Linear shape modification is adopted with the length of 2.8mm and the value range of modification is [0.01mm, 0.09mm]. The interval between values is 0.02mm.The average engine torque of 2500N.m is applied to gear 1. The influence of modification on meshing stiffness and load distribution coefficient between teeth is shown in the figure.It can be seen from the diagram that the profile modification eases the dramatic change of meshing rigidity of gears when single and double teeth alternate, and the change of profile modification does not affect the meshing rigidity of double teeth meshing area.
When the amount of modification is 0.01mm, the time proportion of single tooth engagement and the overlap degree of gears will not change in a single engagement cycle.When the amount of modification exceeds CH (greater than 0.022m), further increasing the amount of modification will result in an increase in the proportion of time occupied by single-tooth engagement, a decrease in gear overlap and a sharp increase in meshing stiffness in a single meshing cycle.At the same time, it can be seen from the drawing that when the amount of modification exceeds CH, the load distribution coefficient between teeth in the area near the entry and exit engagement of the gear is 0, which indicates that the gear is in single-tooth engagement state. With further increase of the amount of modification, the sudden change of gear load becomes more and more obvious.
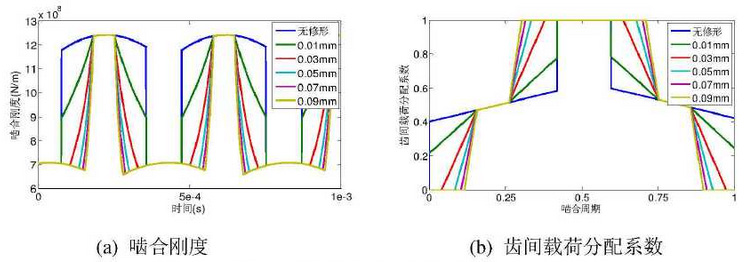
The above analysis shows that under quasi-static condition, when the amount of modification exceeds the deformation at the highest point of single-tooth engagement under a constant design load, further increase of the amount of modification will result in a reduction of gear overlap, and at the same time, the meshing rigidity and load sudden change will gradually increase when the single-tooth and double-tooth alternate.
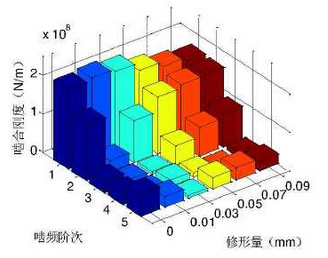