The gear manufacturing process is a complex and intricate journey from concept design to the final delivery of a product. It involves multiple steps, each critical to ensuring that the gears meet the required specifications and performance standards. Let’s explore the complete process of gear manufacturing, highlighting key stages and considerations.
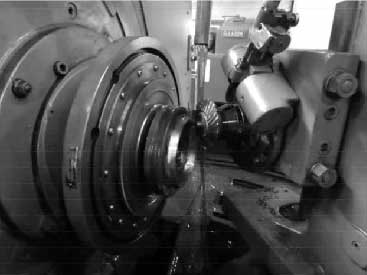
1. Design and Engineering
- Conceptualization: The process begins with understanding the application’s needs, including load, speed, environment, and space constraints. This stage defines the basic requirements for the gear manufacturing.
- Design: Utilizing CAD (Computer-Aided Design) software, engineers design the gear’s geometry, specifying dimensions, tooth profile, material, and other critical features.
- Simulation: Through FEA (Finite Element Analysis) and other simulation tools, the design is tested under virtual conditions to predict performance and identify potential issues.
- Prototyping: Rapid prototyping, often through additive manufacturing, allows for the physical testing of designs to validate simulations and make necessary adjustments.
2. Material Selection and Preparation
- Material Selection: Based on the gear’s application, materials are selected for their strength, durability, and resistance to wear and environmental conditions.
- Preparation: Raw materials are prepared for manufacturing, which may include casting, forging, or procuring pre-formed stock for machining.
3. Manufacturing Processes
- Machining: Using CNC machining centers, the gear blank is cut to the approximate shape. This step may involve turning, milling, or drilling.
- Gear Cutting: Specific gear-making operations like hobbing, shaping, or broaching are used to form the gear teeth with precision.
- Heat Treatment: Processes such as carburizing, nitriding, or induction hardening are applied to improve the gear’s hardness and wear resistance.
- Finishing: Additional machining processes, grinding, or honing are performed to achieve the final dimensions and surface finishes.
- Coating: If required, surface coatings are applied for extra wear resistance or to reduce friction.
4. Quality Control and Inspection
- Dimensional Inspection: Gear manufacturing is inspected for dimensional accuracy using micrometers, calipers, and gear measurement machines.
- Material Inspection: Material properties, including hardness and microstructure, are verified to ensure they meet specifications.
- Performance Testing: Gear manufacturing may undergo performance testing under simulated or actual operating conditions to validate their functionality and durability.
5. Assembly and Integration
- Assembly: If the gear manufacturing is part of a larger system, it may be assembled with other components to form a gearbox or drive assembly.
- Integration Testing: The complete assembly is tested to ensure it operates correctly within the intended application, meeting all performance criteria.
6. Packaging and Delivery
- Packaging: Gears or assemblies are carefully packaged to prevent damage during transportation.
- Delivery: Finished products are delivered to the customer, along with documentation including quality assurance certificates and maintenance guides.
7. Post-Delivery Support
- Installation Support: Manufacturers may offer guidance or services to assist with the correct installation of the gear or gearbox.
- Maintenance and Repair Services: Ongoing maintenance support ensures the gear’s longevity and performance, including repair services or providing spare parts.
Conclusion
The gear manufacturing process is a detailed and coordinated effort that requires precision at every step. From initial design and material selection to final quality control and delivery, each phase contributes to the overall performance and reliability of the final product. Advancements in technology and materials science continue to refine and improve this process, allowing for the development of gears that meet increasingly demanding requirements in terms of efficiency, durability, and cost-effectiveness.