Innovative design techniques for helical gear systems focus on improving efficiency, reducing noise, increasing load capacity, and extending the lifespan of helical gear. These advancements are crucial in industries such as automotive, aerospace, and heavy machinery, where the performance and reliability of helical gear systems are critical. Here’s an overview of some innovative techniques:
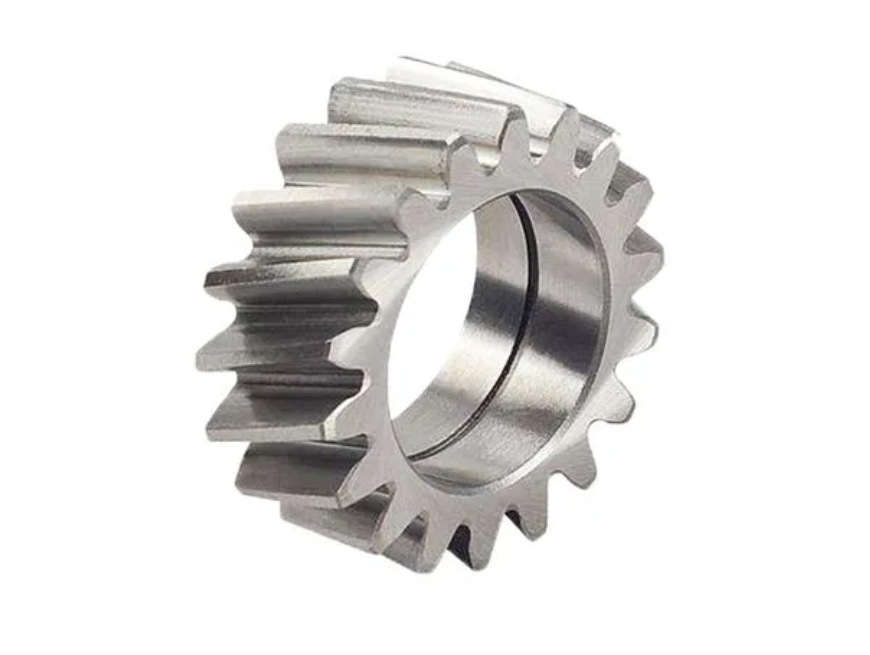
1. Advanced Materials
- High-Performance Alloys: Use of stronger, lightweight materials like titanium or advanced steel alloys can increase strength and reduce weight.
- Composite Materials: Incorporating composites can reduce weight and improve thermal properties.
2. Precision Manufacturing
- Computer Numerical Control (CNC) Machining: Ensures high precision in helical gear manufacturing, crucial for maintaining exact helix angles and tooth geometry.
- 3D Printing/Additive Manufacturing: Allows for complex geometries, potentially reducing weight and optimizing design for specific applications.
3. Surface Treatments
- Surface Hardening: Processes like case hardening or nitriding increase surface strength, leading to higher resistance to wear and tear.
- Coating Techniques: Applying coatings like diamond-like carbon can reduce friction and increase durability.
4. Innovative Tooth Design
- Modified Tooth Profiles: Optimizing the shape of the teeth for specific applications can lead to better load distribution and reduced noise.
- Variable Helix Angles: Designing helical gear with variable helix angles along the tooth length can balance the trade-off between strength and noise.
5. Noise Reduction Techniques
- Micro-Geometry Adjustments: Fine-tuning tooth surface geometry can significantly reduce noise and vibration.
- Sound Dampening Materials: Incorporating these materials into helical gear housing can further reduce noise.
6. Enhanced Lubrication Systems
- Advanced Lubricants: Using lubricants with better properties can reduce friction and wear.
- Lubrication Delivery Systems: Optimized delivery systems ensure consistent lubrication, especially in high-stress areas.
7. Computer-Aided Engineering (CAE)
- Finite Element Analysis (FEA): Used to simulate and analyze the stress distribution and predict the lifespan of helical gear components.
- Computational Fluid Dynamics (CFD): Helps in understanding and optimizing the flow of lubricants within helical gear system.
8. Integration with Smart Technologies
- Sensors and Monitoring Systems: Embedding sensors to monitor gear performance, wear, temperature, and lubrication in real-time.
- Predictive Maintenance: Utilizing data analytics and AI to predict and prevent gear failures.
9. Eco-Friendly Design Considerations
- Lifecycle Analysis: Designing helical gear with consideration for their entire lifecycle to minimize environmental impact.
- Recyclable Materials: Using materials that are easily recyclable to reduce waste.
Applications
These innovative design techniques are applied in various sectors such as:
- Automotive: For more efficient and quieter transmissions.
- Aerospace: Where weight and reliability are critical.
- Wind Turbines: Enhancing efficiency and lifespan in power generation.
- Industrial Machinery: For improving performance and reducing maintenance costs.
In conclusion, these innovative design techniques for helical gear systems aim to optimize performance, efficiency, and durability while addressing specific challenges such as noise, weight, and environmental impact. As technology advances, these techniques continue to evolve, offering more sophisticated solutions in helical gear system design.