for easy access, maintaining cleanliness, standardizing best practices, and creating routines to keep discipline.
- Efficiency and Safety: Improved organization reduces time spent searching for tools or materials, minimizes clutter which can lead to errors or accidents, and establishes a more efficient, safer workplace.
3. Just-In-Time (JIT) Production
- Reduce Inventory Levels: Implement JIT to minimize inventory, which reduces the cost of storage and risk of obsolescence or damage to components and materials.
- On-Demand Production: Develop systems to produce spiral bevel gears as they are needed, not before. This requires accurate demand forecasts and quick setup times to respond flexibly to customer orders.
4. Kaizen (Continuous Improvement)
- Employee Involvement: Encourage workers at all levels to contribute ideas on how to improve processes. This involves regular brainstorming sessions and improvement workshops.
- Small, Incremental Changes: Focus on continuous small improvements to processes and productivity, rather than large-scale changes, which can lead to significant cumulative benefits over time.
5. Jidoka (Autonomation)
- Automation with a Human Touch: Implement technology that automatically stops the production line when issues are detected. For spiral bevel gear manufacturing, this could mean using CNC machines with sensors that detect and correct machining errors or stop the machine for tool changes.
- Prevent Defects: Jidoka helps in ensuring that defects do not pass to the next stage of the production process, thereby improving overall quality and reducing rework.
6. Poka-Yoke (Mistake-Proofing)
- Error-proofing Methods: Incorporate design modifications or develop tooling that prevents errors in the assembly or machining of spiral bevel gears. For example, design fixtures that only allow parts to be held in the correct orientation for machining.
- Quality at the Source: Ensure that each operator is responsible for the quality of their output and has the tools and authority to halt production if quality issues are detected.
7. TPM (Total Productive Maintenance)
- Machine Maintenance: Develop a comprehensive maintenance program where operators are trained to perform routine maintenance. This prevents machine breakdowns and downtime, which are critical for JIT and overall productivity.
- Predictive Maintenance: Use data and predictive analytics to anticipate and prevent equipment failures before they occur, thereby minimizing unplanned downtime.
Implementing these lean manufacturing principles in spiral bevel gear production not only optimizes the manufacturing process but also aligns with broader business goals of reducing costs, enhancing quality, increasing customer satisfaction, and improving employee engagement. These changes can transform ZHY Gear Manufacturing into a more agile, efficient, and competitive player in the gear manufacturing industry.