Linear modification is adopted with the modification quantity of 0.022m m and the length of 2.8m M. Fixed torque of 1500N.m, 2000N.m, 2500N.m, 3000N.m and 3500N.m are applied to gear 1 respectively.The engagement stiffness and load distribution coefficient between teeth are shown in the figure under the above five torques.
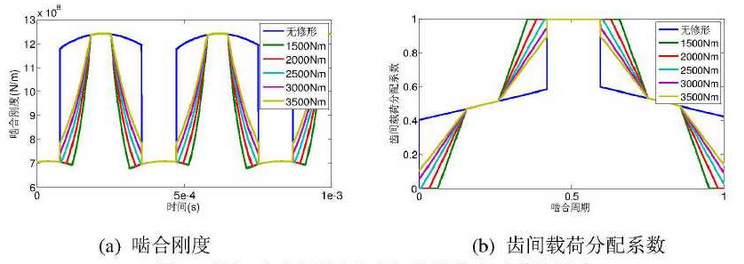
As can be seen from Fig. a, when the input torque is less than the average engine torque of 2500N.m, with the decrease of the torque, the proportion of time occupied by single-tooth engagement gradually increases in a single engagement cycle, the engagement degree of gears gradually decreases, and the steep change of engagement rigidity gradually increases.When the input torque is greater than the average engine torque, the steep change in engagement stiffness increases with the increase of the torque, although the coincidence remains unchanged.It can be seen from Figure B that when the torque is less than the average engine torque, the load distribution coefficient between teeth is 0 and the gear is in single-tooth engagement state in a single engagement cycle in the area near the entry and exit engagement.When the torque is greater than the average engine torque, the sudden change of gear load becomes more and more obvious by further increasing the input torque.
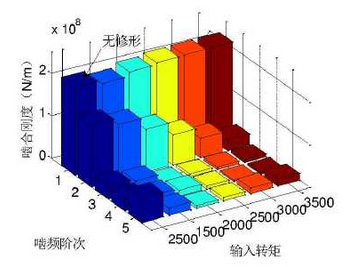
Under different torques, the corresponding amplitude of the first five-order meshing frequency is shown in the figure. It can be seen from the figure that the corresponding amplitude of the first-order meshing frequency increases gradually and that of the second-order meshing frequency decreases gradually with the increase of input torque for the modified gear.Combining the analysis results, it can be seen that the variation trend of meshing stiffness and load distribution coefficient between teeth with increasing input torque is opposite to that with decreasing profile.
In conclusion, from the analysis results under quasi-static conditions, in order to effectively ease the sharp change of meshing stiffness caused by alternation of single and double teeth, to realize the smooth transition of load change during gear transmission and to ensure the overlap of gears, the amount of modification should be the amount of deformation at the highest point of single teeth meshing under a fixed design load, and the selection of modification length should satisfy the entire area of double teeth meshing area.In the modification area, since the modification type mainly affects the curve form of meshing rigidity and load variation in the modification area, the degree of difficulty in machining the modification type should be considered and the type of modification that is easy to machine should be selected.
At the same time, the profile modification parameters and external loads have a great influence on the corresponding amplitudes of each order of meshing frequency of meshing stiffness.Previous studies have shown that the dynamic characteristics of gear drive system are sensitive to the variation of amplitude corresponding to meshing frequency of each order of meshing stiffness, which indicates that profile modification will inevitably affect the dynamic characteristics of gear drive system.