Improving efficiency and reducing costs in gear manufacturing are critical goals for staying competitive in a demanding market. Strategies to achieve these objectives span across technological innovation, process optimization, and management practices. Here’s an overview of key approaches to enhance efficiency and minimize costs in the gear manufacturing process:
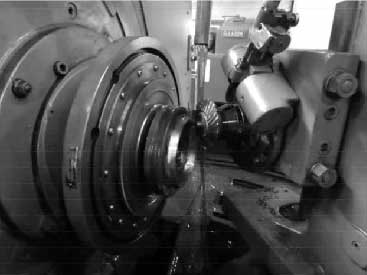
1. Adoption of Advanced Manufacturing Technologies
- CNC Machining and Automation: Employing CNC (Computer Numerical Control) machines and automation in the production process enhances precision and reduces labor costs. Automated loading and unloading systems, as well as robotic assembly lines, can significantly increase production speed and consistency.
- Additive Manufacturing: Integrating additive manufacturing (3D printing) for prototyping and production of complex gear geometries can reduce waste material and shorten development cycles, lowering both time and cost.
- Advanced Inspection and Quality Control: Utilizing AI-powered inspection systems and machine vision technology for quality control can detect defects early, reducing waste and rework.
2. Process Optimization and Lean Manufacturing
- Lean Manufacturing Principles: Implementing lean manufacturing principles helps in identifying and eliminating waste throughout the production process, improving overall efficiency and reducing costs.
- Process Integration: Integrating multiple manufacturing steps into a single operation, where feasible, can reduce handling time, decrease work-in-progress inventory, and shorten cycle times.
- Flexible Manufacturing Systems (FMS): FMS allows for the efficient production of small batches of custom gears, reducing setup times and enhancing the ability to respond quickly to changing customer demands.
3. Material Optimization
- Material Selection: Careful selection of materials based on performance requirements and cost can lead to significant savings. High-performance alloys may offer better longevity but at a higher initial cost, whereas more cost-effective materials might be suitable for less demanding applications.
- Efficient Use of Materials: Techniques such as near-net-shape manufacturing minimize material waste, and recycling of scrap metal can further reduce material costs.
4. Supply Chain and Inventory Management
- Just-in-Time (JIT) Inventory: Adopting JIT inventory practices reduces storage costs and minimizes the risk of material obsolescence.
- Supplier Relationships: Developing strong relationships with suppliers can lead to better pricing, improved material quality, and more reliable delivery schedules, contributing to smoother production flows and cost savings.
5. Workforce Development and Management
- Skill Development: Investing in employee training and development enhances efficiency and reduces errors. A skilled workforce can better operate advanced machinery and adapt to new technologies.
- Employee Engagement: Engaging the workforce in continuous improvement processes can lead to innovative ideas for efficiency improvements and cost reduction.
6. Energy Efficiency and Sustainability Practices
- Energy-Efficient Machinery: Investing in energy-efficient machines and lighting can significantly reduce utility costs.
- Sustainable Practices: Implementing sustainable manufacturing practices, such as waste recycling and minimizing energy consumption, not only reduces environmental impact but can also lower operating costs.
Conclusion
Enhancing efficiency and reducing costs in gear manufacturing requires a comprehensive approach that includes technological innovation, process improvement, and effective management strategies. By adopting advanced manufacturing technologies, optimizing processes, and focusing on sustainability, manufacturers can improve their competitive edge, offer better prices to their customers, and ensure long-term profitability. Continuous improvement and adaptation to new technologies and market demands are key to achieving success in the dynamic field of gear manufacturing.