Bevel angle of preform of spiral bevel gear α It has a great influence on the filling fullness of tooth profile and the size of forming force. Taking the preform cone angle as the research object, the numerical simulation analysis is carried out to observe the influence law of the change of preform cone angle on metal forming.
As shown in Figure 1, when the cone angle of the preform of spiral bevel gear is too small, the metal material fills the die tooth cavity under the action of extrusion force. First fill the small end of the die tooth cavity, and then fill the large end of the die tooth cavity. Due to the insufficient axial flow of metal material, the large end of the die tooth cavity is very easy to be filled. The light colored area is the phenomenon that the large end of the tooth shape is not fully filled.
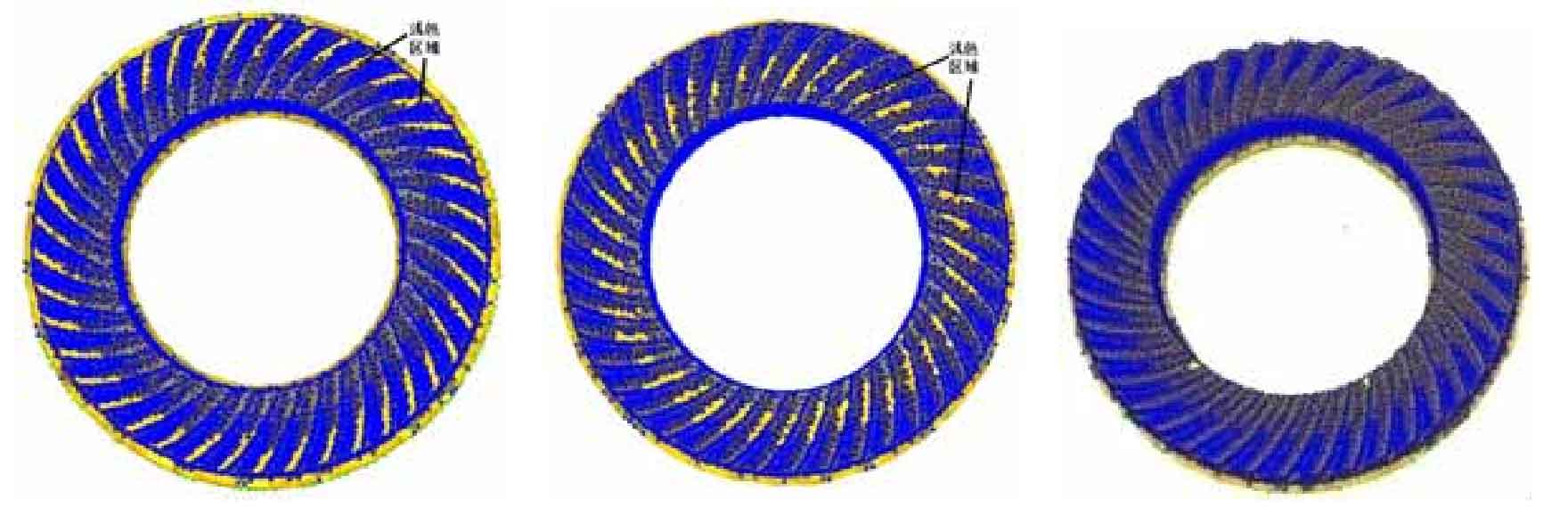
As shown in Figure 2, when the cone angle of the preform of spiral bevel gear is too large, the metal material first contacts the large end of the concave die tooth shape, and then contacts the small end of the concave die tooth shape with the continuous increase of the pressing amount. Due to the rapid radial flow of metal material, when the large end and small end of the concave die tooth shape are fully filled, the middle part of the tooth shape cannot be filled in time, resulting in depression in the middle part, and the flow of metal is limited, At this time, more extrusion force is needed to force the metal material to flow downward, which is enough to fill the tooth cavity. Light colored areas are not filled in the middle.
As shown in Fig. 3, when the cone angle of the preform of spiral bevel gear is properly selected, at the end of the forming, the metal material can fill the large and small ends of the tooth shape of the female die at the same time, and the forming quality is good.
Figure 4 shows the cone angle of preform α= 110 ° and α= The relationship curve between forming force and stroke at 155 °. According to the relationship curve, the precision forging process of spiral bevel gear has three important stages.
The first stage is the initial stage. The blank of spiral bevel gear is in contact with the convex concave die, and the deformation area of metal material is mainly concentrated in the contact part. With the gradual increase of the pressing amount of the convex die, the metal material flows to the tooth cavity of the concave die. At this stage, the forming force shows a slow upward trend, with a small increase.
The second stage is the tooth profile forming stage of spiral bevel gear. At this stage, the metal material continues to flow to the tooth cavity of the female die to form the spiral umbrella tooth shape. Due to the obstruction of the tooth cavity of the female die, its stress is mainly concentrated in the tooth shape. The forming force at this stage increases rapidly.
The third stage is the local filling stage. Metal materials are mainly used to fill the unfilled part in the mold cavity to ensure fuller filling of the tooth shape. At this stage, the forming force rises very rapidly and reaches the maximum forming load at the end of the tooth formation of the spiral bevel gear.
Bevel angle of preform of spiral bevel gear α= 110 ° and α= The maximum forming load of 155 ° at the end of forming tooth profile is 8545kn and 7823kn respectively. From the results, it can be seen that the cone angle of spiral bevel gear preform has a great influence on the forming force.
Fix the internal and external diameter dimensions of spiral bevel gear preform. When the internal shunt gap is 5mm and the external shunt gap is 4mm, under the condition of ensuring full filling of tooth cavity, the change law curve of the influence of bevel angle of spiral bevel gear preform on forming force is obtained through numerical simulation, as shown in Fig. 5.
It can be seen from the forming force curve in Figure 5 that too large or too small cone angle has a great impact on the forming force, and the cone angle of spiral bevel gear preform α In the range of 140 ° ~ 150 °, the big end and middle part of the gear can be filled at the same time, and the forming force is the smallest, about 7300kn. Therefore, under the condition of ensuring the forming quality, a more appropriate preform cone angle should be selected to reduce the forming force on the one hand and improve the service life of the die on the other hand.