High power gear transmission mainly adopts wide helical gear transmission, which has complex form and structure, large load and high precision requirements. Heavy load helical gear transmission teeth produce large deformation and stress, which have an obvious impact on the dynamic characteristics. The test cost is expensive and the design cost is high. The use of numerical models to accurately predict the load distribution, helical gear transmission error and other important data can reduce the helical gear design cost, especially the test cost in the real environment. When the helical gear rotates, the position of conjugate tooth profile and the number of meshing teeth change constantly. The meshing stiffness and load distribution are the position functions of meshing helical gear pairs. Based on the linear elasticity theory, AGMA and ISO adopt a simplified equation, which considers that the load is uniformly distributed along the contact line. The bending deformation of helical gears is calculated by using this pseudo design without considering the tooth surface friction, and the calculation result is not very accurate. It is very important to accurately calculate the load distribution on the contact line of the helical gear pair, and then calculate the meshing deformation and time-varying meshing stiffness of the helical gear pair.
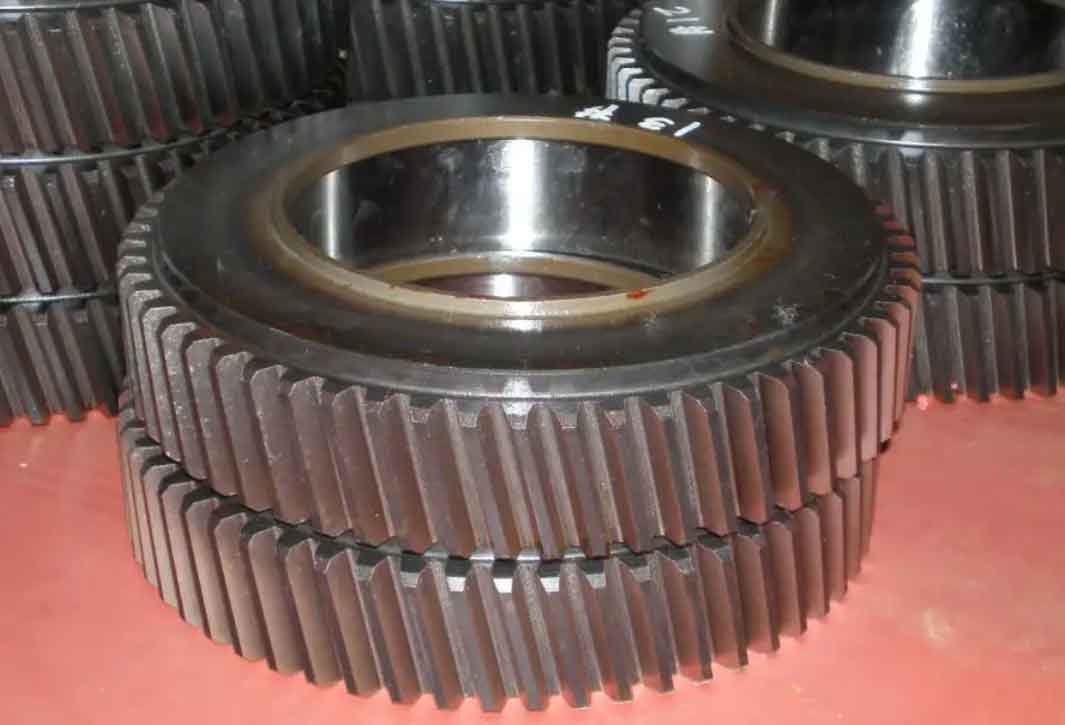
Based on the principle of minimum elastic potential energy, the load distribution model is established to calculate the load distribution between helical gears. The elastic potential energy of helical gears is a function of the position of the tooth profile at the instantaneous contact point. The load distribution between spur gears can be obtained by dealing with the whole minimum elastic potential energy. The helical gear can be treated as a thin straight gear of unit length. The load distribution along the time-varying contact line of the helical gear is given by integrating the elastic potential energy of the meshing point along the contact line. On this basis, the meshing deformation of the helical gear along the time-varying contact line is analyzed by considering the tooth surface friction. The time-varying meshing stiffness of helical gear is calculated by using the change law of time-varying contact line and the meshing deformation of nodes on the contact line. The bending torsion shaft coupling dynamic equation of helical gear transmission with tooth surface friction is established, and the sensitivity of the time-varying meshing stiffness of helical gear to the vibration displacement of the driving and driven wheels is given.
According to the principle of minimum energy, the theoretical model of load distribution along the contact line of involute helical gear is given. Considering the tooth surface friction, the meshing deformation and time-varying meshing stiffness of helical gear are analyzed, and the following conclusions are obtained:
- according to the calculation of time-varying contact line load distribution, the maximum time-varying contact line load occurs at the node. The load distribution of the helical gear along the contact line is smoother than that of the spur gear, and there is no sudden load change, which also shows that the helical gear runs smoothly and has less vibration noise than the spur gear.
- the influence of tooth surface friction is considered in the calculation of tooth deformation. The analysis results show that: due to the change of friction direction of the node, there is a large deformation mutation near the node. The meshing stiffness calculated when considering the tooth surface friction is larger than that when not considering the friction, and the increase of the meshing stiffness has a significant impact on the increase of the axial vibration displacement of the helical gear.